Trust not rust
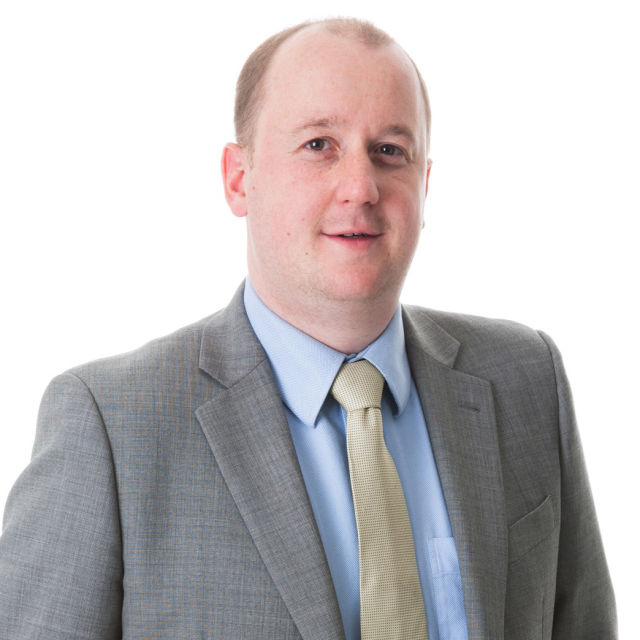
Steven Booth explains that some of the common practices employed during pre-commissioning cleaning have the potential to introduce problems rather than solve them.
Pre-commissioning cleaning is an essential part of a water system’s handover, implemented to clear the system of building debris, mill scale and jointing compound, in order to prevent blocked pipes, leaks, contamination and high energy consumption once the system is up and running.
There are some inherent problems with the processes involved, however, which can lead to unnecessary water wastage, pipe degradation and problems which only come to light further down the line.
Reducing wastage and unnecessary degradation
Installation essentials
|
Pre-commissioning cleaning wastes more water than any other activity during a building’s construction. Traditionally, vast quantities of H2O are required to flush the system of debris to maximize flow rates. Chemical cleaning is then undertaken – using more water – to remove bio-films that encourage the accumulation of corrosive bacteria.
While designed to remove corrosive contaminants, high volumes of water and chemicals can weaken pipe walls, leading to pitting and degradation issues further down the line, effectively shortening a systems usable life.
Advanced filtration units have been developed over recent years and are just as effective but use far less water. With this new technology, the water system is flushed at an extremely high velocity - which also saves time.
The other key way to reduce wastage and unnecessary degradation is through having a proper understanding of system condition. Traditionally, this process is completed by sampling, used during the pre-commissioning cleaning process and at the point of handover.
Pre-commissioning cleaning essentials
|
While an important part of water system management, when used as the sole source of understanding water make-up, sampling has a number of inherent problems. Results can take weeks to return, by which point condition may have changed, and sampling focuses primarily on bacteria, which indicates that things have gone too far – ideally the pre-cursors to bacteria (and corrosion) need to be identified. Dissolved oxygen (DO) is the main culprit here, something that sampling doesn’t effectively detect.
Monitoring remotely
By using 24/7 remote monitoring, a range of parameters can be checked for, including DO, pressure and corrosion rates. This approach also allows trends to be tracked, so it’s clear when an issue occurs and when base levels are returned to, which can lead to a reduced need for chemicals and flushing. If an activity takes place that causes imbalance but stable conditions resume quickly no action may be needed. If a sample had been taken during this period, it may have led to chemical dosing, when in reality by the time the results had returned this was no longer needed.
Monitoring is particularly important at the point of handover, allowing building maintenance teams and FMs to be confident in the system they are being left with. This is key where there are disputes over who, or which part of a water systems commissioning and maintenance has caused a specific problem. We have saved our customers hefty repair bills using Hevasure’s 24/7 remote monitoring solution by accurately attributing a specific activity to a problem and a liable party.
There is no ‘standard’ water system BSRIA provides a set of guidelines (B29/2012)* that inform the process of pre-commissioning cleaning to help promote high industry standards, but what is often missed is the fact this is a guide NOT a standard. One of the most common problems we see is the BSRIA guidelines being treated as a bible.
Every water system, the environment in which it operates and its subsequent usage is different and should therefore be treated as such. There is no ‘one size fits all’ approach to pre-commissioning cleaning or water system management in general. |
While flushing and chemical treatments cannot be completely eradicated, by applying the real-time monitoring model to a water system, a more efficient and sustainable result can be achieved. We believe monitoring should begin during pre-commissioning cleaning and then be undertaken at regular intervals throughout a water system’s life, as a diagnostic tool to ensure that all maintenance is fit for purpose and lean.
*BSRIA guidance is currently being reviewed and an updated version may be published later this year.
Steve Booth is managing director of Guardian Water Treatment