Get plugged in to modular wiring technologies
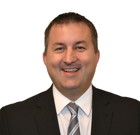
David Draper offers his five top tips to help extract the maximum benefits when designing and installing modular wiring.
Modular wiring is all about saving time and money when installing electrical systems. Electrical cables and connectors are assembled offsite and delivered in ready-made sections. All mains power, HVAC connections, lighting, building control cabling and terminations can be pre-wired within trunking if required and tested prior to delivery.
There are plenty of cost and time-saving opportunities that modular wiring can offer, but extracting the maximum benefits requires careful planning. Here are my five top tips to help make the most of modular.
1. Plan ahead for late design changes and keep costs down
Modular wiring can be used in almost any building, but it is best suited for buildings that have standardised, repeatable room and floor layouts. These include offices, schools, hospitals, retail premises, warehouses or hotels. A modular approach means wiring configurations can be duplicated room-by-room, or floor-by-floor.
This simplifies the design and allows it to be installed in less time with less wastage.
It can also make installations easier to reconfigure and accommodate late or future design changes. Consider, for example, a hotel that wanted to make one of its rooms wheelchair-accessible. This might necessitate lowering or relocating light switches, requiring longer cable runs. This assembly could be built and labelled off-site to reduce installation time on-site.
2. Realise money-saving opportunities
Modular wiring may have a higher up-front cost compared to hardwired solutions, but it slashes overall project costs by taking much less time to install. Rather than having an electrician wire and test every connection, much of this can be done before an assembly arrives on-site. Some modular wiring manufacturers now offer colour-coded plugs and cabling to reduce the possibility of wiring errors and make re-ordering parts more straightforward.
Electricians are still required to ensure safety and carry out final wiring and testing, but in far fewer numbers. With a pluggable system, much of the labour can be carried out by unskilled workers, which results in a far lower labour spend on-site.
3. Work with your supplier
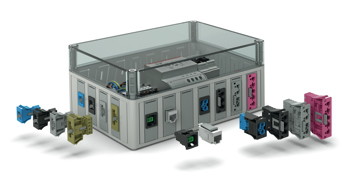
As well as modular wiring, manufacturers are increasingly offering the trunking to contain it, also in modular form. Using the same supplier for both the trunking and wiring can further reduce installation time on-site and prevent installation errors from occurring. On a busy construction project, delays not only cost money for the installer, but can hold up the entire project if the wiring installation is holding up other tasks.
Some suppliers also provide consultancy services, from initial design all the way through to final project handover. This can help to ensure the installation is standard-compliant to BS 8488 (Standard for Prefabricated Wiring Systems), BS 7671 (Wiring Regulations) and other applicable standards.
4. Future-proof your installation
One of the key concepts of modularity is that an installation can be added to or adapted gradually without affecting its overall integrity. As buildings and building services get smarter, the amount of power and data cabling that must be laid out is rapidly increasing. A modular approach enables designers to allow provision for future expansion, while consolidating all cabling into the same trunking assembly. As well as saving space this can save design and wiring time when it comes to upgrading.
5. Spring pressure is the way
Many electrical installations use screw connections to terminate wiring. However spring pressure connections are becoming increasingly popular. These are up to 50 percent quicker to install compared to screw connections, while also delivering superior reliability.
Spring pressure connections use a spring mechanism to apply constant pressure to conductors, keeping them secure without damaging them. Unlike screws, they will not work themselves loose over time, nor do they require regular maintenance. Specifying spring pressure connections can add many freefrom-maintenance years to an electrical installation.
From the designer through to the end user, and every contractor and installer in between, modular wiring can bring greater reliability and flexibility to building wiring, at a lower overall cost compared to traditional hard-wired systems.
David Draper is Interconnection product manager at WAGO