Brake failures on lifts, consequences and recommendations
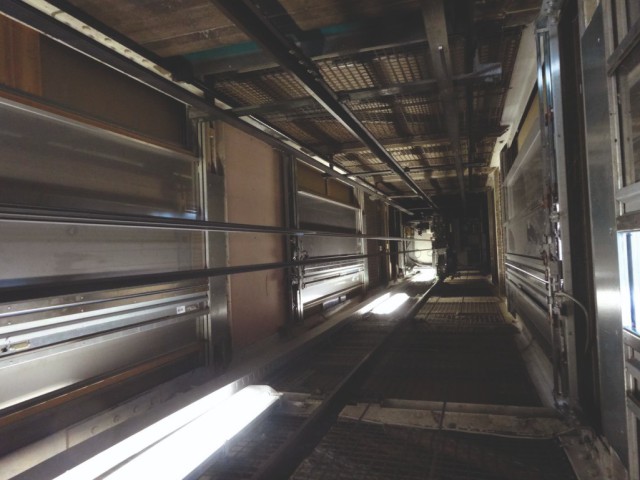
Eur ing Dave Cooper, CEO of LECS UK, outlines the latest developments within BSI standards that govern brakes on lifts and outlines his key recommendations to keep brakes operating safely
Brake failures affect many types of equipment and while efforts have been made in standards to improve the outcome of a brake failure - unfortunately they still occur*.
The consequences of a failure can range from a ‘near-miss’ to fatalities. Many service technicians take the view that with the introduction of variable frequency drives into the lift and escalator industry that the brake no longer needs maintaining. Nothing could be further than the truth.
Thankfully recent standards have been developed to reduce the risk of brake failure, but there are key areas to be aware of and key recommendations that everyone responsible for lifts, whether in commercial or private settings, should be aware of.
The function of a lift brake has changed over recent years with developments in drive systems.
Older systems such as single speed and two speed designs relied on the brake itself to bring the lift to a stop during an ordinary journey and the leveling accuracy would be dependent upon the condition of the brake pads, the load in the lift car relative to balance and the position of the lift in its shaft. With these drive systems the brake was also used to bring the lift to a safe stop in the event of a power supply fault or a control system situation (such as a high speed lock tip). The regular maintenance of the brake with these drive types is vital.
Older but more sophisticated drive systems [such as the DC Ward Leonard system or the DC static converter drive] were designed so that the motor would bring the lift to a stop at a landing and then the brake would apply to hold the lift car for loading/unloading. Similarly these drive systems were required to bring the lift to a safe stop in the event of a power supply fault or control circuit situation.
Modem drive systems [such as the AC VV and the variable frequency drives] are similar to these however maintenance is still required as situations such as high speed lock tips can still occur and cause premature wear of brake pads.
What happens when a brake fails?
A lift can be compared to a set of scales with the heaviest side of the balance equation between the car and counterweight being the side that descends when left to gravity.
In many cases when a brake fails the lift car will run upwards due to the counterweight being heavier than a lightly loaded lift car.
As the counterweight descends, where no compensation exists, the lift car ascent increases in speed as the suspension ropes pay out onto the counter-weight side.
Modem lifts are fitted with uncontrolled movement devices that will detect and arrest a runaway condition but many lifts were installed prior to this recommendation in the standards and do not have such a facility. It should be remembered that uncontrolled movement may be caused by situations other than a brake failure too.
In addition, many older lifts using single speed or two speed drive systems rely on the brake for stopping and the accuracy of the car to landing threshold is reliant on the condition of the brake, position of the lift in the shaft and the load in the car.
Types of brake failure
There are many ways that a brake can fail and these include electrical and mechanical failures. In some cases one or more of these situations can come together to create an uncontrolled movement scenario.
Examples include:
- Brake solenoid going open circuit (single solenoid)
- Brake solenoid going open circuit (twin polarised type)
- Physical wear of brake pad
- Rivets coming loose on brake pad
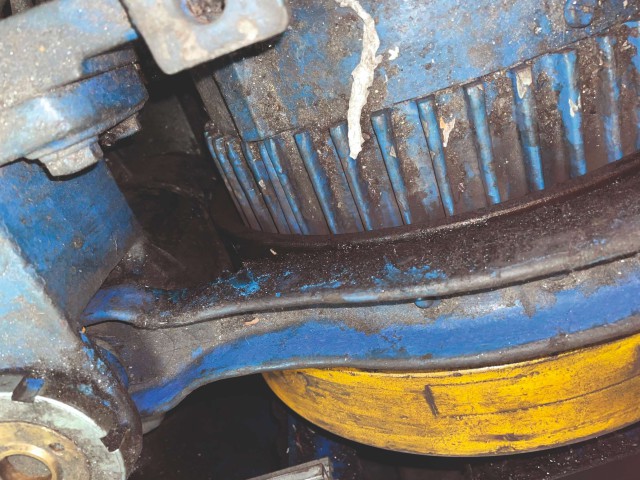
- Lubricant on brake pad
- Stuck in open position - release mechanism failure
- Stuck in open position - other mechanical failure (such as a single line component e.g. a split pin)
- Held in open position - residual magnetism
- System overloaded
- Poor adjustment
- Overheating
Standards
Over the years there have been many improvements in braking systems for lifts including the introduction of the A3 amendment to the EN81-1 standard [Safety rules for the construction and installation of lifts. (London, BSI] for uncontrolled movement however this dealt with the symptom of brake failure rather than the cause.
The current edition of EN81-20 (that replaced EN81-1) includes uncontrolled movement detection and also the requirement for brake components to be in two sets - thus offering redundancy and monitoring of the brake itself for correct operation.
The EN81-80 (2003) standard (Improvement of safety of existing lifts) didn't mention inadequate braking systems however the 2019 version has been expanded to include this situation.
Key takeaways:
1 Older lifts with single line components in the braking system need to be assessed.
2 It is recommended that all brakes should be fitted with lift detection switches.
3 Where modernisation takes place and an old style brake is retained and a variable frequency drive is fitted to replace an older system such as single speed, two speed etc there is a real risk that the lift can drive through a closed brake especially with the lift car in the upper reaches of the shaft.
4 Prevention is better than cure. Methods of detecting the depletion of braking efficiency should be developed so as to detect rather than respond to a failure situation. The potential for uncontrolled movement should be detected before it actually happens.
5 Checking of brake condition and adjustment is still an essential part of the maintenance regime as extraneous situations such as high speed lock tipping can affect braking performance.
*This can be because many lifts were installed prior to the introduction of current standards.