Carbon emissions contained
In meeting the ever-more stringent requirements of Part L of the Building Regulations, every little counts. John Garbutt explains how pre-insulated ductwork can deliver some remarkable savings.
Insulating ductwork to help conserve energy has long been an important aspect of energy-efficient-building services design. Ductwork air-leakage also impacts on energy use, yet has only recently been recognised as a significant factor in design calculations. This article looks at how the approach to air-leakage changed in 2010 and examines research that supports the effectiveness of this relatively simple measure for cutting carbon-dioxide emissions in non-domestic buildings.
The latest revisions that came into play in October 2010 to both Approved Document L2A (ADL2A) to the Building Regulations in England and Wales and Technical Handbook Section 6 to the Building Standards in Scotland, have brought us one step closer to zero-carbon building, with challenging new targets for reducing carbon-dioxide emissions to be met.
Until this time, the National Calculation Methodology (the core calculation engine for demonstrating compliance with the Building Regulations/Standards) was limited to calculating carbon-dioxide emissions on the basis of only Class A or B ductwork air-leakage, so the full effect of air-leakage on carbon-dioxide emissions could not be modelled.
However, the latest version has introduced two far more stringent ductwork air-leakage classes (C and D) in accordance with the classifications outlined in BS EN 1507: 2006. Research has shown that these classes can, and will, play a part in meeting carbon-reduction targets.
Environmental Design Solutions (EDSL) used TAS 9.1.3a to model the annual effect of different ductwork air-leakage rates on four example buildings: two office blocks; a sports hall; and a warehouse-sized retail unit. It was found that in the offices and the sports hall the increase in whole-building carbon-dioxide emissions for Class A ductwork air-leakage compared with Class C was 2.1 to 2.6%. Although these figures may not seem significant in their own right, in the context of the more demanding 2010 requirements they could mean the difference between a building either meeting or failing to meet its carbon-dioxide emissions target.
What’s more, incorporating this kind of improvement need not significantly add to costs. Pre-insulated ductwork offers a cost effective solution that is inherently capable of delivering savings in carbon-dioxide emissions. This is underpinned by a recent case study comparing the air-leakage rates of two differing HVAC ductwork systems, insulated to the same standard: pre-insulated ductwork and traditional sheet metal ductwork lagged with glass fibre.
Our case study is Luther Home of Mercy, a not-for-profit organisation founded in 1928 to care for people with developmental disabilities.
Recent increases in demand created a need for two new 650 m2 residential cottages, which became the focus of an independent study carried out by HVAC specialists, MDA Engineering Inc.
The two virtually identical buildings presented a unique opportunity to compare two different ductwork systems, providing valuable empirical data. One installation comprised a conventional sheet metal duct system lagged with glass fibre; the other used pre-insulated ductwork fabricated from the Kingspan KoolDuct System. The HVAC systems consisted of four high-efficiency furnaces, cooling system condensing units and ductwork located in the vented attic.
Both ductwork systems were designed to meet the same performance standards at 500 Pa static pressure.
Extra attention was paid to the joints of the sheet-metal system which was constructed with sealed longitudinal Pittsburgh Lock seams and sealed drive slip and S slip transverse joints.
An independent testing contractor performed the leakage tests on the entire run for both systems, as opposed to the standard industry practice of testing a sectioned off portion, to provide a more accurate reflection of the actual volume of air-leakage.
To conduct the subsequent analysis, three building models with the same physical characteristics were created in Trane Trace 700, a commonly used energy analysis program. Model 1 was a building with perfect ducts and no leakage. Models 2 and 3 represented buildings with pre-insulated ductwork and metal ductwork, each with their respective operating leakages.
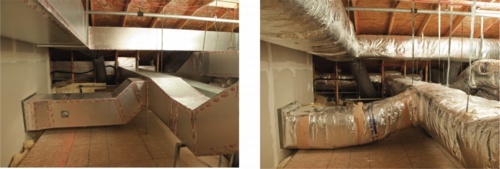
The results showed that the pre-insulated ductwork system had 80% less leakage and cost less. This was despite the fact that the metal-duct system had been constructed with great attention to sealing and installed at the lowest price from competitive bids.
The results included the following key findings.
• Recorded operating leakage for the pre-insulated ductwork system was nearly 80% less than the metal duct system.
• The measured air leakage rate of the sheet metal system was more than three times the specified maximum allowable.
• First-year operating costs, as a result of leakage for the pre-insulated ductwork system, were calculated to be 70% less than the metal-duct system, with overall HVAC operating costs 7% less.
• The pre-insulated ductwork was projected to have an energy saving of 7 MWh per annum and 211 MWh over 30 years.
• Using local average energy mix CO2 generation data, the pre-insulated ductwork system is predicted to save an estimated 5.7 t of CO2 annually (170 t over 30 years) compared to the metal duct system.
Before the latest version of the National Calculation Methodology, the airtight benefits of a pre-insulated ductwork system would not have been recognised in compliance calculations, but as the Luther Home of Mercy case study clearly demonstrates, it can make a very real contribution towards achieving the necessary carbon reductions.
Full details of the Luther Home of Mercy study and the EDSL research are available on request.
John Garbutt is marketing director with Kingspan Insulation.
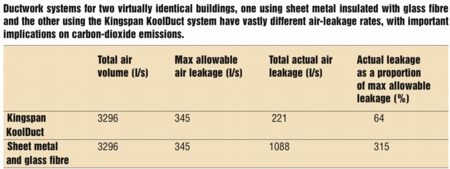