Intelligent heat networks improve network efficiency
Intelligent heating networks can revolutionise heating efficiency and reduce energy usage, says Neil Parry of Altecnic
Even where networks are well-designed and properly commissioned before residents move in, heat networks are often left to drift, with performance degrading over time.
This is often not due to a fault in equipment, but rather is due to the accumulation of many small changes in the system over time, for example maintenance engineers changing one part of a heat network without regard to the effect on the whole.
Research has shown that the cost of heat and carbon emissions can more than double on a heat network within three years if action is not taken.*
Continuous commissioning through an intelligent heat network improves network efficiency by maintaining set points, reducing network drift and reducing costs. What’s more, it can be done remotely, removing the need, inconvenience and costs for an engineer to keep visiting the site.
The Climate Change Act commits the UK government to reducing greenhouse gas emissions by at least 100% of 1990 levels by 2050. Heat networks are fundamental to the decarbonisation strategy, with the proportion of UK heating delivered over heat networks projected to rise from 2% to at least 17% and as much as 43% by 2050.** To fulfil their potential, heat networks must be as efficient as possible, while also meeting the needs of customers.
But we know that heat networks start to run less efficiently over time due to system degradation, often from an issue that has slowly got worse as time’s gone by. Quite often the efficiency drift is evident, but it is difficult and costly to resolve, so maintenance/adjustment is left until it reaches crisis point.
Prevention rather than cure
In the same way, we regularly hear from stakeholders that if a Heat Interface Unit (HIU) develops a fault, traditionally, the tenant would experience the problem, then advise the caretaker, the caretaker would then contact a plumber or the manufacturer. Many days could pass just going through this process. When the plumber/engineer attends site, they will have to investigate the problem and may or may not have the required spare parts. This creates even more delays for the customer.
With an intelligent heat network that can be controlled remotely through the Internet, such as the Guru Integrate SATK32, a fault can be identified even before the tenant is aware. An engineer can be called out instantly with the full knowledge of what the issue is, how to fix it and carrying the correct spare part they require. The problem for the customer is resolved rapidly and far faster than before.
Benefits for all
This brings multiple benefits to all involved. For the contractor who is employed to install the HIU, they can install the unit but then save themselves the time and expense of being onsite by commissioning it remotely via a web browser.
In addition, during the defects period, which can be anything from 1 to 2 years, the contractor doesn’t have to initially travel to site, saving time and money, to investigate a fault or problem reported by a tenant. Instead, they can login remotely to the network to diagnose the problem and potentially resolve it that way too. If the contractor still needs to visit the site, they can go along armed with the relevant part that they have been able to identify from accessing the HIU remotely, again saving time and costs by only needing to make one visit.
Often the contractor can advise and help the tenant over the phone, suggesting what they can try themselves to resolve the issue based on the information they can access remotely. After the defects period then this remote baton can be handed over to the facilities management company or caretaker, enabling them to troubleshoot tenants heating issues without initially needing to go to site.
A physical visit to an occupied flat to change HIU settings can cost up to £600. A remote intervention is estimated to cost around 1% of this figure.
For the energy supply company (ESCO) who manages the network, they are able to look at the data provided by the intelligent heat network to calculate how much it will cost them to generate energy to the property and therefore how much to charge their customer per unit. And for the developer or landlord of the property it reduces the amount of potential calls from their tenant(s) phoning up to report heating problems.
