Get a head start with your controls
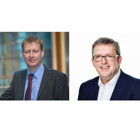
The commissioning of controls is beset with challenges, and yet with some forward-planning there are benefits for consultants, contractors and end-users. Karen Fletcher explores the issues with some of those at the front line.
Timing, as they say, is everything. And when it comes to commissioning controls and building management systems (BMS), that is certainly true. Engineers involved in commissioning know that there is never enough time to do the work, and controls are no different. But where controls commissioning is concerned, the ‘when’ is as important as the ‘how long’.
Ian Ellis, head of product management and marketing for Siemens Building Technologies, says: “It’s not just lack of time for commissioning that is the problem. Control systems take time to settle down, and if you carry out the work too soon you face a number of issues. For example, you’re not taking enough account of changing conditions during the day.”
Trend Controls’ marketing director Graeme Rees agrees: “Commissioning of controls really needs to be the last thing that’s done, because everything else needs to be in place for a proper system test. But of course, once you have waited, there is often very little time left to commission properly.”
Jon Kilpatrick, director of installation specialist Detail Design Engineering adds: “In an ideal world, controls would be commissioned after practical completion and time would be allocated for a controls specialist to commission the building to ensure it’s running correctly – in other words, that it’s operating as the occupier requires.”
TOP TIPS Controls commissioning • Time for commissioning controls will pay dividends in better building performance and feedback from occupants.• Do it at the right time – when other building services installations are complete and power to the building is available. This allows the system to be checked, vital with integrated services. • Put someone in charge of the process – ideally, an individual with knowledge of controls; or a client representative with power to enforce the process. • Use the controls system to help commission other areas of the building – technology is now available that offers a view of how other hvac equipment is performing. This supports more effective and timely commissioning of the whole project. |
Off to a bad start
It goes without saying that poorly- commissioned controls lead to all sorts of negative consequences. Jon Belfield, director of controls and BMS specialist InTandem Systems, and vice president of the Building Controls Industry Association (BCIA), says: “Poor commissioning of controls leads to energy inefficiency as well as shortened plant life due to unnecessary operation.
“There are less obvious issues such as the long-term impact of negative perceptions of occupants such as ‘our office has always been cold’ or ‘they’re still having problems’.
“These perceptions stick even after issues have been addressed and it can be hard to recover from the negativity,” he adds.
Ellis agrees with this point about occupant comfort: “Occupier wellbeing is a key factor for many building owners and tenants. This is partly a commissioning issue, as that has an effect on operation. Studies are showing that if staff don’t feel good in a building, that has a detrimental effect on output.”
And omitting controls commissioning is not simply a question of leaving the occupier with time clocks that aren’t set.
“A fire test should be done when the plant is running so that you can see that the fire systems such as alarms and fire dampers are all working as a system. I’ve have never seen that happen on site,” says Kilpatrick.
The problems with controls commissioning start at the specification stage. “Design engineers can’t be expected to be experts in everything, and we often find that specifications are very general,” says Rees.
He continues: “That’s not helpful because controls need a detailed specification, and it affects commissioning because we need to know what parameters we are commissioning to.”
Kilpatrick agrees and highlights contradictions within different parts of the specification that add to problems as a building project nears completion: “Contractors want to buy products with the most basic features as they are generally lower cost. But then the BMS specification may require a Modbus connection to that product. So, the controls engineers will fit that connection in the BMS, yet find that the specified product does not allow for that connection. You’re left with a cable dangling in mid-air and no one takes responsibility.”
Think integration
Belfield echoes this thought: “Packaged kit, with no provision for site commissioning, such as AHUs that work ‘out of the box’ cause problems at the commissioning stage. They seem like a good idea, but one size rarely fits all.”
Ellis agrees that in the age of integrated systems, the issue of controls commissioning is increasingly urgent: “Commissioning is particularly important where there is greater use of integration. Someone has to ensure that the system is functioning, and that all the equipment can operate smoothly together. If the integrations don’t work, that can lead to serious problems in performance.”
There is general agreement on what steps can be taken to ensure better controls commissioning. In a time-constrained project, there are quick wins that can help with long-term comfort and efficiency.
![]() |
|
|
Rees suggests ‘pre- commissioning’, saying: “Controls are not only about hardware, but software too. It seems simple, but it’s very important to ensure that the points in a BMS are all correctly installed through point- to-point checks, yet so often time to do that is not allocated on the build schedule.”
Steps for success
Ian Ellis agrees that simple steps can make a significant difference: “If the cooling is set to 21oC and the heating is also set to 21oC, the two systems fight against each other. This leads to energy waste and discomfort.
“Ensuring there are ‘dead zones’ so that heating and cooling work harmoniously is simple, but effective – yet so often overlooked,” he adds.
All agree that, in an ideal scenario, there will be a knowledgeable individual responsible for commissioning controls and the BMS.
“If a client does not have the know-how, they should take someone on to oversee the work. They should not rely on the builder or contractor, because it’s in their interest to hit a completion deadline, not necessarily to hand over a commissioned controls system,” says Kilpatrick.
It’s no surprise to find that where projects are based on teamwork, the commissioning outcomes are better. Graeme Rees cites the work that Trend’s Technology Centre partner Impact Control Systems carried out at the Manchester Town Hall redevelopment: “It was done very differently; it was very collaborative. The client led the team all the way to commissioning, with main contractor, mechanical and electrical sub-contractors and system specialists all working together with a structured, well managed approach. The BMS was actually used to support the commissioning of other systems.”
Commissioned controls mean better building operation.
“We can provide a dashboard that shows how the system is performing. It can help the consultant to see what’s working. This sort of technology could help with the time squeeze at the point of commissioning” says Rees.
The ideal for controls professionals would be to return to a building once it’s occupied and tweak the controls to match occupant requirements. However, that is rarely allowed for in construction budgets. Yet, as we face increasing pressure to make buildings more energy efficient and better for occupants, time and money invested in commissioning controls is more than justified.