The art of the possible

Steve Richmond, Head of Marketing and Technical Building Solutions at REHAU UK, discusses the possibilities with offsite construction.
Offsite construction is not new, and the ability to quickly and simply link panels and modules together in a controlled environment has long appealed to developers and M&E contractors when constructing buildings.
However, reports of plumbing leaks and insulation breakdown stemming from inferior components and fittings have shaken the market’s faith in modern methods of construction (MMC). If these concerns can be resolved, the principle of building high-quality properties quickly remains sound, especially given growing demand for building work in high-density urban areas.
These city centre projects are often hampered by space restrictions, and while building upwards seems an effective solution, multiple teams working in cramped conditions can hinder the installation of key building services.
Alongside this impaired quality control, the nation’s ongoing construction skills shortages provides further concerns, with the UK Trade Skills Index 2023 highlighting that 937,000 new workers will be needed by 2032 to meet construction demand.
MMC’s Appeal
Taking these issues into account, MMC methods undoubtedly appeal. Yet while approximately 200,000 homes are built annually, this needs to be dramatically scaled up if the sector is to meet the Government’s target of 300,000. This also does not account for demand in the commercial sector, including for new student accommodation and hotel properties.
It is with these concerns in mind that REHAU has launched its latest guide, Offsite Trends in Building Services. The polymer solutions manufacturer developed the new report to explore the role MMC can play in alleviating pressures currently affecting construction and provide further insight into what is possible using this building method. The ultimate aim is to raise overall awareness of MMC among M&E contractors about offsite construction, development of new building services solutions, and the impact of new technologies and innovations on best practice.
For example, integrating an MMC project’s building information modelling data with bill of materials documents can streamline processes, improving overall quality control and the availability of key components.
As the work is carried out in a controlled environment, material waste can also be reduced by 90% with less distracting on-site noise and reduced risk of tool loss. In turn, this ensures durable, energy-efficient properties can be built cost-effectively at scale despite skills shortages.
Trends and Developments
MMC itself is a fast-moving and broad sector. Multiple installation approaches are possible beyond the offsite sub-assembly approach used in the UK, in which precast elements are made offsite and transported to the site for installation within traditional builds.
For instance, in the European market where offsite construction is long established, innovation continues apace to develop best possible products and practices. This includes the use of volumetric and panel construction approaches, or a hybrid modular method combining the two.
Using the first method, entire three-dimensional elements such as bathrooms can be made in factories to include all plumbing pipes and components such as windows and doors and lifted into place onsite within a superstructure. By contrast, panel construction involves manufacturing wall or roof modules offsite as flat panel units to suit a specific type of housing, with plumbing pipes joined and installed on-site.
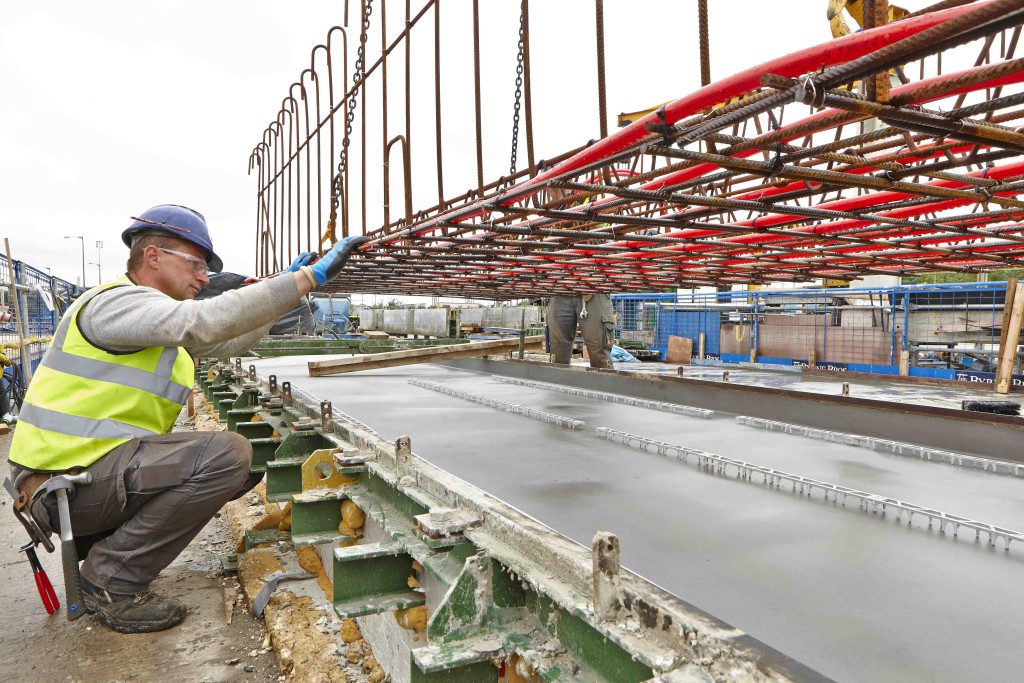
Though these approaches already allow for new and exciting possibilities, emerging methods including timber concrete hybrid construction also demonstrate how MMC can become even more sustainable. Replacing pre-cast concrete panels with this timber composite means less concrete is required and panels can be made lighter, resulting in faster, less carbon-intensive construction.
Keeping updated on advances
It is crucial that building services professionals work with third party experts to ensure they are up to date on advances in this area. Awareness of trends such as the increasing popularity of modular shafts may also provide new possibilities for delivering and directing mechanical services into prefabricated units in a simpler, easier way.
As a result, contractors can save time by stacking individual modules with one shaft per floor in a streamlined, optimised and standardised process.
Polymer risers also offer contractors a way to replicate high-quality work at scale and have also been the subject of continuous innovation. Allowing ducts, pipes and conduits to deliver key mechanical services, these vital components have traditionally been made of copper and steel when used in MMC projects. Yet the introduction of new materials such as fiber-reinforced PP-R which is easier to transport, has allowed contractors to opt for larger riser sizes that can be welded and tested offsite, providing further assurances over performance.
Similarly, the integration of customisable frames into the walls of offsite bathroom builds can offer building services professionals a way to quickly connect various sanitaryware within a smaller space. As a result, time can be saved during the build while also providing easy access for later maintenance by simply removing a wall panel, rather than breaking out the bathroom to find specific pipework.
Opportunities for streamlining construction can also be seen when it comes to construction utility cupboards on MMC projects. A singular area that can be used for building service isolation points, utility cupboards are highly appealing in MMC projects as they can be replicated at scale during construction.
These spaces also suit as a location for modular plumbing components through which washing machines, air handlers and other household utilities devices can be situated for easier maintenance. For example, REHAU’s smart manifold has been designed to be quickly installed and offer a manifold-based plumbing solution which reduces the number of plumbing fittings required by up to three times.
Seeing what’s out there
Although the construction industry is subject to multiple pressures, the overriding target remains high-quality builds, built quickly. With demand increasing across multiple sectors, M&E contractors must identify efficient and effective methods to turn this objective into a reality.
Collaboration with expert suppliers and fabricators is crucial to ensure best installation practices and avoid quality concerns.