Rethinking refurbishment
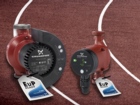
Unlike computers, pumps are not out of date before you get them out of the box, but they are out of date when the time comes to replace them. Glynn Williams puts the case for a rethink when that time arrives.
No-one would ever dream of buying an exact copy of a piece of electronic equipment that they had bought 10 to 15 years previously as they would be only too aware that technological advances would mean that they could get a much improved version. But is the same true of other, perhaps even more fundamental, energy-using products that are to be found in every single commercial building in the UK?
We know that pumps consume 10% of the world’s electrical energy and have for decades been central to many aspects of commercial buildings. They play a pivotal role in maintaining a buildings’ internal equilibrium and, therefore, its inhabitants’ well-being. Their replacement cycle is about15 years, and the decisions made at the point of replacement have important long-term energy ramifications.
As a pump manufacturer we are very aware that the entire replacement issue can be a ‘grey’ area that often slips under the energy-use/best-practice radar. Maybe because it is often service support staff who decide when a pump has reached the end of its useful life or perhaps because of the complexity of repair or the unavailability of particular spare parts. Then it is all too often a scenario where the details are simply read off the pump plate and an identical pump is reordered, or the closest alternative if an identical pump is not available.
The pump industry, like many businesses driven by engineered solutions, is constantly evolving. It can be likened to the motor industry in many ways, especially for the dynamic pace of change that it has experienced in the past 20 years, particularly in the development of solutions that are more energy efficient. However, even though there are similarities, most people change their car every two to three years, so a 15-year pump lifecycle makes it even more important that the right decision is made when the replacement cycle does come around.
When the pump or pump set was first specified, it would probably have been sized to meet an original duty or flow against a pressure. An additional 10% leeway was often added, purposely built in to cover ‘eventualities’. This over-sizing was (and in some instances still is) common practice. In fact we estimate that 95% of the current installed pump base, in HVAC applications in particular, is incorrectly sized because of the addition of sizing-in for added comfort but also because pumps are sized on maximum demand, even though pumps will only need to work near the end of their curve for at most 5% of their lifespan.
The first step should be to review the current system requirements, as this will often lead to a more efficient pump selection that will offer the benefit of reduced energy consumption.
Once the correct duty has been ascertained, the next step is to check out the most energy-efficient solution currently available. Heating circulator pumps make up most of the replacement market within commercial services, and glandless circulators are the favoured choice because of their compact design and low maintenance. Glanded products with mechanical seals are, however, more efficient and can be fitted as a direct replacement for glandless circulators in some cases.
From 1 January 2013, an EuP Directive comes into effect that will require glandless standalone circulators, with the exception of those specifically designed for primary circuits of solar-thermal systems and heat pumps to have an energy efficiency index (EEI) of not more than 0.27. Stricter changes are scheduled to take place in 2015 and 2020.
As the motor is the energy-sapping aspect of the pump, special focus should be given to it. Where conventional motors are used they should be as efficient as possible. To simplify the various current national standards that exist for motors, a new IE standard (International Efficiency class) has been adopted.
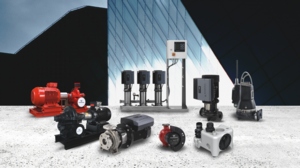
• IE1 — standard efficiency (comparable to EFF2)
• IE2 — high efficiency (comparable to EFF1)
• IE3 — premium efficiency
Making the best pump decision really does add up. A 20% reduction in speed returns a 50% reduction in energy consumption, and a 50% reduction translates into a huge 87% saving in electrical consumption — all based on cube-law principles. In fact switching to high-efficiency motors would reduce electrical consumption by the requirements of 11 million people – the population of Greece.
Many factors are improving pump efficiency. They include improvements in pump design, improved tolerances in manufacturing, better testing and, when in the field, ease of service, accessibility of spare parts and a wide range of ancillary products that support the infrastructure they sit within.
Make sure advantage is taken of the latest technological advances by choosing to reselect every time a pump needs to be replaced. That way you will know you have achieved a win/win — by reducing energy usage and decreasing the building’s carbon footprint.
Glynn Williams is sales director for commercial building services with Grundfos Pumps.