Reducing safety risks in the construction industry with packaged plant
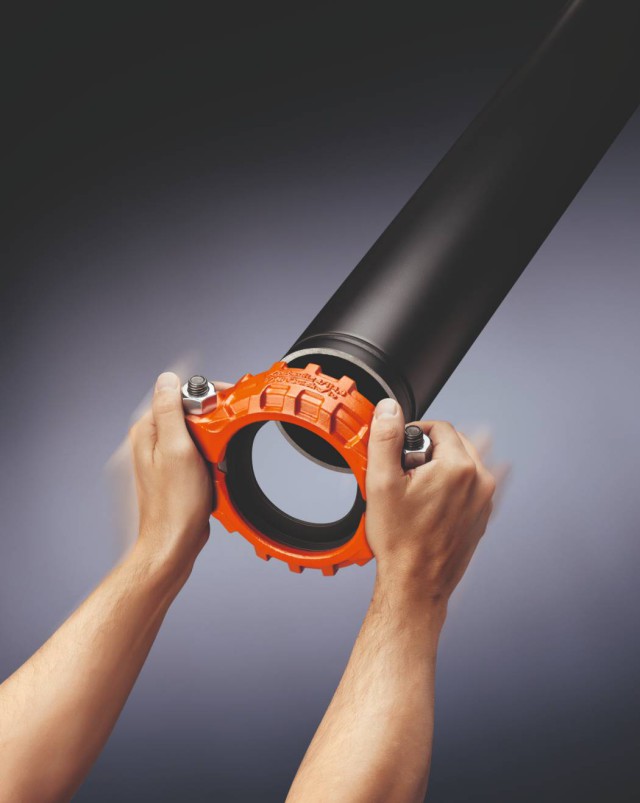
From hazardous equipment to risky situations, health and safety is understandably a top priority in the 21st-century construction industry. According to global estimates, work-related accidents and injuries (although not exclusive to the construction industry) cost the EU €476 billion each year.
The construction industry is acutely aware of the risks. Findings from the Health and Safety Executive showed an encouraging downward trend in the overall rate of self-reported non-fatal injury to workers in construction, prior to the coronavirus pandemic. Whilst there are undoubtedly several causes which may have contributed to this reduction, particularly a decrease in operations during this period due to the economic downturn, it could also be due to a more concerted effort in the industry as a whole to reduce risk and improve safety.
Improvements in safety policies have been brought in at a time of new technological development and adaptation of product design in order to improve safety and prevent injuries. At Victaulic, we look at the issue of safety from many different perspectives, including exploring how our products’ design can boost safety through the three stages of a project’s life-cycle: pre-site, on-site and post-site.
Whilst there is a general standard of safety throughout the construction process, the stages of a project have different safety challenges to consider. From before arriving on site, to the management of installation processes, to maintaining safety standards through regular check-ups, every stage of construction has specific practises which can help alleviate risk.
Pre-site
Companies in the construction sector are increasingly employing the latest technology tools in their operations before getting on to the site. 3D modelling and BIM are revolutionising the construction industry and have expanded into Virtual Reality (VR). This means that construction professionals can immerse themselves in the digital version of their project, which allows them to visualise, amend and mitigate issues before committing to the installation.
Not only does this mean that firms can save money and pre-empt mistakes, but also the time it takes to solve problems on site is reduced, as any potential issues or suggested changes are caught and handled at the design stage. By mitigating any design faults and on-site alterations, the use of VR and BIM can improve the safety level on construction sites.
Following the use of modelling techniques, utilisation of pre-fabricated spools and assemblies is another way Victaulic is encouraging the industry to improve its safety record. Though pre-fabricated products and systems differ in scale, ultimately the benefits to construction safety are universal. By designing systems which can be pre-fabricated off-site, for example, data centre piping systems, site workers are less exposed to risky tasks once on site. As many potential issues have been pre-addressed in a more stable environment, the prefabricated design allows for a more controlled planning of a project.
On-site
Now that we have done what we can to alleviate future risk on the job site through BIM and prefabrication, let’s focus on the job site itself. Easier to install products translates to less time on the job and thereby reduced risk. For example, Victaulic’s grooved pipe-joining systems are three to four times faster to connect than welded or flanged methods and don’t require open flame for installation.
