A robust approach to industrial protection system specification
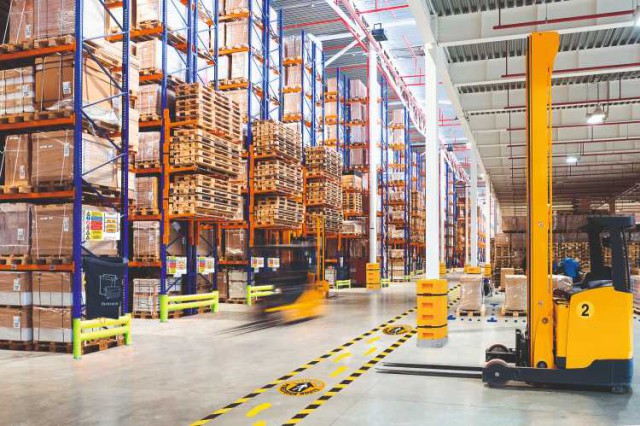
Architects are increasingly specifying industrial protection equipment for warehouses and distribution centres. Paul Roehricht of Brandsafe provides guidance on best practice.
Distribution and logistics are dynamic sectors that’s forecast to be worth over $325 billion by the end of 2024. In the UK alone, one leading commercial property group* reports that investment in UK industrial and logistics totalled a record £6bn in H1 2021, more than double the £2.7bn recorded in the same period of 2020 and up 54% on the previous record period in 2018. It also forecasts that the UK will require an extra 92 million sq. ft. of warehousing space over the next three years. The demand for online grocery sales alone will account for 7.1 million sq. ft. of this additional space.
So, what does all this demand mean for warehouses now and in the future? One thing for certain is that continuing best practice around health and safety in industrial environments that are becoming ever busier will be crucial. People and property need to be protected and architects and others responsible for these designs, need to understand how they can facilitate better, safer and more effective workplaces for their clients. Under UK law, employers must observe a duty of care to their workforce: they must identify the risks each person faces at work and plan accordingly.
Specification
A key part of best practice involving specification for new warehouses, or even improving or expanding existing ones, centres around the efficiency and sustainability of the property - clients are ultimately looking for a premises that runs as safely and efficiently as possible. The Health and Safety Executive’s HSG76 advises on a number of areas that need to be taken into account when planning the layout of a site so that ‘…pedestrians and vehicles can circulate safely. Where vehicles and pedestrians use the same traffic route, there should be adequate separation between them’.
This involves the installation of clear signage and floor markings, which are crucial to the safe and efficient movement of people, vehicles and machinery around the industrial workspace. HSG76 also recommends combining this clearly discernible signage with guardrails and pedestrian handrails used to create clear segregation and traffic routes.
Racking and storage is another area where incremental gains in safety can be achieved in a relatively straightforward and cost-effective manner. The application of clip-on protection to rack ends and any sharp edges of units will for example, protect people, vehicles and the units themselves from impact and collision damage.
Careful consideration should also be given to choosing the right products supplier. First and foremost, it is critical that they must offer products appropriate for the project. This might seem somewhat obvious, but it is not uncommon for some safety products to look good on paper only to lack the necessary performance characteristics that make them suitable for the required application. Here, opt for products whose performance has been assessed and verified through independent testing - this will always be a good starting point and a clear indicative of suitability.
A good supplier should be able to advise an architect on the performance requirements for each system on a project-by-project basis, which will allow you to tailor your designs to the exact needs of the end user. This is where it benefits to partner with a supplier which has an in-house surveying and design team; they can directly support you and make it easier to create bespoke solutions for each project.
Requisite expertise
Looking further down the project timeline, it will make life easier for the appointed main contractor if your safety system supplier is able to deploy its own installation teams. They will be best placed to assist on-site, helping to make sure that the project is completed within the desired timescales and budget. They will also have the requisite technical knowledge to deal with any issues on-site during the installation process, adding further to fast turnaround times and efficiencies.
It’s important to bear in mind that the end client is duty-bound by Regulation 3 of The Management of Health and Safety at Work Regulations (1999) to ‘…make a suitable and sufficient assessment of the risks to the health and safety of their employees to which they are exposed whilst they are at work’. An experienced supplier will be well positioned to offer advice and insight when it comes to producing a comprehensive risk assessment for the project site in question.
It is also worth considering the strategic partnerships of the supplier when the relevant products are required for your project. Ultimately, architects and specifiers will want to work with fast and responsive suppliers; organisations that can guide and advise based on project requirements through a consultative approach.
This can be seen in the work supplying safety and impact protection equipment for major new warehouse and distribution centre operators such as Amazon. Working with project architects SMR Architects, providing consultancy and project design, together with a comprehensive package of aftersales service support, the specification of a range of its high-quality safety and protection equipment for a 180,720 sq. ft. multi-storey site in Neasden includes products designed to facilitate pedestrian and parking safety while improving vehicle traffic routing and calming for the site.
The Neasden site is part of on-going plans by Amazon to upgrade its international distribution infrastructure to improve its operations and boost deliveries to millions of customers. Several sites across the UK and Europe are either under new construction or being upgraded to provide state-of-the-art centres to meet the current and future operational requirements.
Hundreds of items of impact protection products, including Armco safety barriers featuring integrated safety ends, corners and post caps together with pedestrian safety handrails, column protectors, bollards, speed bumps and flexible traffic delineators, are among a package of equipment installed onsite by Brandsafe’s expert service team. The equipment is manufactured at the company’s Milton Keynes site and sees close cooperation also between product supplier and contractor teams as part of an extensive scope of work to provide added safety planning services and expertise.
The project shows how the requirements of customers can be met, adding value in the process through bespoke planning and consultancy services. It also reflects how adopting a holistic approach to risk mitigation in the specification process from the outset has to be seen as good practice and a sensible first step. This includes combining practical standards with safe behaviour as a part of an efficient workplace operation. The key part of managing risk starts with an assessment - the effective process of evaluating threats to health and safety from workplace hazards to eliminate or reduce the level of incidents/accidents.
And what should be considered best practice when managing workplace risk? Success in managing risks is based on effective assessment: the process of evaluating the risks to workers from hazards to determine appropriate measures to eliminate, or at least reduce the level of incidents/accidents. An assessment should identify the key health and safety priorities within and around the warehouse so that efforts can be concentrated on these important areas.
A thorough risk assessment will involve considering a raft of workplace factors, the dangers they may pose and who might be harmed by them. This work should involve gathering information such as current shift patterns, work arrangements and then evaluating it before an assessment to decide on the most appropriate measures and strategies to cut risk.
Health and safety is a critical component of any modern, well-managed warehouse or logistics operation and there is always room for improvement when it comes to safeguarding and protecting people, and mitigating risk. In short, specification of effective safety solutions is simply good business.
Paul Roehricht is Strategic Accounts Manager at Brandsafe