Pressurisation: The key to an efficient hospital HVAC system
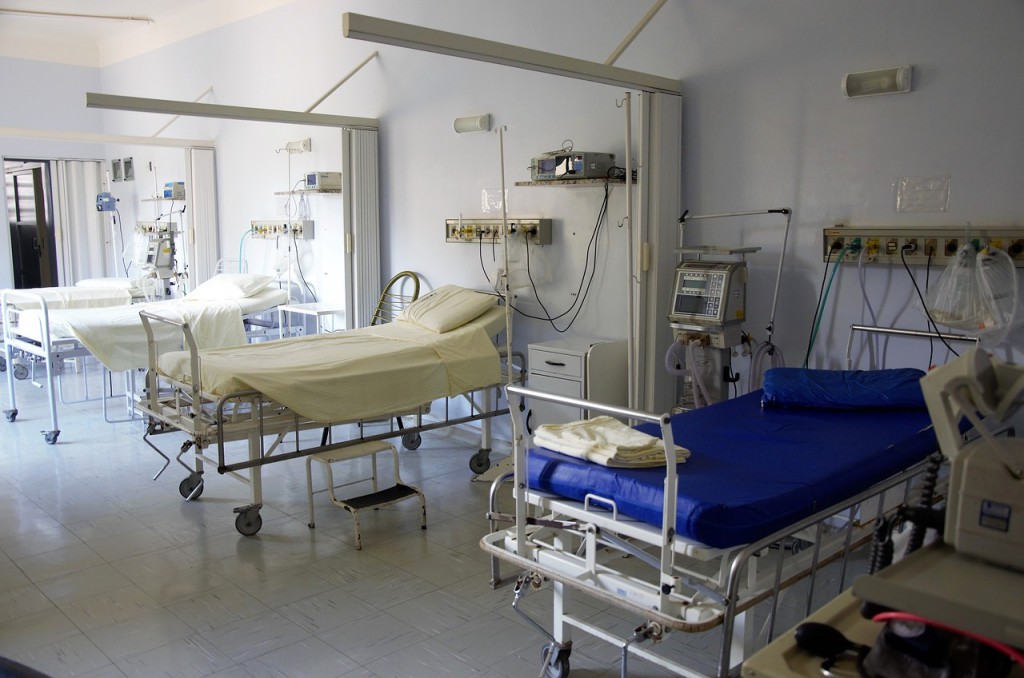
The efficiency and reliability of the heating and cooling systems within a hospital are crucial – just a couple of hours’ downtime can impact on the comfort of patients and staff unless there is a fallback position. However, if a cooling system fails, then this could have a major impact on such devices as an MRI scanner. Steve Simmonds, Spirotech’s Special Projects Engineer, outlines the key areas that need to be considered to ensure an HVAC system works efficiently and reliably.
Without the right preparation and research going into the planning of a plant room, the resulting installation will almost certainly not run optimally and, over time, require evermore frequent maintenance visits. The system may also be prone to breakdowns further down the line. Therefore, a plan needs to be in place to deal with such a situation should it occur.
Specifying the correct equipment for a particular scheme is vital and should cater not just for current needs, but any envisaged future expansion. The system needs to be capable of maintaining a comfortable temperature, whilst keeping both the humidity and airflow within the building at the correct levels.
If the wrong equipment is specified in the first place, or a contractor changes parts to cut costs without ensuring it can deliver the same performance and reliability, then there is likely to be future problems that will need to be addressed. Therefore, facilities managers need to work closely with experts that have the expertise to provide the right guidance.
Given the high cost of energy in the UK, there is a greater than ever need to reduce operational costs and an energy efficient system can play an instrumental role in this. NHS budgets are under increasing pressure, so an optimally running system can make a big difference to expenditure.
Spirotech is currently working on several hospital projects in the London area including a scheme at one in which a new boiler room is being installed, whilst at another ageing vacuum degassers are being replaced with our S400 model. This is a fully automatic unit for closed heating, cooling and process systems with an operating pressure of between 1 and 4 bar.
Water is the single most important ‘component’ within the system. Get its conditioning right, and it will provide efficient, trouble-free operation. However, during the design and installation stages of many heating and ventilation systems, straightforward problems are often missed, potentially resulting in the system’s fluid quality being seriously compromised.
A poorly installed and maintained pressurisation system can lead to negative pressures around the circuit, causing air to be drawn in through automatic air vents, gaskets and via micro-leaks. Too much pressure can also lead to water being emitted through the safety valves, meaning raw refill water will need to be added. Unfortunately, the newly introduced water will be oxygen-rich and further deplete any corrosion inhibitors in the system.
