The first commission
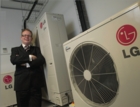
Graham Hendra looks at the importance of getting it right first time, every time, when it comes to commissioning an air-conditioning system.
Commissioning an air-conditioning system correctly is one of the most important operations of the whole installation process. Carried out correctly, it will give the system the highest possible chance of long and trouble-free service to the end user.
How you commission any type of system (whether it be a relatively complex VRF system, large chiller or small single split system) will dictate how that system performs, the lifespan of the system and the likelihood of it breaking down. Inadequately commissioned systems will almost always cause nothing but problems for everyone on the supply chain — manufacturer, distributor, contractor and, last but most important, the end user.
Commissioning involves checking many aspects of the system from installation to operation, recording all measured data, setting up controls, and writing a comprehensive report of all findings.
Checking that the system has been installed according to the drawings and manufacturer recommendations is the first port of call. If the system has been installed outside its piping/wiring parameters, capacity limitations or the outdoor or indoor units unit have been installed in unsuitable locations, there is no point running the system in the first place, as the commissioning data will be meaningless. Not only that, it is almost certain that the system will not operate correctly.
Once it has been confirmed that the system has been installed correctly and all pre-commissioning tests (such as field piping pressure testing, and electrical testing) have been passed by the relevant authorities and checked by the commissioning engineer, only then should commissioning commence.
Once commissioning is complete up to the point of testing the system in cooling and heating (normally in an empty unoccupied building), the next phase of commissioning should be a re-visit of the site after the occupants have moved in.
This post-commissioning visit almost never happens and could be just as important as the commissioning itself. The chances are that the occupants have no idea how to use the equipment and need to be advised. There may also be cases where further settings need to be made — such as air-flow adjustments, temperature control recommendations, optimisation of central controls and setting up time-clocks.
A system can be commissioned to the highest standards, but the end-user will never get the best from it if he does not know how to use it properly and it is not set up correctly. The system may not operate as efficiently as it could, so running costs will be much higher than necessary.
There is also sound business sense behind correct commissioning — it adds to a contractors’ reputation for best practice. Just put yourself in the client’s shoes; we all gravitate to the people or services that look after us the best. And end-user clients also choose the installers which look after them the best — especially during the current tough times in the marketplace.
We have all seen jobs where someone has simply evacuated a system for five minutes, charged it with refrigerant, powered it up, run it, felt the air temperatures with the back of a hand and left site — without even showing the customer how to start and stop the system. This NOT commissioning!
Another point about the commissioning process is that five minutes with the end-user can save you, the installer, hours and hours of call-back time.
A successful air-conditioning installation does not finish with handover; customer service must be at the top of its list for problem-free operation. A post-installation health check on the system along with sound practical advice on how to operate it easily and efficiently will pay dividends in customer satisfaction.
We were recently involved in a project to install three new Multi V II heat recovery VRF systems, which are packed with features to make life easier for both the installation contractor and, ultimately, the customer.
However, no matter how well the units are installed there is always some tweaking to be done to a new system. The problems are fairly simple to solve but to expect a contractor who deals with many different products from a variety of manufacturers to know all of them is not realistic.
The units were installed in phases as the building was refurbished. As expected installation and commissioning went according to plan with minimum fuss. However, after handover a number of issues were raised by the customer, so the contractor responsible for the installation called in LG to fix the problem.
He feared the customer would lose faith in the kit and withhold payment, so we were called in. Once on site we walked through the job and addressed each problem individually. The first to be addressed was the age-old one of people sitting directly in the airflow from a ceiling cassette.
The solution is simple — adjust the vane angles and advise the customer that sitting in a draught is pleasant for 10 minutes, but any longer will drive you crazy. We swiftly altered the angles to cut the draught and, in some units, blocked the airflow from one side. This is a new function on our latest range of cassettes, where each louvre can be operated independently to the other three from the remote controller.
The next problem was temperature control. In some areas the units were overcooling the rooms by as much as 3 K — 20°C rather than 23°C. All our units have a sensor in the fan coil and one in the remote controller. The theory is that the remote controller is mounted near the occupants because sensing the temperature here gives better temperature control where it really matters.
However, a controller on a pillar in the middle of the room will respond to the pillar temperature as well as that of the air around it. To prevent this, we include an insulated pad to be installed behind the controller, which had not been fitted by the contractor. Flicking a switch in the back of the remote controller disabled the function, and the unit could then sense the temperature up at the fan coil.
Such nuisance issues can easily turn customers against a perfectly applied system. Ideally, these problems should be foreseen at commissioning. A return visit a week after handover is costly but can often pay dividends. A happy customer calls out the service engineer less and recommends you as a good supplier of air-conditioning systems.
We hold commissioning courses covering all aspects of commissioning from installation rules, commissioning procedures, through to controls set-up. Once this course has been completed and the candidate certified, they may become a registered LG Multi V II commissioning partner.
Graham Hendra is with LG Air Conditioning.