Off-site construction shows its worth at new Birmingham hospital
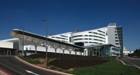
The prefabrication of mechanical and electrical components away from site saved over 450 000 man hours during the construction of the new Queen Elizabeth Hospital in Birmingham, as part of a variety of measures aimed at creating a greener building. Construction company Balfour Beatty, which built the £545 million hospital, sees the project as a highly successful example of how design, manufacture and installation can help deliver a sustainable and cost-efficient new healthcare facility.
The hospital has 1231 patient beds, 30 theatres and the largest critical-care unit in Europe. It took five years to build.
Balfour Beatty will rent the hospital to University Hospitals Birmingham NHS Foundation Trust for 30 years. Graham Hackett, estates and design manager with the trust said that the use of sustainable construction had helped ensure the new hospital was ‘very energy efficient’.
The time savings included a reduction of 112 220 h of hot works on site, 156 480 h of manual handling and 183 840 h of working at height.
Off-site manufacture included designing and building over 600 shower and WC pods, helping to complete the £230 million M&E package 12 months ahead of schedule.
Other off-site work includes over 300 ward wall modules incorporating electrical accessories, medical gases, nurse call and lighting. There are also over 1800 modules supporting ductwork, pipework and cabling.
Mr Hackett said, ‘Balfour Beatty did an awful lot of off-site prefabrication, which kept their costs down and enabled them to complete each of the six phases of the hospital ahead of programme.’