Remote control
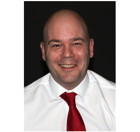
The pressure independent control valve (PICV) is widely acknowledged as a useful tool for achieving precise and reliable balance and control of hydronic heating and cooling systems.
The latest advances in technology have seen the introduction of network connected PICVs that offer the cost and time saving benefits of remote commissioning. A traditional field device receives open/close commands but does not know what is happening across the system. But network connected PICVs are two-way communication devices that can receive complex commands and give different feedback information. They offer the option to send and receive data to improve control even further.
Connected
Fast, accurate actuators are essential to achieving the best indoor climate. Network connected PICVs fitted with intelligent digital actuators that connect directly to a building’s building management system (BMS) can optimise both speed and accuracy. Using BACnet or Modbus communication, for example, this innovative concept provides the perfect connection between superior hydronic HVAC system performance and smart building automation.
Unlike traditional controlled actuators that, at best, offer an analogue feedback signal to the BMS room controller, digital actuators are able to send digital system parameters directly to the BMS. This enables the exchange of accurate information about the actuator/valve position, flow rates, settings, and temperatures. Even alarms indicating any failures of operation or errors when closing can be reported to the BMS.
All this information provides the BMS with a unique insight into HVAC system status. This data can be used by engineers to optimise system performance, helping to ensure the highest level of energy efficiency and indoor comfort at the lowest operational cost throughout the building’s lifetime.
![]() |
Network-connected PICVs are two-way communication devices |
The latest multi-functional digital actuators for PICVs, such as the Danfoss NovoCon, give HVAC engineers access to valuable data for remote commissioning, as well as for continued maintenance purposes. This is a major advantage in a large office building, for example, which may involve hundreds of valves. All valves and actuators can be accessed remotely from the BMS system via Fieldbus communication and be installed and commissioned at the same time.
Time-saving
Whilst traditional commissioning of each individual valve can take 30 minutes or longer, any number of valves can be balanced remotely with a single click of a mouse when using a digitally connected system. This is a huge time saver, and also creates less disruption for building occupants, as engineers can close the ceiling immediately after installation and then fine-tune and correct thesystem from a computer.
As any mechanical engineer will tell you, trying to access and set a valve in a dark ceiling void, often using a torch and mirror, is not an easy task and working in these challenging conditions increases the risk of errors. The ability to remote commission valves via the BMS, including flow setting, flush and de-airing, significantly reduces this risk and ensures greater accuracy.
System data provided by this type of solution can be retrieved and analysed. Any adaptations that may be required in the event of subsequent changes in the system or building use are easy and can be completed on just one device, a few, or all actuators at the same time. This facility can be particularly helpful when adjusting flow rates to meet seasonal efficiency standards. Under the Ecodesign Directive LOT 21 these now apply to commercial heating and cooling products including fan coil units and chillers with specific- rated capacities.
The Directive recommends that flow rates are adjusted as necessary on a quarterly (seasonal) basis. Needless to say, with a traditional system requiring manual adjustment this can be a time-consuming operation. Also, gaining physical access to the building and opening ceilings to complete the adjustment is likely to be very disruptive for occupants. This is eliminated when valves are connected to the BMS via digital actuators. Engineers can simply check flow rate data on a laptop to establish how many valves need to be changed for seasonal efficiency and then make the required adjustments remotely in a matter of minutes.
Further advances
Advanced digital actuators that cmonitor, log and store system data can be used for predictive maintenance purposes. Rather than waiting for the HVAC system to fail, engineers can use this data to see where and when an issue might occur and take proactive measures. For example, remaining lifetime of individual valves and actuators can be predicted based on running cycle data, while monitoring of Delta-T will indicate when filters or coils require cleaning. Being able to prevent the need for urgent service action reduces both system downtime.
![]() |
More and more commercial building projects around the globe are recognising the benefits of network-connected PICVswith digital actuators and the technology is being developed all the time. Recent innovations have focused on achieving even greater control of energy management, such as power control. This facility makes it easy to limit maximum energy consumption by setting emission in kW rather than flow rate in litres/hr. Other new energy features include Delta-T management which, inbrief, limits Delta-T between supply and return to selected valves and so prevents overflows due, for example, to oversized coils, clogged coils and filters. Furthermore, the remote I/O functionality available on some digital actuators can now be used to connect sensors for humidity, room temperature or condensation.
In the age of ‘Big Data’ the ability to provide system feedback and alarms on individual terminal valves is invaluable during installation, initial, seasonal, and on-going commissioning. These Internet of Things solutions provide today’s smart connected buildings with continuous monitoring, energy management and preventive maintenance, improving indoor comfort and energy efficiency throughout the building’s lifetime. No doubt in years to come we will look back and wonder how we ever did without this functionality and flexibility.
Greg Tracy is business development manager (HVAC) of Danfoss