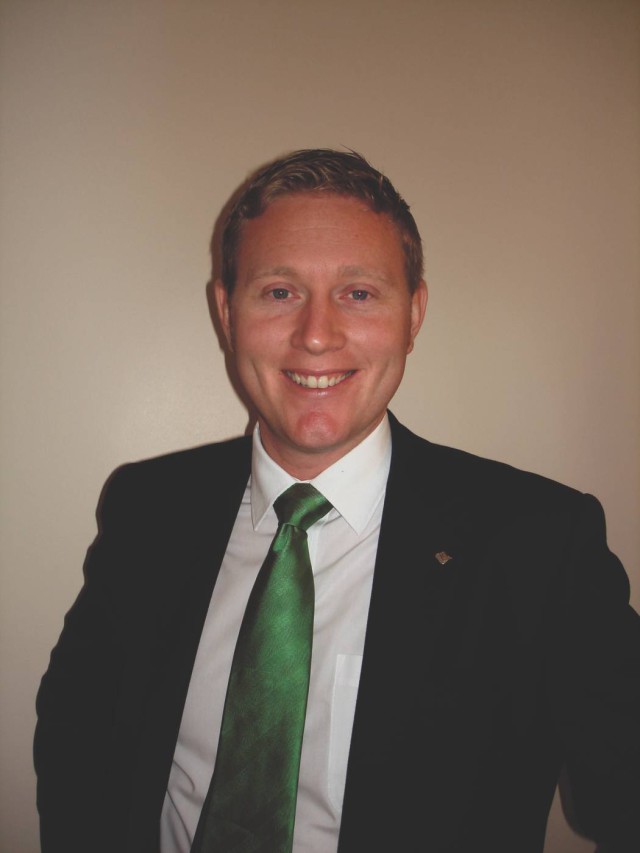
Avoiding welding not only makes construction tasks much safer, but also makes jobsites cleaner and requires less specialised training. Working with an open welding flame can make jobsites more vulnerable to fire and the fumes released by the process are often toxic. The hazards of welding have been said to cause both short and long-term health impacts, such as nausea, irritation of the respiratory system or even cancer, so when it comes to safety, the benefits of avoiding this process are clear. Grooved mechanical pipe joining systems provide an attractive alternative to welding and flanging for engineers, installers and owners alike. They can be quickly, easily and safely installed and maintained in order to meet tight project schedules and operate efficiently. Victaulic’s Installation-Ready™ Technology couplings do not require any disassembly prior to installation and can further help keep the jobsite safer as it limits the amounts of loose parts which can be easily misplaced or dropped.
In addition, as mechanical pipe joints only consist of three parts (the gasket, the housings and nuts and bolts), one can easily install the system without needing to use dangerous equipment. By not requiring any additional man hours, electricity or excessive on-site preparation time, easy-install and flexible product design further reduces the risk of accidents and injuries as it does not introduce any excessive outside threats.
Post-installation
Once products have been safely designed, prepared and installed, the importance of site safety doesn’t finish. The choice of the right product at the BIM phase can ensure that any post-installation maintenance and refurbishment procedures can also be done in a safe way long after a project is completed. This is particularly pertinent in sensitive facilities such as data centres, hospitals and airports, where maintenance work is usually carried out when a facility is open to the public.
For example, when dealing with any systematic maintenance in these situations, it is more convenient that the methods used are flame-free to avoid the risk on fire. This is also the case during refurbishment projects, which often involve delicate materials used in the previous construction and take place in unstable environments which could be damaged by the welding process. Products consisting of only a few parts, which fit together without requiring welding, not only help to speed up the installation and maintenance stages, but also help to reduce the risk of injury in these situations.
Consequently, whilst several factors impact jobsite safety in the construction industry, it is clear that investing in the best designed and most suitable products and ensuring safety throughout the construction process are both integral to the decrease in jobsite injuries at work. The European construction sector has enjoyed a positive period of increasing safety over recent years. Looking ahead, thanks to better technology, innovative products and improved safety standards, jobsite safety levels are expected to improve even further. Victaulic aims to be a central part of that story.
Shaun Hughes is Regional Manager at Victaulic