Building on experience
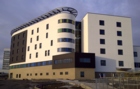
Having successfully exploited off-site manufacture for a major hospital project, Hulley & Kirkwood and Balfour Beatty were well place to use it again for another hospital — which is also designed for low carbon emissions.
With the new acute facility at Kirkcaldy’s Victoria Hospital in Fife having now been handed over and set to open to the public in 2012 comes the opportunity to stand back a little and consider some of the engineering highlights of this £170 million project. The project was completed on time and to budget with Hulley & Kirkwood Consulting Engineers as services designers to Balfour Beatty.
Two notable features of the project are the extensive use of prefabrication for the M&E elements of the project and an energy centre with two biomass wood-chip boilers and a CHP unit.
The energy centre is a key part of Hulley & Kirkwood’s holistic low-energy low-carbon design, which has contributed to a B-rated Energy Performance Certificate — an excellent achievement for the design of a highly serviced acute hospital facility.
This new acute hospital has over 50 000 m2 of accommodation. It includes 11 operating theatres, three of which are UCV laminar-flow vascular theatres. There is also an interventional radiology theatre, catheter lab theatre, endoscopy clean room and diagnostic suite with CT scanner and X-ray machines. The ward for infectious diseased has 10 single HBN 4 style isolation rooms. Other facilities include an emergency-care centre and 20 wards with a total of 508 beds. There are surgical and medical assessment units, maternity unit, women and children’s unit, and facilities for day intervention, critical care, coronary care and renal and dialysis.
The use of offsite prefabrication followed on from its use for the Queen Elizabeth Hospital in Birmingham, again a project on which Balfour Beatty employed Hulley & Kirkwood and a high level of collaboration took place. That was a bigger project, about two and a half times the size of the 50 000 m2 of this latest project, says Michael O’Donnell, director with H&K’s Edinburgh office.
Using offsite prefabrication for the M&E elements of the Victoria Hospital project provided a more sustainable way of delivering the scheme by reducing waste. It also reduced man hours by 270 400 h compared to a traditional M&E approach. That saving looks like a considerable improvement on the Queen Elizabeth Hospital, where 450 000 man hours were saved by producing M&E components away from site. Given the relative size of the two projects, one might have expected a saving of 150 000 h, so the additional 120 400 h saved represents 45%.
![]() |
Among the technologies in the hospital’s energy centre is a 750 kWe CHP unit and woodchip boilers. |
The savings using prefabrication were achieved by H&K spending a year after detail design and during the early construction phases carrying out co-ordination of the services installations. This information was taken into account in the design and manufacture of the off site pre-fab corridor and riser modules produced by BBES Modular Systems + team. Delivery to site was planned and executed to match the construction of the steel frame and metal decks and crucially prior to any internal partitioning commenced.
This level of collaboration continued through construction, with the Hulley SFM team providing commissioning-management support up to handover to ensure knowledge transfer to BB Workplace and NHS Fife occurred in a sensible and controlled manner.
Michael O’Donnell summarises, ‘The new facility at Victoria Hospital, Kirkcaldy, is a highly successful example of how a carefully considered design, co-ordination and construction method derived through designer/contractor collaboration can help to safely deliver a sustainable and cost-efficient new healthcare facility.’
At the heart of the energy strategy is the new energy centre, which provides the electrical supply and standby power generation for the entire site.
It also features a 725 kWe combined-heat-and power plant, two 1 MW wood-chip boilers, thermal accumulators, 300 m3 below ground bunker for the wood chips and automatic wood-fuel feed system for the biomass boilers.
Finally, there are three 6 MW dual-fuel gas/oil-fired boilers, one of which is a standby boiler for resilience.
The new energy centre also serves the retained estate on the site by supplying a new MTHW distributed heat source. The existing retained estate steam mains are to be decommissioned over time and replaced with this low carbon heat source.
The CHP unit provides base-load heat demand and power for the new facility to reduce energy costs and carbon emissions. It is expected to reduce carbon emissions by over 700 t a year.
If the CHP unit cannot meet the demand, the biomass boilers and thermal accumulators are brought in. They also reduce energy costs and carbon emissions by a further 700 t a year.
![]() |
Extensive use of offsite manufacture for services modules reduced time on site by 270 400 hours compared to a traditional M&E approach. |
![]() |
The new unit itself has been designed with enhanced thermal insulation and glazing. It was briefed before the 2007 Building Regulations came into effect, but is designed to be significantly better than those requirements.
Dynamic simulation modelling of the building and envelope by H&K identified the optimum levels of thermal insulation for walls, floors, roofs and glazing. In addition, solar glazing to those facades exposed to the Sun resulted in smaller heat gains.
Air-handling plant for ventilation includes heat recovery to recover about 800 kW of heat from exhaust air systems.
The air-handling plant also has inverter drives to the supply and extract fan motors to allow air volumes to match design requirements. The inverter drives also run plant at part load when areas such as operating theatres are not in use through presence detection.
Pump motors also have inverter drives so that flows can be matched to design requirements. Pumps are also set up to match load through variable-flow regimes on variable-temperature heating systems.
The building is designed to maximise the use of daylight, with daylight sensors to control the electric lighting. In addition, lighting is controlled in some areas by occupancy sensors.
To help keep the building running efficiently, the building-management system monitors energy meters to enable the early recognition of operational problems so they can be diagnosed and rectified quickly. H&K is employed by Balfour Beatty to provide energy monitoring and reporting for two years post handover in order that the design and operational realities can be aligned to produce the optimum energy-efficient plant set up for the long term.
And finally, this new facility has achieved a NEAT (NHS Environmental Assessment Tool) Excellent Rating.