The ABC of EPCs
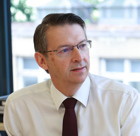
Dr Andrew Geens explains how building managers can help to ensure their EPC is accurate – and why that’s so important to update your EPC with MEES on the horizon.
EPCs for MEES? Yes, the correct metric. But don’t rely on an old EPC that was produced for sale or rent to comply with the Energy Performance of Buildings Regulations. This isn’t simply a case of creating business for EPC schemes. An up-to-date EPC provides an accurate assessment of your building’s potential energy performance – and should also give a good indication of where improvements could be made.
Of course, there are many questions flying around about EPCs. These include reservations about accuracy, which are important to address. There are three factors that influenced the accuracy of EPC’s in the early days of the scheme, and how these have been addressed over the past decade:
1. Competence of assessors
2. Human Error
3. Urgency and conventions
Competence
The qualifications and experience of EPC assessors are much improved from the early days of the scheme. In order to lodge an EPC, an assessor has to be on an approved register. And to be on an approved register the assessor either has to obtain a qualification or use the APEL process.
The qualification is quality controlled by Ofqual, but no previous experience is required to take the qualification. Most people producing EPCs now qualified before 2012, so have at least five years’ experience.
The APEL route (Accreditation of Prior Experiential Learning) is quality controlled by DCLG (Department of Communities and Local Government) and provides a route to registration for those with previous energy surveying experience. Whichever route to registration is taken, DCLG also requires ongoing maintenance of competence through CPD and auditing of lodged EPCs. One register operator additionally operates their register with UKAS accreditation (ISO 17024).
It is therefore reasonable to expect that the overall competence of the EPC assessor pool is better now than it has been in the past and is continually improving. The combination of CPD and auditing should mean that most mistakes in EPCs now are simply down to human error.
Human error
Even competent, experienced EPC assessors will be prone to human error and the ongoing audit regime is designed to manage this risk. The more complex a building, the more data required for the EPC production process and therefore the greater the risk of human error. There are many contributory factors leading to human error, but one routinely implicated with EPC production is rushing the task.
It is less the case now, as the property industry is more accustomed to the need for an EPC on sale of a property. In the past however, and still now occasionally, an EPC is procured in a hurry when a client wants a quick property sale. An EPC assessor is more likely to make errors, or be unable to find important data about the building, when working against a tight deadline.
Urgency and conventions
EPCs for existing buildings are a challenge. They were not built with EPC assessment in mind. Reliable information is often difficult to obtain, and here consistency takes over from accuracy. Fairly early in the development of EPCs it was decided that relying on assessor judgement in the absence of reliable evidence, (boiler efficiency or mechanical extract rates, for example), would lead to a situation where the EPC rating would be different depending on which assessor produced it.
To overcome this problem, EPC conventions were introduced on 1st June 2010. We are now on Issue 6, as they have been refined over time. The conventions are developed by representatives of the assessor register operators, with assessor representation a more recent addition, but are approved by DCLG. A key component of the conventions is the provision of default values where there is no reliable evidence. These defaults are intended to be a tool of last resort and are typically selected to represent a worst case to discourage their use. This logic is predicated on clients wanting the best possible EPC rating, thus motivating clients to source the information that the assessor requires.
So, EPCs procured a decade ago are unlikely to be as accurate as building owners would like when approaching the new MEES scheme. Even if there was no human error involved, the conventions and measurements of today’s Certificate assessments are very different. There is no blame attached to DCLG, EPC assessors or EPC clients in any of this, it is simply the case that the early EPC programme was not developed with MEES in mind.
Another important point is that although an EPC is valid, for the purposes of the EPB Regulations, for 10 years as permitted in complying with the Energy Performance of Buildings Directive, it is really only “accurate” on the day that it was produced. To exercise due diligence, even ignoring the points above, a new EPC would be advisable if any of the following have happened since the EPC was produced:
• Replacement of any controlled fittings (windows etc.) or controlled services (boilers etc.) as these will be better that those replaced.
• Low or zero carbon technologies have been installed (PV etc.).
• Efficiency data not used for the original EPC has been found.
• Changes to the calculation methodology are beneficial for your particular building, but note that changes could also have been detrimental. Seek advice on this from your EPC assessor.
• You have realised that the characteristics of your building mean that dynamic simulation modelling would give you a more accurate rating, but not necessarily better, where this wasn’t used for the original EPC. Again, seek advice from your EPC assessor.
In requesting an EPC now, clients should be aware that the information requested by their assessors, or more specifically an absence of the information, is going to have a detrimental influence on the EPC rating. In selecting an assessor, clients should be confident in any assessor on an approved register. In the interests of due diligence they could find out a little about any prospective assessor such as when they first registered as an EPC assessor and what other relevant qualifications or experience they have.
In conclusion, I hope that I have been able to explain that although an existing EPC may have been accurate on the day that it was lodged and was prepared perfectly correctly, following approved conventions, satisfying its purpose for the EPB Regulations, a second EPC produced today with MEES in mind is likely to be more accurate, although due to changes in the calculation methodology over the years, not necessarily better. Whether better or worse, MEES related decisions will be better and less risky, if you have more confidence in the accuracy of the EPC.
Dr Andrew Geens is head of CIBSE Certification