Flues for thought
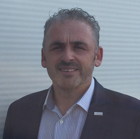
Paul Martin highlights the important role of flue design in ensuring condensing boilers operate at maximum efficiency
Gas condensing boilers remain the dominant force in the UK’s domestic and commercial heating markets. Manufacturers have invested a lot of effort in improving combustion and heat transfer efficiencies, as well as internal components and lifetime costs. However, while these are all worthy points of note, one important element of an installation – whatever its size – that should not be overlooked, is the flue design.
As virtually all modern boilers are condensing models, they are highly likely to be replacing their non-condensing counterparts during retrofit projects. Plus, most condensing boilers are either room sealed or fanned, as well as compatible with many different types of flue, depending on a heating system’s application and/or location.
Flues vary from straightthrough-the wall, extended concentric, twin pipe or extended non-balanced – all of which should be familiar to installers and system designers alike. Some manufacturers also offer extended flue systems, which offer greater flexibility when positioning boilers. With such a plethora of options available, boilers such as ATAG Commercial’s own XL series, for example, are equipped with connections for both flue gas and air inlet (parallel tubes), which allow both open and room sealed arrangements.
In an open system arrangement, boilers’ combustion air can be taken from a ventilated plant room via an air filter, with the flue discharge connected into a cascade header. In contrast, a room sealed system has the combusted air ducted into the boilers via a cascade header system, with the flue discharge connected together into its own cascade header.
![]() |
Planning for flues at high- and low-level ventilation |
Another energy saving option available for condensing boilers is a passive flue gas heat recovery unit. These use a heat exchanger and heat store, fitted into the flue. The cold inlet water is then warmed directly from the flue gases produced by the boiler whenever it operates. This results in the pre-heating of the domestic hot water supply, as well as reduced gas and water usage, as less time is required to deliver an acceptable outlet temperature. ATAG has incorporated this type of technology into its boilers, in the form of a ‘Gas Saver Module’, which provides optimum efficiencies for installations at new build properties – as well as additional BREEAM points through SAP Appendix Q listing.
Design stage
It is important for larger developers to consider BREEAM points, especially during the design stages for multi-storey buildings, where flue layouts can be particularly challenging. This stems from the 1960s, when individual boilers were commonly fitted in flats and connected to shared flue systems designed to operate with room-sealed, non-condensing appliances. Subsequently, boilers in these types of buildings can only be replaced by those compatible with SE and U ducts, otherwise, if an incorrectly designed unit is installed, overheating can occur.
However, there is an alternative arrangement available for new multi-storey apartments, in the form of communal flue systems, which have been popular in Europe for many years. These allow combustion gases from individual [appliances] to combine into one common system and terminate at a high level. Three designs of communal flue systems exist: ‘Naturally vented’, ‘fan assisted’ and ‘naturally vented or fan assisted (exhaust only)’. Naturally vented communal flue systems provide combustion air and removal of combustion products from a number of heating appliances by a concentric flue system. The common duct is a naturally vented negative pressure open flue, while the exhaust ducted normally opens and terminates at a high level.
These days, fan-assisted communal flue systems are being installed more frequently. As the name suggests, the common duct is fanned to help overcome the loss of gas buoyancy, due to the lower flue-gas temperatures exhausted from condensing boilers. Flue joints must be watertight and able to cope with the positive pressure created by the fan, in order to retain the condensate. The appropriate fan control should be specified at the design stage, while any boiler attached to this type of flue system needs to have a non-return valve fitted (either in its exhaust outlet or between the unit and the common duct). This will ensure combustion products aren’t recirculated through non-operational products. Some manufacturers actually build an overpressure non-return valve into their boilers as standard, to cater for this type of flue.
![]() |
Atag’s XL series is equipped with connections for flue gas and air inlet |
Quailty counts
Several communal flue systems can be installed inside the same building, with multiple boilers connected to a duct on each floor. This arrangement enables developers of blocks of flats and other multi-storey buildings to incorporate condensing units into their projects – while simultaneously giving occupants control over their individual heating systems. It also ensures there is no ‘pluming effect’ caused by numerous flues venting to the outside wall.
Whatever type of flue is chosen, it is vital it is one of high quality. All metal flue products are required to carry CE certification, ensuring they perform to the specifications of the system to which they are installed. This takes into account the temperature and pressure ratings of the flue, as well as its condensate resistance for wet or dry systems.
So, while there are many issues to consider when installing heating systems in single and multiple occupancy buildings, the flue system remains one of the most vital. Consulting manufacturers as early in the design process as possible will help both installers and system designers alike to identify the best option(s) available. Doing so will ensure safe, long-lasting and efficient boiler performance.
Paul Martin is national sales manager at ATAG Commercial