Closed systems need careful commissioning
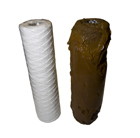
James Townley explains why commissioning is so important for closed heating or cooling systems, and offers advice on the approaches that can help ensure effective long-term operation right from the start.
Commissioning is a critical stage in the life of a closed heating or cooling system. Failure to manage water quality during the transition from initial cleaning to project completion impacts on the success of the commissioning process and, potentially, the longer-term operation of the system.
The commissioning engineer is required to put into service a diverse range of equipment and provide accurate and repeatable measurements to demonstrate correct operation. Modern systems utilise components of increasingly small internal bore, low velocity or sensitive internal mechanisms. Probes and sensors, linked to the BMS system, are essential to their efficient operation and integration. It is these components and controls that ultimately provide the future operating efficiency of the system, but are especially susceptible to poor water quality.
In some cases, key components will be protected by in-line strainers. Pumps are perhaps the most common example, but protection may also be required for heat exchangers in boilers, CHPs, chillers and heat pumps. Small, fine mesh strainers are also commonly employed in terminal units, such as heat interface units (HIUs). Protecting these strainers from blockage is a priority in the commissioning phase.
The requirements for the initial cleaning of systems, and subsequent management and testing regimes are extensively covered in the BSRIA Guides (BG 29 Pre-commission cleaning of pipework systems; BG 50 Water treatment for closed heating and cooling systems) and this commonly forms the basis of the specification for water treatment.
However, there may be additional requirements imposed by manufacturers, industry standards or clients, which demand more stringent standards be maintained. For example, a boiler or CHP warranty may adopt the VDI 2035 standard, requiring oxygen, dissolved metals and water hardness to be maintained at levels well below those accepted under BSRIA guidelines.
Maintaining water quality during the commissioning phase presents a unique set of challenges. Water exchange must always be rigorously controlled. Quick-fill loops should be removed by this point and top-up via pressurisation units monitored by water meters or BMS feedback. Any ingress of fresh water will dilute the established water treatment and may introduce oxygen, hardness and bacteria.
Circulation at suitable velocity must be maintained in all areas. Circuits requiring temporary isolation must be monitored as separate systems and measures put in place for periodic circulation and testing prior to reconnection to the core system.
Initial inhibitor and biocide dosing may be based on estimated system volumes and levels may decline with water exchange or normal consumption of the product. Regular testing and adjustment will be required as commissioning progresses. In addition, systems will often be operating at ambient temperatures prior to full commissioning of heating and cooling plant, increasing the potential for bacterial growth.
Filtration
Deficiencies in the initial cleaning process, or a subsequent decline in water quality, will result in an elevated particle load. This presents the greatest risk to effective commissioning, as even low levels of fine material can build up on narrow valve apertures or strainer surfaces and disrupt low velocity flow readings.

In-line settlement type devices may assist where higher levels of dense particulates are present, but are less effective on the finer, lighter material characteristic of systems post pre-commission cleaning.
There has been an increased uptake of side stream filtration to overcome these issues. Indeed, there are progressive cleaning strategies now being employed which replace traditional flushing with mains water and clean entirely by side stream filtration, vastly reducing water consumption and limiting ingress of undesirable elements.
Where a conventional cleaning method has been employed, side stream filtration allows flushing to be halted sooner, before continuing to polish the water and deliver the required suspended solids targets. It is possible to effectively filter to < 5 microns and an overall suspended solids level of < 2 mg/l. (BSRIA guideline < 30 mg/l).
Cartridge type filters are commonly employed in the temporary phase, as filtration can be achieved to any desired level with relatively simple equipment. Maintenance requirements are high, often requiring more than one cartridge change in 24 hours, and this needs to be undertaken by the resident water treatment specialist during this stage.
Permanent side stream filters may be specified within the plantroom design and bringing these into service prior to commissioning should be considered. In some cases, these remain isolated with the intention of protecting them from the rigours of the initial cleaning, but this should not be necessary and is missing an opportunity to gain additional value and cost savings from their inclusion.
As the project moves through the commissioning phase, the management of the filtration system need to be determined. Intensive cartridge replacement is unlikely to be maintained and responsibility for this can be uncertain. A more modern approach is automated cleaning, which favours the media bed (sand filter) type approach. A regular backwashing interval appropriate for current water quality can be adopted, with options to alert the operator via BMS if any problems arise.
In summary, management of water quality during commissioning phase is a dynamic process, which requires the roles and responsibilities of several parties to be clearly defined. Taking full advantage of modern technologies to automate and monitor this process can significantly improve this process and yield cost savings for the project as a whole.
James Townley is head of technical sales for ENWA Water Technology UK