Smart power technology
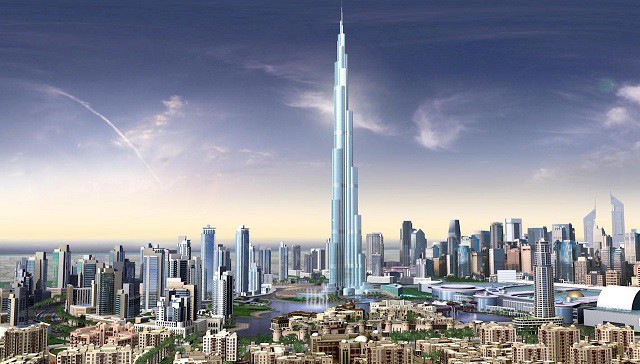
Nigel Thomas of ABB discusses how building services managers can use smart power technology to control energy consumption.
How can electrical technology help building managers deliver more with less?
According to media platform Construction21 International, predictive maintenance is 3-9 times less costly than traditional time-based maintenance. It reduces inspection requirements and means that spares and consumables are only used when they’re needed, rather than according to a schedule.
Smart electrical infrastructure also provides the additional benefits of higher resilience and uptime for services. That is essential for mission-critical sites, and it also provides higher tenant satisfaction when system faults can be identified, repaired and re-booted quickly.
Climate change and the pandemic are also driving demand for smart systems. The US Green Buildings Council surveyed workers in Leadership in Energy and Environmental Design (LEED) certified buildings in 2018. It found that they feel happier, healthier and more productive and if given the choice would prefer to work for employers working from LEED-certified buildings. The pandemic has accelerated this trend.
How does technology reduce maintenance and operational costs?
One example of a building that has deployed smart power distribution is the Burj Khalifa in Dubai. In 2019, our local team upgraded the building’s electrical distribution system with digital sensors and controls. The new system oversees the power supply for 400 electrical loads, including a 24 MW HVAC (heating ventilation and air conditioning) system and 57 elevators serving 163 floors.
To meet the goal of reducing operational costs, we deployed an ABB Ability Electrical Distribution Control System. It uses sensors embedded in devices and in the building to provide real-time data on energy, power, current, voltage and temperature. It also monitors for harmonics and power quality issues.
The project required the upgrade of the existing air circuit breakers by retrofitting them with new plug-and-play digital trip units.
The sensors feed data to a cloud-based system with an algorithm that constantly monitors and assesses maintenance requirements, and raises alerts so that the maintenance team is kept informed and can take preventive action. A further benefit of the cloud-based approach is its accessibility from anywhere and on any device with a web interface, so that managers can remain in control wherever they are.
The system enabled the Burj Khalifa to replace its time-based maintenance and inspection regime with condition-based maintenance. As a result, its operational costs have dropped by as much as 30 percent.
And the system was also built to enable the addition of energy management in future.
How can operators in the UK apply energy management?
Energy management is a tool that can help building managers keep consumption below a maximum threshold. This uses intelligent decision-making to prioritise loads for automatic shedding and reconnection.
UK operators can use it to avoid penalty tariffs under the DCP161 regulation, as well as saving carbon dioxide emissions and cutting bills.
Energy management used to require the design and installation of load control devices and PLC controllers. However, today it can be integrated into the trip unit of the latest generation of air circuit breakers (ACBs) and moulded case circuit breakers (MCCBs). These also have built-in metering, monitoring and communication modules to support the function.
How can building managers become carbon neutral?
We’ve used our own factory at Lüdenscheid in Germany to show how industrial and commercial building operators can achieve carbon neutrality. The site produces electrical installation products such as switches, sockets and connectors, as well as high end building automation solutions.
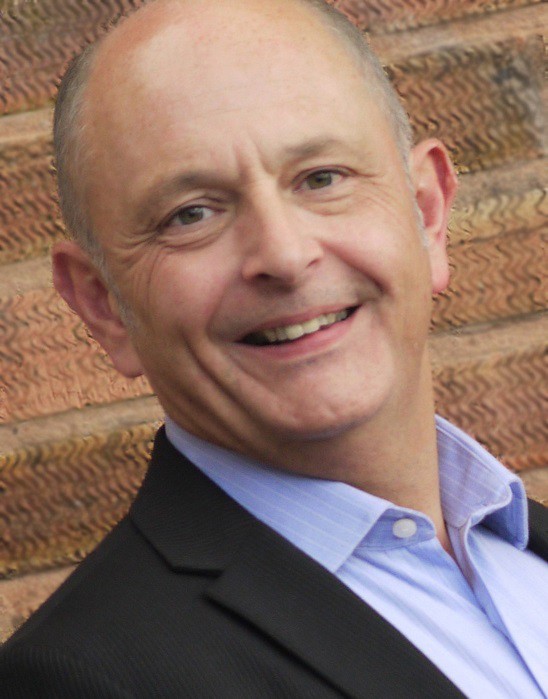
This made ideal to be a flagship site and an early project in our programme to reduce our own carbon emissions to zero.
One of the first priorities for the site was to establish on-site renewable energy generation. We installed an array of solar photovoltaic (PV) panels to generate 1,100 MWh annually, equivalent to the annual demand from 340 private homes. These cover an area of around 3,500 m2 and on sunny days can deliver 100 percent of the factory’s power demand. To maximise the use of space, we have installed them on canopies over the existing car park.
We also deployed a high-efficiency cogeneration plant, which has twice the energy efficiency of a traditional coal-fired power plant.
Together, the PV panels and cogeneration unit provide around 14 percent more energy than the factory needs. That gives us scope to earn income from selling surplus green energy to the grid. However, we have also engaged MVV Energie AG to supply green power to cover any peaks in demand that we cannot meet from our own sources.
To balance power supply and demand, we installed a battery energy storage system capable of delivering up to 200 kW and with a capacity of 275 kWh.
Meanwhile we also provided electric vehicle (EV) charging points for staff and visitors to use free of charge to encourage the adoption of sustainable transport.
A control system acts as the brains to automate and optimise energy generation, consumption and storage. It is based on our scalable OPTIMAX energy management system, which uses data to learn and predict power supply and demand, and compensate for deviations in real time.
The installation was completed in 2019 and is now saving around 630 tonnes of CO2 annually. We are now using the scheme at Lüdenscheid as a blueprint for other sites.
How can we pack more electrical distribution technology into a smaller space?
Whether it’s a smart phone or a watch, we all expect the latest technologies to deliver the same level of performance from a smaller envelope – and it’s no different with electrical distribution systems.
For example, we recently delivered systems for a Purpose-Built Student Accommodation (PBSA) block in Swansea that helped developer RDE Silex and operator Fusion Students to dedicate maximum footprint to student living.
That created the challenge in the panels feeding each floor. Traditionally, a contractor would install individual metering cubicles to house energy meters. However, as space was tight, we supplied energy sensors with digital connectivity. These compact devices communicate directly with a cloud-based control and monitoring system. This eliminates the need for a technician to read meters.
Elsewhere in the building, we deployed a hardware and software solution to provide control, monitoring and management of electrical power at every step from the incoming utility supply to individual circuits. It includes hardware based on the latest compact circuit breakers and panels, as well as circuit monitoring systems and Internet of Things gateways.
Like the system at the Burj Khalifa, these integrate metering, power quality and communication so that they feed data directly to a cloud-based management platform. In turn, the building managers can monitor the site remotely and optimise inspection and maintenance.
Nigel Thomas is ABB’s National Specification and Projects Sales Manager