New steam traps make visible savings at Burton on Trent brewery
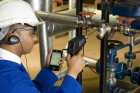
A year on from upgrading its steam traps, Marston’s Brewery has saved £60 000 in energy and hot-water costs. The new equipment from Spirax Sarco prevents steam escaping into the brewer’s condensate-recovery systems and also improve the site’s environmental image by eliminating visible steam emissions.
‘You used to see plumes of steam exiting the plant, but now that’s all stopped,’ says Colin Watson, senior engineer at the brewery. ‘I used to tell the fitters that I’d know they’d done their job when steam stopped coming out of the condensate tank in each section.’
Stainless-steel sealed inverted bucket steam traps have replaced about 70 old steam traps aged from 10 to 40 years. The brewery changed them all rather than individually checking each trap for faults.
As the work progressed, Marston’s took the opportunity to remove trap bypasses from the system. Bypasses enable condensate to be redirected around defective steam traps but can encourage bad practice by enable the steam system to carry on operating at a sub-optimal level rather than forcing engineers to fix defects immediately.
The brewery makes about 300 000 barrels of beer a year. Brands include Pedigree, Old Empire, and Burton Bitter, and draught Bass. Steam is used throughout the process, as well as for space heating.