5 star challenge
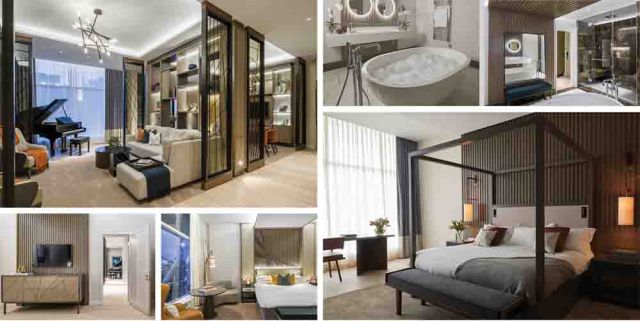
Daniel Tebay the challenges of delivering operational refurbishment projects in a luxury hotel environment, drawing upon the company’s experience at the five-star Lowry Hotel in Manchester.
First opened in 2001, The Lowry Hotel was Manchester’s first five-star hotel. In the hospitality sector, a reputation for being a city’s most prestigious place to stay goes hand in hand with an imperative to invest in regular upgrade programmes to ensure the accommodation and facilities live up to customer expectations. However, any closure of rooms or facilities involves a loss of revenue, so refurbishment work must be carried out while the hotel maintains business-as-usual operations wherever possible.
Krol Corlett has worked with the hotel for a number of years, helping to keep the building and its services up to high standards. There have been five major refurbishment projects around the building during that time. Each involved working with the existing building services networks and, despite the relatively recent construction of the hotel, not everything was installed as designed and not all subsequent modifications have been accurately recorded. As a result, both the project management and mechanical and electrical teams involved have had to take an agile approach to delivering the programme around a changing landscape of the client’s operational requirements and the building’s physical condition.
The First refurbishment projects was of the washrooms in the communal areas of the first and second floor, including the installation of new sanitary ware, taps and hand dryers, along with and upgrade to decorative finishes.
Although these areas are not revenue-generating facilities for the hotel, they are part of its five-star offering, so the project involved time-pressure to get them back into full use as quickly as possible. Throughout the six-week upgrade programme toilet facilities had to be available for use during events and functions.
Planning and co-ordination of this work was vital. Isolations of plumbing and electrical services were carried out at the start of the working period each evening to enable new sanitary ware, taps, hand dryers and lighting to be installed and the services were restored before the start of the following day’s event schedule. Temporary partitions were used to enable access to as much of the washroom area as possible during operational hours.
The next stage was the remodelling and refurbishment of the hotel’s 300m2 Presidential Suite. The calibre of facilities and finish in Presidential Suite is critical to maintaining the hotel’s luxury reputation and has hosted stars including Beyoncé, Justin Bieber and Mohammed Ali. As the hotel had an existing booking directly after the handover date, the programme was fixed and there was no question of it running over, regardless of any challenges the strip out and installation uncovered along the way.
The project began with a full strip out of the suite and a connecting room. This involved working carefully around any electrical and mechanical isolations that could affect services in other rooms or common areas. It also involved minimising noise and dust at all times and ceasing work completely when a VIP guest was expected. Close collaboration with the hotel’s management team and an agile programme of work was essential. The project manager had to co-ordinate works with the mechanical and electrical installation team on a daily basis to work around any restrictions and manage movement of work teams and materials to the top floor via the service lift, avoiding any disruption to guests.
The remodelling works included extending the suite’s master bathroom and dressing room while introducing some new partitioning to reconfigure the space. This meant significant changes to the electrical layout too, and previous modifications to cabling routes had not been updated on the as-built plans for the building, so managing an unfamiliar electrical layout with an unpredictable installation schedule was a considerable challenge. As part of the project, therefore, we also undertook to identify discrepancies and provided an as-fitted layout at handover.
The mechanical and electrical works also involved installation of a wide range of high-end A/V and smart technology equipment, with lighting controls and smart controls that can be operated by both the hotel and the guest occupying the suite.

For the subsequent reception and lobby refurbishment and the recently completed restaurant and bar upgrade, the working conditions have been less challenging because of a reduced need to manage work around guests and public access.
While the reception and lobby is the most public-facing area of the hotel, this project was designed with a redirection for customers to a temporary reception and an acoustic hoarding was erected to shield the work area from the central stair core. This not only reduced the potential disruption of noise and dust for guests while the works were carried out, but also enabled a dramatic ‘reveal’ of the completed works when the project was finished. The most significant mechanical and electrical element of this project was the installation of new feature lighting. Once again, upgrading electrical services and replacing light fittings was made more challenging by historic changes to service routes which had not been accurately recorded.
The restaurant and bar were closed for the duration of the eight-week refurbishment project but, once again, the handover date was business critical due to
bookings that had already been confirmed by the hotel. Minimisation of noise and dust was also essential to reduce any disruption to guests, and the mechanical and electrical installation teams also had to ensure that isolations to services in this area of the hotel did not affect services in corridors or guest rooms.
The latest refurbishment project at The Lowry Hotel is still ongoing and this involves the upgrade of five of the hotel’s suites. The project team was able to take occupation of all five suites at once to commence strip out but the upgrades are being delivered on a phased handover basis, to enable each one to go back into service as soon as possible.
In addition to the need to identify service routes and service connections that affect areas of the hotel beyond the suites, the mechanical and electrical installation team is also tackling a scheme that includes the installation of a new suspended ceiling with feature recessed lights and a new lighting control system. The suites will also have a new TV and A/V system fitted and all TV aerials will need to be individually configured.
With each project that is handed over we are providing the hotel with as-fitted plans for the building services which will aid ease of design and delivery for future upgrade projects. In the meantime, a meticulously planned programme and an agile approach to adapting it while on site are vital to meeting business critical deadlines.
Daniel Tebay is director of construction contractor Krol Corlett