Full potential
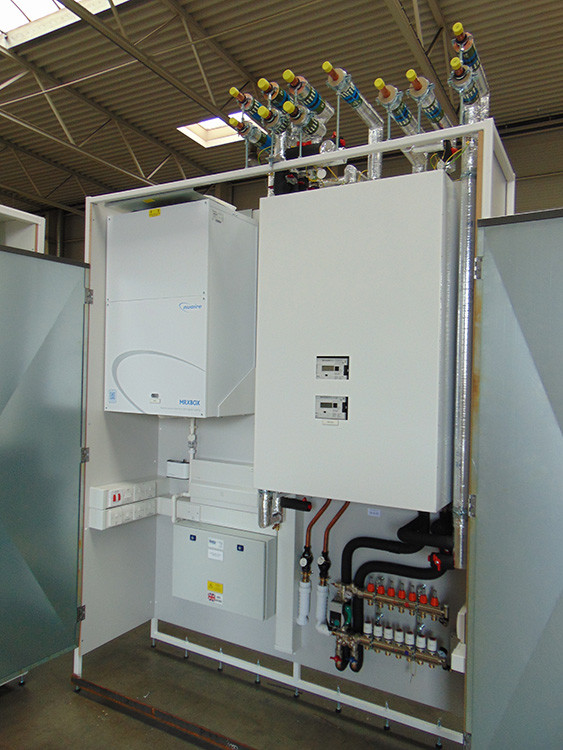
Use of offsite fabricated heating solutions is on the up in residential developments with communal heat networks. But early engagement is key if the maximum benefits are to be reaped, says Ian Lock.
Adopting modern methods of construction (MMC) has been hailed as the silver bullet to overcome the current skills shortages and satisfy the surge in demand for residential property development. The benefits of MMC are well established, from significant reductions in time and costs to improved onsite safety, reduced waste and enhanced quality control.
When it comes to the building services, the advantages of using offsite prefabrication techniques are equally compelling. Take offsite fabricated service pods, for example.
New residential properties typically house hundreds of individual apartments, all served by a communal heat network or a central energy plant room. Prefabricated service pods can be installed rapidly within each individual dwelling to meet all requirements in a compact, efficient and space-saving solution.
Designed on a modular platform to meet the site and project requirements, the pods are fitted with a full suite of HVAC including a heat interface unit (HIU) and electrical components. The cupboards can be configured to suit the exact layout, service connections and spatial requirements of each building. The pods are then fabricated offsite in a factory setting, arriving on site fully assembled and ready to install.
A key benefit of the offsite fabrication process is that it enables mass customisation across the development, improving the quality, accuracy and efficiency of the products. The specifier and contractor can be sure that the exact specification will be met, reducing risks and helping to keep to budget. Installation is faster, snagging and de-snagging issues are vastly reduced along with onsite hot works, and costs and onsite disruption are hugely minimised.
But here’s the caveat – to unlock the full potential of prefabrication, it’s essential to encourage early engagement and collaboration between developers, consultants, architects and customers from the outset.
A major advantage of prefabrication is the ability to load the design of the units in line with customer requirements. However, it should be noted that this is a change to traditional manufacturing procedures, as it requires a more detailed design to be agreed and delivered at a far earlier stage. Consequently, when considering offsite fabrication, total buy-in to the process is essential, with excellent coordination a crucial factor for a successful outcome.
How does early engagement benefit the project?
Early discussion at the outset provides the opportunity for all the stakeholders to discuss the project and gain a clear understanding of what the customer is trying to achieve. With different areas of expertise to tap into around the table, the project team can then weigh up the options and produce the most creative and achievable solutions that will deliver the required outcome.
In this way, the design stage becomes an iterative process with 3D drawings produced to show each element in the service pod, its precise location and the available space. While the 3D drawings provide useful early visualisation, in our experience it can be helpful to produce one example of the finished pod before starting mass production.