Quizzing the data
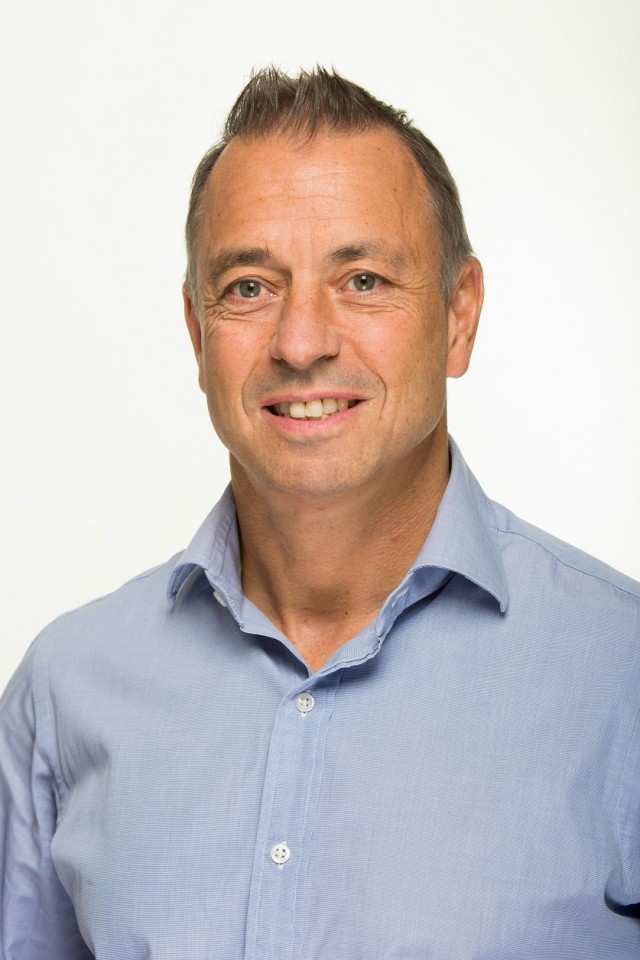
So what sort of data and analysis can be done on an intelligent heat network compared to a network where the data is coming from a typical energy meter?
On a typical energy meter there are circa 12 to 14 points of data available that can be used to analyse energy usage and efficiency data, such as flow and return temperatures etc. With an intelligent heat network, this increases exponentially. MODBUS connectivity can give 250 points of data or more, giving a far more detailed and granular insight into how the network is performing and how it can be improved or issues fixed.
This additional, fine resolution data will also allow us to learn more about the actual demands on a network, the actual diversities, actual flow rates and usage patterns etc. in real time, on actual installations. This additional data could be used to feed into standards, avoid network oversizing and allow us to construct and operate lean, efficient networks that reduce energy usage, reduce carbon and reduce the cost to the stakeholder.
But it’s not just about reading the data, a standard energy meter can only be read, whereas an intelligent network can be read AND written to, enabling changes to be made remotely.
Reducing carbon impact
Just like the electricity grid, existing and new heat networks must decarbonise over time in order to live up to their potential.
One way that heat networks can reduce their carbon impact is to run at lower temperatures. Lower temperature networks have reduced heat losses, and also mean that a wider range of zero carbon heat sources can be used, such as heat pumps.
When lowering network temperatures, it is imperative that the HIU’s output temperatures are reduced to suit. Reducing a network flow temperature to 60°, when the HIU’s are set to provide space heating at 65° will cause catastrophic failure of the network. The HIU’s close to the plant-room take all the available energy and the HIU’s further out on the network are starved. The result is multiple tenants without hot water.
For this reason, the potential savings in carbon and energy have been ignored and networks have been set to run in the ‘worst case’ winter condition, all year round.
Imagine now, a system where the HIU’s are tracking the flow temperature and adjusting set points, automatically, thereby keeping a stable approach temperature and constantly adjusting to maintain the most efficient network and the best possible performance.
In the example above, if the flow temperature is dropped to 60C, all the HIU’s automatically adjust their space heating settings, down to 55C. The network continues to operate without issue, but in a more efficient condition. The reduction in energy use and carbon emissions all happen automatically, without operator intervention.
Now and later
Intelligent heat networks are here now and for the future. Not only do they save time and money for all parties involved – developer right through to tenant – but they are also essential in reducing our impact on the environment and contributing to the Government’s 2050 CO2 reduction goal.~
* Guru Systems real-world monitoring of heat networks over a three year period, delivered in collaboration with the UK Government
** The Association for Decentralised Energy ‘Heat Networks in the UK’ market report 2018