Pressing matters at Gilberts
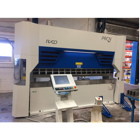
Gilberts Blackpool, Britain’s leading independent air movement specialist, has further expanded its fabrication capacity with the installation of a new press brake. The new machinery doubles Gilberts’ capability to bend sheet metal at its 90,000 sq ft headquarters, and compliments the addition already this year of a new laser cutter.
Explained Gilberts’ Sales Director Ian Rogers. “The press brake works hand-in-hand with the laser cutter, one giving us faster, more accurate cutting of metal, the other processing what has been cut.
“We are seeing growing demand for our products that use sheet metal, particularly our innovative MFS hybrid stand-alone solution, that was the first of its kind when we launched it less than a year ago. The growth is such that, to meet demand, we need to invest in technology to give us enhanced productivity, with accuracy, to ensure that our customer service remains at the high levels we historically deliver for our clients.”
The new Rico press brake automatically calculates angle and force, and has the capability to bend sheet at multiple points in one process. It is claimed to reduce wastage from deformation during processing by up to 60%. It will help manufacture not only Gilberts’ MFS units, but a variety of its penthouses, swirls, diffusers, louvres and dampers.