This will enable all parties to consider every aspect of the unit and how it will function in situ. Where will the electrical consumer units be positioned? Maintenance workers will need to be able to access all of the prefabricated aspects once installed. What about the cables? Cable trunking, routing and containment is another key element that must be determined at the outset with prefabricated utility cupboards.
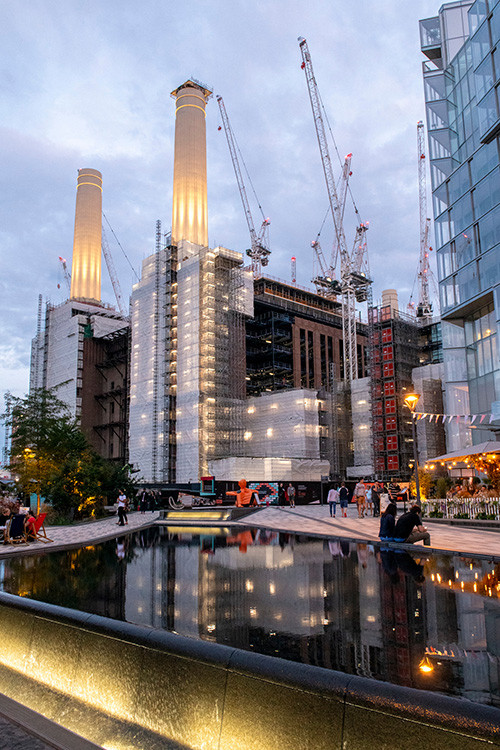
It’s also important to ask if the right materials been specified? This is particularly important in high-rise developments to avoid excess noise or sound. If a ventilation system is not mounted correctly and/or mounted on the wrong type of structure, it can lead to excessive noise and vibration that would travel through the building into other residences.
Specifying the right material to contain a utility cupboard will have implications on safety as well as acoustic performance. It’s vital, therefore, to ensure that the correct fire retardant and preventative materials are specified, especially in high-rise buildings.
One of the main advantages of modular prefabricated units is the opportunity to maximise cost savings through mass customisation. It may sound obvious, but once production has begun, the design cannot change without incurring significant cost implications and delays in delivery. So it’s critical that every detail is addressed at the outset. At the same time, this process gives the customer greater cost certainty and greater confidence that the project will be delivered on time and to budget.
The prestigious Battersea Power Station development is one example where prefabricated service pods have been used. The power station project comprises the refurbishment and transformation of the iconic Grade II listed Power Station into modern use. Due to open in 2021, the building will house more than 100 shops, restaurants and cafes, an events venue, office space – including Apple’s new London Campus – and 253 new residential apartments.
Packaged Plant Solutions, part of Baxi Heating, supplied offsite fabricated utility cupboards for the residential apartments. The final pods included a HIU/CIU for heating and cooling, mechanical ventilation heat recovery, underfloor heating, electrical distribution, and metering and billing devices. A washing machine was also included in each pod.
Due to its heritage status, the building presented significant challenges in terms of design and logistics. However, early engagement and collaboration with Battersea Power Station Development Company and Mace, the Principle Contractor, enabled the team to achieve the most efficient and successful design.
The Packaged Plant Solutions team supported Mace’s architects and consultants with the system design and provided BIM models for visualisation purposes. The opportunity to work alongside the M&E designers and lend manufacturer expertise, meant that a detailed design could be assessed and approved at the early stages. Only once the standardised approach was agreed was the production line set up for the manufacturing process begin.
By manufacturing the full solution offsite, the risk of human error was reduced significantly, as were the health and safety because of the elimination of hot works on site. It also saved huge amounts of time on the overall project. To put it into context, it takes three hours to connect one unit via MMC, whereas an on site installation can take up to five days.
The success of the Battersea Power Station project demonstrates how offsite fabrication is as relevant in refurbishment projects as in new building development. And with demand for residential properties showing no sign of slowing, the role of MMC, and offsite fabrication in particular, in providing value added benefit is clear. But early engagement, full commitment and improved coordination across the supply chain are key if the maximum benefits are to be reaped.
Ian Lock is Baxi Heating’s business development director