Hassle-free installation on busy sites.
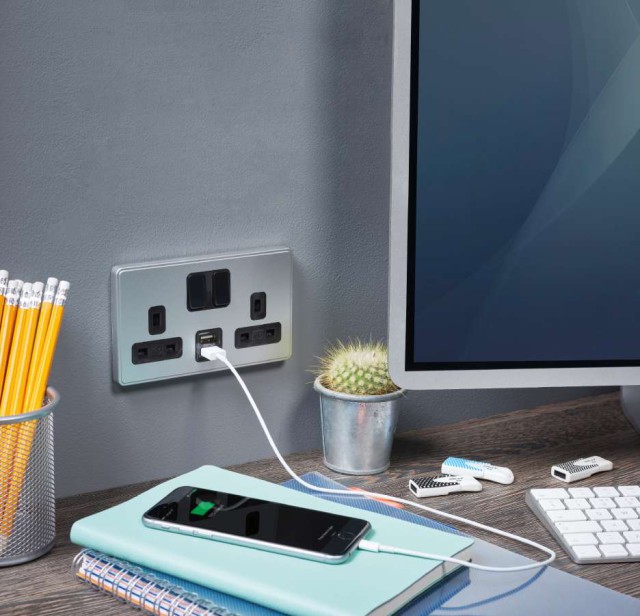
Neil Brown, offering manager at MK Electric, looks at what can electrical contractors and project managers can do to help streamline installations to help save costs and increase productivity on site.
Figures from the Office of National Statistics (ONS) revealed that the UK’s construction output in November 2021 was 1.3% (£197 million) above the February 2020 pre-COVID-19 level.1 While it’s great news for the industry, the additional work that is contributing to the uplift means contractors are looking for new ways to achieve hassle-free installations across tight timeframes.
Commercial construction projects, whether it’s an office building, a hotel or a block of luxury apartments, will be subject to various contractors coming and going. The risk of installations getting damaged – and needing to be replaced along the way – can be high.
Damage limitation
Meeting expectations on a job, both in terms of time and quality, can be a stressful experience for contractors. This can be made even more difficult if products need to be reordered and reinstalled after being damaged on site.
Most contractors will be obligated to fix or replace any damaged installations, so finding ways to minimise potential issues is key to an on-time, on-budget project completion and client satisfaction.
Decorative wiring devices with chrome, brass or matte black finishes can be susceptible to damage during construction. Multiple trades and tradespeople can be working in the same space at the same time so it’s far more likely that sockets and switches will encounter people, materials and equipment, such as ladders and power tools, that increase the potential for scrapes, scratches or other cosmetic damage to the decorative finish.
Wiring devices that provide a two-step installation solution - a functional module which can be installed initially and a frontplate which can be fitted over the functional module during the final staging process – can help both contractors and project managers.
By separately installing the final frontplate, it can be protected from the knocks, scrapes, plaster abrasion and paint splatter which can often occur on a busy site, potentially saving cost and time to replace the product.
Separate installations, separate deliveries
A common problem with wiring devices that come as two parts is that they usually come packaged together. Whilst the functional module may be successfully installed, the frontplate can be easily damaged or misplaced between delivery and final fit. This can be especially problematic for frontplates with decorative finishes selected primarily for aesthetics, particularly with finishes such as brushed stainless steel and matte black, where scrapes and scratches are more noticeable.
Specifically designed to be modular, the clip-on frontplate and functional modules in the MK Dimensions range are individual component products with separate part numbers. Unlike many other two-piece solutions, this means that components can be ordered, delivered and installed separately to align with the project schedule, removing the potential for loss or damage during fit out.
This provides contractors with the flexibility to install the functional module to align to the build schedule and continue working without concern that the frontplates will be mislaid or damaged. Additionally, the option to order the frontplate at a later stage in the project allows for any last-minute changes to the design brief, such as the colour or material used for the front of the socket or switch.
The ability to order the functional module and frontplate as individual components also gives project managers more budget flexibility. With parts on order at different times this can help to keep track of accurate spend. It’s feasible that by the time you need to order the frontplates, you will have a clearer picture of the quantity needed and the finish required, with the need for replacements significantly reduced.
Making the functional, functional
Installing the functional module of a wiring device towards the beginning of a project can supply power for tools and equipment needed on site whilst the build continues. With other two-part products, the socket alone often cannot be used as it may not meet British Standards without the frontplate.
This can be frustrating for contractors who then need to find an alternative power source for their tools and equipment, which may be metres away from the working area. It can also create additional safety concerns for project managers, as extension cables will need to be tested and taped down to avoid trip hazards and site workers made aware of the out-of-use sockets.
A flawless finish
Whilst functionality is something installers always look for, it’s important not to lose sight of the overall look and feel of a project and achieving the client’s vision.
The demand for stylish finishes and fixings is constantly growing. Hoteliers, restaurant owners and landlords are all wanting ‘social media-worthy’ rooms and spaces to compete with the top players in their industry.
Screwless, clip-on frontplates for sockets and switches are not only easier to fit but they also look stylish and blend seamlessly into contemporary spaces. A screwless design also lends itself to changing trends, as they can be swapped out easily to accommodate evolving interior design over time.
This provides scalability across a build, and for single rooms or entire developments to be fitted out with a single common design aesthetic, whilst still offering the option for differentiation through choice of final frontplate finish.
So, whether it’s hospitality or a residential development, contractors working on high-end specs can surprise and delight their clients with more options than ever before.
Getting the job done
When you consider the quantity of sockets that are installed in buildings, particularly as our modern power requirements continue to grow, products that offer time saving and snag reducing opportunities offer benefits to the overall finances of a project.
To help keep a construction project on track, a simple swap to two-piece wiring devices can help make on-site installations more effective and efficient. In addition, a functional module that meets British Standards can help contractors get other jobs done more quickly and easily, whilst reducing the amount of corrective action that will be needed post-install, preventing avoidable expense and completion delays.