Build your fan base
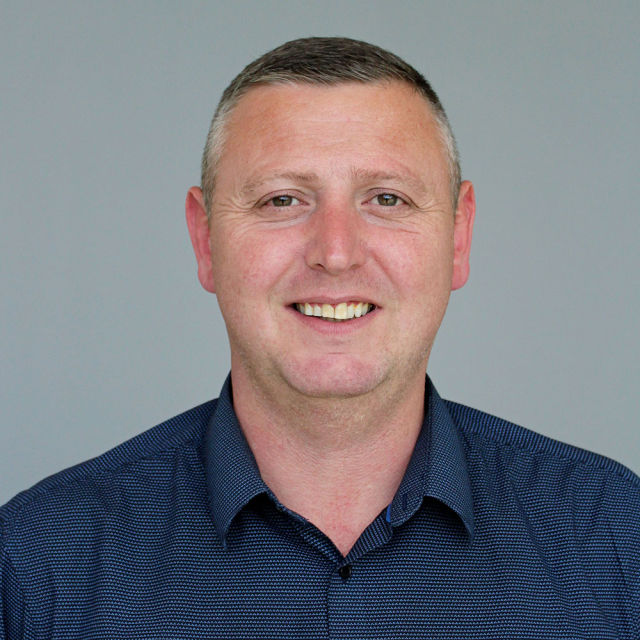
Richard Gordon explains why upgrading fans is a cost-effective approach to saving energy in existing buildings.
The HVAC industry has never been under such a focussed spotlight in regard to matters of the environment, than it is right now. With ever-increasing conversation about global warming and very real fears about the damage to our planet due to high industrial demands, air conditioning manufacturers are being forced to sit up and listen.
Not only is the industry under social pressure to reduce its carbon footprint and to operate more efficiently, it is now legislation. The Eco-design Directive has changed the landscape, forcing manufacturers to look at their production line and find more energy efficient ways to achieve the same results.
HVAC equipment can often account for more than 40% of a commercial building’s energy consumption, thus meaning the Eco-Design Directive is talking directly to them. Some business owners, while aware of the high environmental and financial cost of using so much energy on their cooling equipment, often don’t have the resource to invest in replacing older air handling units that still appear to be functioning.
Fortunately there are simple ways to significantly improve the energy efficiency of existing HVAC equipment, without having to replace full units. Extensive research and development along with live installation data capture has shown that by replacing AC fans with an EC fan upgrade, an organisation can optimise its air handling unit for ultimate energy efficiency, potentially reducing energy usage by up to 70%.
Fan technology has come a long way in the last 20 years. This coupled with the fact that a fan’s performance will naturally degrade over time means that retrofitting AHUs with newer fans is one of the easiest ways to save on energy costs.
Figures show that for a relatively low initial investment by means of upgrading parts (as opposed to whole units), the financial payback forecast is substantial. Furthermore whilst owners of older equipment are not required to meet the new legislation with their existing units, in doing part-upgrades they are demonstrating their contribution towards a greener, cleaner planet.
The key message is not to look at the initial financial cost for the equipment, but to consider the lifecycle of the product along with the associated operational energy costs. It is also important to understand that there are a number of options available to minimise energy consumption by replacing less efficient fans and motors.
1. Direct motor replacement with current high efficiency AC motors, which can alone provide energy savings of around 20%.
2. Replacement of older, less efficient forward curved fans with high efficiency backward curved or aerofoil blade fans.
3. Modification of inefficient, costly belt drive fans with modern direct drive fans, either Plug, AC, PM or EC, with suitable speed control. Upgrading from belt driven fans to a direct drive solution could reduce ongoing maintenance costs by up to 80%
By adding variable-speed AC motors, PM motors or EC fans to the AHU, savings of between 30 to 60% on annual electricity costs can be made.
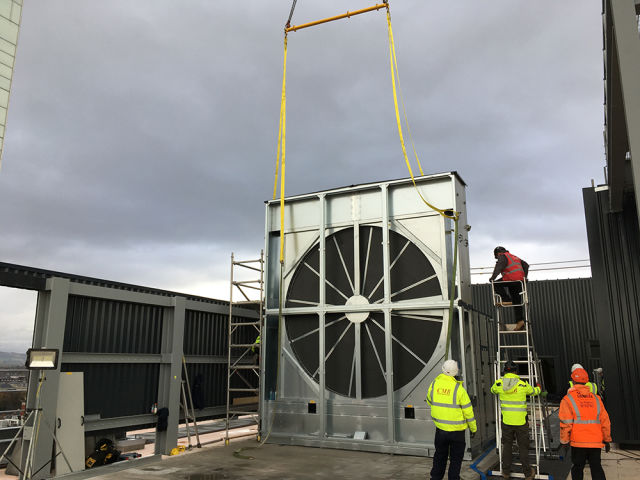
In most cases, modern fans and motors are directly interchangeable with their predecessors, allowing for simple replacements with minimal disruption. Any voltage combination can be accommodated i.e. DC or AC single- or three-phase, as the electronics can be fully integrated into the motor or accommodated by controls systems modifications when carried out by trained and experienced engineers.
EC fans offer enhanced control and provide the most simple, but effective solution for reducing AHU energy consumption. EC fans today are focused on maximum energy-efficiency to enable equipment used in ventilation to work as economically as possible, setting new standards with regards to reliability, service life and energy consumption.
EC fans are fully compatible with most units, meaning that straight-forward, cost-effective EC fan upgrades can be carried out with minimal disruption.
- Up to 70% potential energy saving
- Variable speed control matched to load
- Direct drive motors for maintenance free operation
- 50% more efficient than previous generation fans
There are many contributing factors to consider when selecting the ‘right’ fan for an application. The operating point is the first thing to identify. This is the target air flow rate in cubic feet per minute and a system resistance (or impedance) in inches of water. The target flow rate is usually a known value. The system resistance or impedance is not always available. Knowing the operating point is essential in selecting the correct fan.
That said, selecting a fan based solely on the operating point will not necessarily lead to the best results. The path that the air must take through the system must be factored into fan selection as well. The impact that the air flow path has on a fan’s selection can be dramatic – it can make a very efficient fan perform very poorly and so to select the optimum fan, it is crucial that a full survey is undertaken by an experienced and qualified engineer to identify the above and also understand what the organisation’s design goals are. Whilst the operating point defines the most important variable, power consumption and dependent on application, noise reduction are huge drivers. When noise is a critical factor, the best solution is typically a larger fan running at the lowest possible speed.
Space constraints can also be a factor and as such selection of the right fan must consider the available space within the application. The most efficient or quietest fan may not fit within the physical space available.
Fan selection can never be viewed as a one-size-fits-all approach. It’s really a compromise between variables. The key to success in finding the right fan is to identify which model results in the fewest compromises.
As a starting it is important to make a site survey of existing kit. This can help give the organisation a good idea of payback periods and on-going savings if fan upgrades are undertaken. It is a good idea to work with a supplier that has specialist knowledge in this area, as they can help to identify design goals.
Employing the skills of an experienced supplier and installation team is crucial when starting a fan upgrade project to ensure the solution is tailored to that business’ needs. As demonstrated above an effective upgrade will more than pay for itself over time and will assist a business in meeting environmental and cost-saving targets, without the expense or disruption of replacing full units. It is fair to say that any business that has an AHU system over 10 years should consider an upgrade, as chances are it will result in considerable savings.
Richard Gordon is commercial manager of Barkell, part of the Airedale Group