A clean sweep
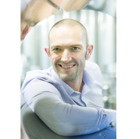
Flue and chimney systems need inspecting and cleaning at regular intervals. John Hamnett looks at some of the key issues around maintenance programmes.
Everyone knows that boiler systems in the CHP plants of commercial buildings require servicing on a regular basis – but the same can’t be said of knowledge about flues and chimneys. That’s probably because most people think that flues and chimneys are just sections of stainless steel tubing joined together to carry exhaust gases away from CHP plants, so they can’t go wrong, can they?
Tell-tale signs of problems
Flues and chimneys play a pivotal role in the performance and efficiency of boilers, so it makes sense to include them when servicing and maintenance are carried out on a CHP system. In most cases, there will be no obvious external signs that a flue or chimney system is in need of maintenance. However, we have seen some classic telltale signs from more-extreme cases:
• Water marks – particularly on ceilings or, in the case of offices and other buildings, on the square tiles of a suspended ceiling. This is indicative of water leaking from the casings and furnishings. Most people forget that water vapour is an intrinsic part of the exhaust gases carried away from a boiler.
• Furred joints – the acidity of the water vapour can cause corrosion over time, and the joints of a flue system are the most susceptible. The appearance of white or green fur around joints is a good indicator that maintenance is required.
• Blocked drains – they can pose a serious risk to the life expectancy of a flue because if they are left uncleansed and blocked, build-up can soon occur and can deteriorate seals in joints.
Over time, this can also cause rapid corrosion to the inner liners, which, again, can cause the products of combustion to leak from the system.
![]() |
Basic visual inspections
Facilities or premises managers can easily undertake a simple inspection and should check for the following:
• Check that joints / clamp bands are tight and have not been tampered with.
• Check for leakages or spillages, especially underneath joints.
• If any part of the system is accessible, such as an inspection hatch, a visual inspection can be performed to look for tar/soot, foreign objects or condensation – depending on what boiler type the flues are connected to.
Call in the experts
Specialist cleaning and maintenance companies offer a range of services, including:
• Expert visual inspections – these assess the entirety of a flue system, from the point at which the flues are connected all the way through a building to the termination point.
• Validation inspections and reports – in situations where boilers are being upgraded or changed, these assess the suitability and compatibility of existing flue systems.
• CCTV inspections – these are ideal for large structures such as free-standing chimneys.
• Full inspections – these are where sections of flue systems are removed to enable full inspection, cleaning or diagnostics.
Compliance
At this point, it’s worth giving a reminder of British Standard 4076:1989 – the specification for steel chimneys. Appendix A of the document deals with the inspection and maintenance of steel chimneys and says:
“For lined and insulated chimneys it is advisable to carry out an examination as above at three-yearly intervals subsequent to the first examination. Lined chimneys should also be inspected internally by close examination from a bosun’s chair; or similar means of support, to ascertain that the lining is still in serviceable condition and fulfilling its task.” (A.6 Appendix A, page 16 of the British Standard Specification for Steel Chimneys BS 4076:1989).
![]() |
The paperwork
On completion of inspection, maintenance or cleaning, a good contractor will provide footage of CCTV inspections, project images, copies of handover certification (if scaffolding was used), and a works checklist that covers cleaning, smoke test results, the fact that the system was operational following the work and any advisory points. The final document is a confirmation of cleaning and maintenance certificate, with a date for the next inspection. If the company also installed the original system, then the certificate should continue to validate any warranties.
A final note – why maintenance is so important
Biomass boilers are a good example of why a programme of building maintenance is so important. One school in London hit the headlines because its new biomass boiler kept breaking down, leaving the head teacher with no option but to close the school on numerous occasions because it couldn’t provide heating or hot water.
It serves as a reminder that, despite the promise of burning pellets to nothing, the biomass boiler combustion process does create infinitesimal fly ash – particularly if the pellets are damp before burning. Over time, fly ash, soot and creosote build up and can rapidly reduce the diameter of the flue. This reduces the flue’s capability to perform (in dispersing and removing the dangerous products of combustion safely out and into the atmosphere). As well as causing boilers to break down, this can pose a fire hazard.
A regular programme of maintenance is not only a health and safety issue, it ensures that end users (who have paid for the system) get the most from the equipment across its lifetime. It’s also an important factor in the reputation of manufacturers – their equipment may be excellent but if it’s not maintained, it can be their reputation which is damaged.
John Hamnett is director Commercial Flue Cleaning and Maintenance Services (CFCM)