Offsite pre-fabrication is crucial for sustainable refurbishment
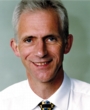
As the country steps up efforts to tackle the sustainability of existing buildings, offsite pre-fabrication of building-services modules is set to play an increasingly important role, says Paul Cooper.
The challenge of improving the performance of existing buildings is being driven hard by Government legislation and by occupants determined to reduce their running costs.
Owners and managers have, somehow, to improve internal conditions for comfort and health, minimise disruption to the day-to-day operations of the building — while ensuring that energy costs are slashed and the building’s carbon footprint minimised. There must be easier ways to make a living!
The Carbon Reduction Commitment Energy Efficiency Scheme (CRC EES) is a potentially game-breaking piece of legislation that will force commercial energy consumers to focus closely on the cost of their carbon emissions. Medium to large sized organisations such as manufacturers, hotels, banks, local authorities, supermarkets, larger chain shops and schools will be included in this mandatory carbon trading scheme, which is designed to fundamentally change the behaviour of energy users.
Around 20 000 organisations will be, at least partly, affected by the CRC EES because they will have to disclose information about their energy usage patterns. At least 4000 organisations will be directly affected if their total half-hourly electricity consumption exceeds 6000 MWh a year during the qualification period, leading to full participation in carbon credit purchasing.
It also seems likely that, under the terms of the revised Energy Performance of Buildings Directive (EPBD), the private sector will become subject to mandatory Display Energy Certificates (DECs) that show actual energy consumption.
All this is aimed at improving the existing building stock and will ignite a major programme of refurbishment projects later this year as building operators rush to meet their commitments.
Reducing energy demand should be the first step in any refurbishment strategy. There is no point building in more sources of energy, no matter how ‘green’, until you have first minimised how much energy the building actually needs to consume.
What energy demand is left needs to be met as efficiently as possible. This means looking at getting back to basics and improving the heating plant, looking at types of lighting used in the building, updating system controls or installing them for the first time etc.
Only then, at the third stage, should you consider renewables.
But how can facilities managers speed up delivery of these changes, get better certainty about the finished product, keep the project costs under control and still be sustainable — oh, yes, and do it without totally disrupting the running of the building? The answer has to be offsite prefabrication. Pre-fabrication is now a well established approach in new build projects, but it is now also coming into its own in the refurbishment arena.
Being able to deliver complete, pre-commissioned plant to site on time and with minimal waste looks increasingly attractive in any circumstances, but particularly when you can ill afford delays and expensive equipment downtime. The costs of having to shut down operations are particularly transparent in the financial and retail sectors.

Also, with many building-services refurbishments, you can end up adding complexity and increasing your failure rates as new systems fail to integrate with what is already there.
Offsite pre-fabrication allows systems engineers to factory test the finished article and pre-commission complete plantrooms and ancillary systems before they are delivered to the building. This is the very foundation of sustainability because it reduces waste, improves health and safety, cuts costs and delivers a quality end product; it ticks all the boxes.
13% of all materials used in construction projects are simply thrown away, adding to our catastrophic landfill problem. With the offsite approach, components are sized to fit in advance, and offcuts can be re-used. The supply chain is also more manageable as suppliers are bringing materials to a factory rather than a building site, allowing fabricators to establish a strategy for minimising waste and packaging.
Pre-fabrication reduces site traffic and noise for the benefit of the local environment and community. It cuts down disruption in an operational building because whole sections of the project can be brought in at once, reducing the amount of work that has to be done on site. And, best of all, it makes commercial sense because time is money and putting things right on site is a hugely wasteful and expensive process.
Pre-fabricated systems are factory tested, and the contractor only has a minimum of pipework connections to make. The equipment arrives already pre-tested and commissioned, so the engineer can have confidence that it will work first time.
We cannot hold off improving our existing buildings any longer, but, at the same time, we must not compromise sustainability in a frantic effort to meet legislative and commercial deadlines. Going offsite means that not only can you make your building more sustainable but also that you do it employing a process that is, in itself, sustainable.
Paul Cooper is managing director of offsite fabrication manufacturer Ormandy Group. www.ormandyltd.com