Retrofit opportunities for CHP
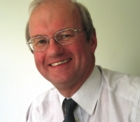
The continuing pressure on capital budgets and the need to tackle long-term running costs are stimulating the market for small-scale combined heat and power (CHP) in the retrofit market. There is increasing demand for a carbon-saving technology that can be applied in existing buildings without massive disruption to day-to-day operations or expensive re-modelling of existing services.
Our new Government also seems to have recognised that throwing money into subsidies for expensive renewables is not necessarily the best route to follow. The budget restraints that have forced the cancellation of the Low Carbon Buildings Programme (LCBP) and the ongoing uncertainty over the Renewable Heat Incentive (RHI) suggest the focus must now be on improving energy efficiency through low carbon retrofits that are largely self funded.
The new Part L of the Building Regulations, which comes into effect later this year, has also radically altered the way in which the carbon content of electricity is calculated — making it more difficult for building owners to comply. The revised carbon-emissions factor used in the SAP calculating software is expected to increase the grid CO2 emissions by 23% from 0.422 to 0.517 kg CO2 per kWh. This could affect the viability of electric heat pumps, mechanical-ventilation systems, and air-conditioning units and makes the ability to self-generate electricity on site even more valuable.
This shifting regulatory framework and the steady rise in energy prices are pushing more and more building managers towards using mini-CHP (up to 50 kW electrical output) as the lead technology in refurbished building-services systems. Long-term accounting systems, such as internal rate of return, and the need for improved energy security makes a strong case for CHP if the facility has a significant heat load.
A building that needs heat and power for around 5000 hours a year (12 hours a day and seven days a week) is a perfect application for CHP, and the end user will see a significant financial and carbon saving.
Leisure centres and swimming pools, hotels, hospitals, sheltered housing, fire stations, schools and many others and will keep the CHP unit working almost continuously. This is when it is at its most efficient, as all the time the engine is running it is producing electricity. A buffer tank can also be used to absorb and store excess heat for release into the heating system when required and, vitally, eliminate on/off cycling that can reduce the efficiency of the engine.
Accountants are also delighted that the purchase cost of the CHP engine is subject to a lower VAT rate of 5% and is supported by Enhanced Capital Allowances, which reduce the owner’s tax bill. And the electricity produced is exempt from the Climate Change Levy to further improve the lifecycle viability of CHP.
The CHP unit can be easily integrated with existing services and controlled via an integral control module that monitors the condition of the system and ensures optimum operating efficiencies.
CHP systems can also be used in trigeneration systems to also provide cooling with the addition of an absorption chiller that uses the heat from the system to generate chilled water and further cut electricity consumption.
However, the key consideration for many building operators is the installation and commissioning time. The availability of complete system packages, such as the Dachs SE Condensing from Baxi-SenerTec, which comes complete with a buffer vessel and all heating system components including an integrated control unit, is a major benefit. The fact that these systems can be retrofitted into existing plant rooms and, in many cases, will free up valuable space has proved to be as appealing to many facilities managers as the considerable energy savings.
For example, at Clayton Street in Newcastle Upon Tyne the existing communal heating system for 243 social housing units was fed from a boiler house in a basement. When the decision was taken to upgrade the heating to improve efficiencies, two Dachs units were integrated into the existing system to act as lead heating appliances feeding both space heating and domestic hot water.
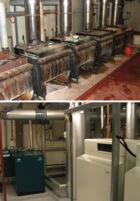
Two of the three existing boilers were retained to provide top-up heating to satisfy peak demand. The remaining redundant boiler was removed to vacate space on the existing concrete plinth now occupied by the two mini-CHP units.
Access into the boiler room was limited, so both CHP units were dismantled to be lowered safely into the basement plant room via a ground-floor access platform and then reassembled in-situ on the existing concrete plinth. The number of Dachs units selected was determined by the base thermal and electrical loads of the property, and they operate in parallel with the local electricity supply infrastructure with any additional electricity required imported from the grid.
Similarly, the Town Hall of Nuneaton & Bedworth Borough Council in Warwickshire has integrated a DACHS mini-CHP system and four Potterton Eurocondense Plus 160 boilers in place of seven ageing gas-fired boilers and two gas-fired water heaters. The original boilers, installed in the mid-1980s, were obsolete, and spares were not readily available. The boilers were also prone to faults, breakdown and high maintenance and repair costs and could not meet modern efficiency standards.
The four condensing boilers were set up in line formation on the original boilers’ concrete plinth base, and the packaged, ready-to-install mini-CHP was installed alongside. The whole system at the Town Hall is controlled by local interfaces and the council’s networked building energy management system, which ensures that the boilers operate only when required to provide additional heating and hot-water capacity.
Heating replacement is often a distress purchase, and, while reducing carbon emissions is a target, the main priority is to improve efficiency and reliability while maintaining good heating and power supplies with the minimum of disruption and cost.
The configuration of modern mini-CHP packages means they can be speedily integrated with existing services, while simultaneously reducing a building’s carbon footprint by 30 to 35%. This is proving to be an increasingly appealing combination for many building managers and owners.
David Shaw is business manager at Baxi-SenerTec UK.
www.baxi-senertec.co.uk