Releasing dissolved air
Today’s highly efficient heating and cooling systems are designed to work at their most effective with ‘air-free’ water. For larger buildings this requires a vacuum degasser to be integrated with the pressurisation unit.
Vacuum degassers work by reducing the pressure in the vacuum vessel that sits within the unit. This liberates dissolved gases from the system liquid in the vessel and the accumulated gases can then be expelled. These powerful vacuum degassers are needed because ‘ordinary’ in-line deaerators will not work anywhere near as effectively in high-rise offices and other tall buildings. By continuously degassing quantities of the system liquid, the vacuum degasser keeps the negative effects of dissolved and liberated gas to a minimum.
As buildings have grown in size, so the requirements for larger, more powerful vacuum degassers have grown. The latest can degas up to 1,000 litres of liquid an hour. The drive for efficiency and energy saving has also seen manufacturers increase the level of connectivity, with more sophisticated vacuum degassers including ‘intelligent’ controls enabling remote access and operation via ‘the cloud’.
Intelligent controls
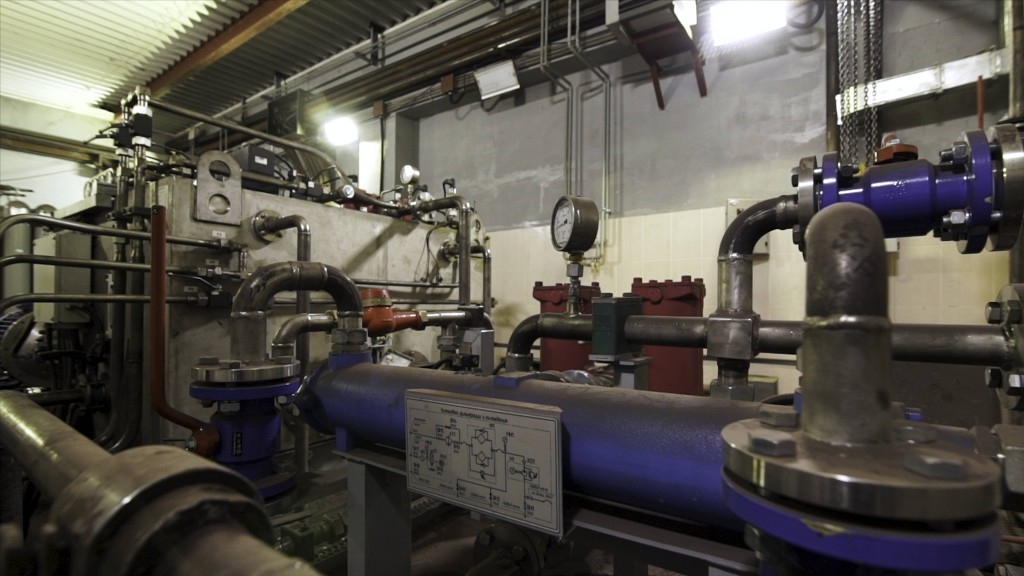
Once commissioning is complete, control and monitoring can be achieved using a touchscreen on the unit, through a building management system (BMS) or via the internet on a PC, tablet or smartphone.
Functions such as on/off, error and alarm reset, and degassing, refill and boiler interlock on/off can be controlled remotely, while parameters can be set for such things as system pressure, refill pressure and boiler interlock.
The most modern feature a comprehensive unit status and event history, providing real-time data and enabling performance to be tracked in detail over time. This higher level of information gathering will, among other things, enable predictive maintenance and servicing, leading to increased reliability and performance, and ultimately cost savings.
There are four issues that regularly crop up around pressurisation in underperforming systems:
• Poor design – the industry is becoming deskilled, especially in pressurisation knowledge.
Industry standards are not followed and shortcuts are taken, with price often dictating. The attitude taken is ‘we’ve always done it this way’, without taking the latest practices into account and sometimes leading to an expensive fix.
• Installationerrors–theexpansion vessel and/or the pressurisation unit is located in the wrong place and sometimes connecting pipework is the wrong size.
• Mistakes in commissioning – the pre-charge and cold fill pressures are incorrect.
• Poor maintenance – there’s a failure to check and adjust the pre-charge pressure of a vessel at least every 12 months.
All the above can be avoided if those involved in the process, from specification to installation, take time to appraise themselves of the latest developments, ensure that calculations are fully worked through and follow best practice, including regular maintenance checks.
For anyone who would like a refresh, Spirotech has developed a CPD which goes into further detail, ‘Understanding Pressurisation Design, Installation and Implementation’.