The future is offsite
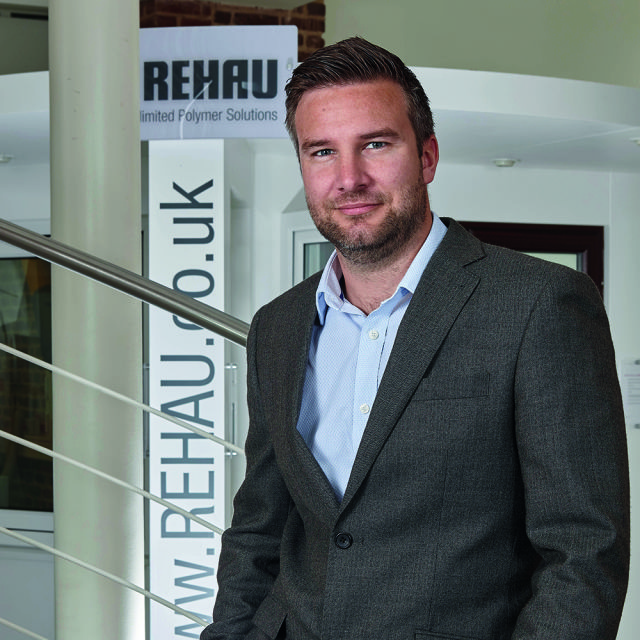
Drew Clough explains why contractors should be changing their business model to accommodate offsite construction and in doing so improve the efficiency and productivity of their business.
The Offsite construction market is on an upward trajectory. Although currently only accounting for 12-15 per cent of new construction industry activity this figure actually represents market size and growth of 30% year-on-year. This growth is being driven by government policy and as a result of the increase in population, the demand for homes, skills shortages in the building industry and environmental considerations.
While this method of construction has become ever more popular in the high-rise construction market, many M&E contractors are yet to utilise this method, despite its many proven benefits.
In recent months, the UK Government has been actively pushing for offsite construction as a key method to replace traditional ways of construction. In fact, in his autumn budget speech Chancellor Philip Hammond said the government wants, “to improve the cost effectiveness, productivity and timeliness of infrastructure delivery.” He promised the government will: “Use its purchasing power to drive adoption of modern methods of construction, such as off-site manufacturing”.
The housing crisis and the phenomenon around build-to-rent space is another one of biggest drivers for offsite construction today. The necessity to meet the demands of the rental sector through quicker construction along with the need to improve quality, safety, control costs and meet strict environmental targets have all contributed to the rise in this method of construction.
Obvious positive benefits from utilising offsite technologies include the improved process and ease of site management. With the project being completed offsite and, in a factory setting, less labour is required and there is less handling of materials, therefore resulting in an easier site managing experience. As offsite project sites are in controlled environments, the entire process of the construct will be reorganised and redesigned and will in turn remove many of the risks that a regular construction site may pose.
A report delivered for the Heathrow development in 2018 by WPI Economics stated that using ONS data updated modelling suggested that by increasing offside construction to account for 25% of all construction activity would be associated with an increase in GVA (Gross Value Added) per job of 3.6%.
In what is one of REHAU’s highest profile offsite construction projects in the UK to date, REHAU’s Thermally Activated Building System (TABS) was installed at the newly opened extension to the Tate Modern on London’s South Bank. Byrne Bros Framework, which produced all the pre-cast concrete slabs ready for the TABS installation for the 10-storey building, formulated it all at their offsite facility in Beckton, East London.
With loops of more than 24,000m of pipework involved in the project, the offsite method minimised disruption to the client and the local community. Due to the work being carried out in a controlled environment, it was also a much safer project in a factory environment. If the construction had taken place onsite and outside, weather would have been another factor to consider and could have delayed the project. The controlled environment of the offsite facility allowed for a much quicker project turn around.
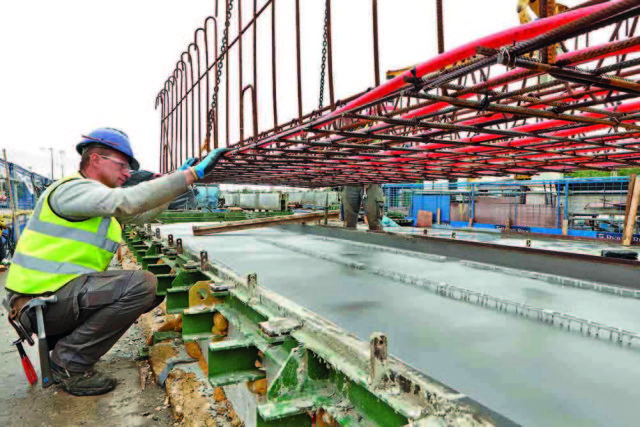
HVAC is another area where there are multiple considerations as to why contractors should be installing heating and plumbing products via offsite methods. Using flexible polymer pipes means that contractors will need to store less stock on the work site. Also, pipes and stock can become damaged whilst in transit to the site, and during the construction itself due to uncontrollable, external variables. Therefore, offsite construction will help reduce the risk of damage and in turn, reduce costs.
The Tate Modern project used more than 24,000m of specialist pipes, which if transported to the site and stored there in bulk, could have been subject to damage. With such huge scale projects taking place offsite, it begs the question as to why onsite methods are favoured among some in the industry, when a safer and more cost-effective method is available.
The benefits of using offsite methods in construction are beginning to demonstrate a higher quality of installation. Prefabrication and preassembly techniques are leading to more economic projects and it is becoming clearer that the M&E market need to adapt to the changes in the business and the ever-growing popularity of offsite construction.
Offsite construction growth comes at an interesting time where the construction sector does not know whether to adopt offsite as a viable option, as businesses would need to remodel their entire process to accommodate it. However, much like some in the architectural sector who are adopting offsite method, M&E’s who accept it early, will find themselves in a stronger position in the supply chain.
The demand for offsite construction will only increase, with considerable growth having been noticed in some key areas such as modular design for bathroom pods and volumetric modules that connect multiple units to create one structure. We view offsite construction as a great opportunity that contractors should take advantage of sooner rather than later.
Drew Clough is product manager at REHAU