Future uses for carbon dioxide refrigeration
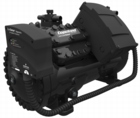
The use of carbon dioxide as a refrigerant has a chequered history, but it is becoming established — with a whole raft of potential applications. Andy Pearson of Star Refrigeration provides an insight into the technology.
Carbon dioxide is one of the natural substances identified as suitable for the early refrigerating systems developed in the mid-nineteenth century. It proved to be extremely popular, particularly for small systems and where safety was paramount — for example on board ships.
Its use continued well into the twentieth century, only fading in the 1950s when R22 became more widely available. Concerns about the effect of fluorocarbons on climate and the environment have led to the rediscovery of this versatile and effective refrigerant, and since 1990 it has been applied to a wide range of cooling needs.
A carbon-dioxide system operates at higher pressures than most other refrigeration systems — one of the main reasons that it was superseded 60 years ago. However, several facets of this property help to explain the reason for its renaissance.
It was first applied as a refrigerant when steam engines were still relatively new and pressure containment was a significant challenge.
Nowadays the pressures required in a typical diesel engine’s fuel injection system are over 10 times higher than those required for CO2 refrigeration. Modern materials, designs and production techniques make it possible to produce compressors and other components that are cheap, compact and lightweight.
The high operating pressure also makes carbon dioxide very efficient as a refrigerant due to the high gas density and low pressure ratio required in a typical system.
The ratio of gas to liquid density also makes 2-phase heat transfer in evaporators and condensers very effective.
For higher-temperature applications, the gas is pressurised beyond the critical point, so that heat rejection to atmosphere is achieved by cooling dense gas rather than condensing liquid. This enables a wide temperature range to be used effectively on the heat-delivery side while maintaining near-constant temperature on the heat extraction side of the system, making trans-critical carbon dioxide uniquely attractive for heat-pump systems.
Carbon dioxide has recently been used in low-temperature freezers, cold and chill stores, supermarkets, direct air-conditioning systems for high-density heat loads and high-temperature water heaters. This has led to recognition of ‘The A-B-C of CO2 systems’.
A stands for ‘Absolutely not the right thing to do’ — such as a delicate and expensive evaporator that forms part of a larger system and cannot be replaced, as in a jacketed milk or beer tank or a chocolate-enrobing machine.
B is for ‘Borderline’, describing situations where CO2 is one of several viable solutions, delivering some benefits but not the only way to deliver the cooling. Most cold- and chill-store applications, supermarkets and car air-conditioning are in this category.
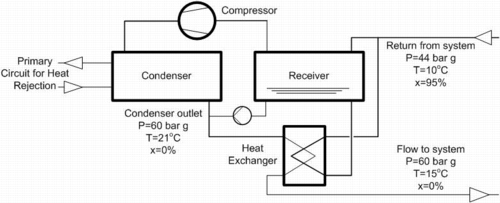
C indicates that ‘you’d be Crazy not to use CO2’. This includes low-temperature plate and spiral freezers, where carbon dioxide delivers freezing time performance that is at least twice as fast as the best alternative systems, and high-density IT cooling where the heat exchangers are significantly smaller than equivalent alternatives and can be installed in a wide variety of ways not appropriate for conventional solutions. Such applications include blade servers in data centres and underdesk cooling of PCs for trader floors in banks.
The compressor, the heart of the cooling system, is the most challenging part of the development program, and great progress has been made in the last 20 years. These machines can be divided into large and small, and high-temperature and low-temperature.
Low-temperature machines are available across the whole size range, from a few hundred watts to several megawatts of cooling capacity. They typically have a discharge pressure rating of 40 to 50 bar and are used in cascade systems.
High-temperature machines can operate up to 130 bar, for trans-critical heat rejection to atmosphere or in heat-pump applications, but so far have only been developed for up to about 100 kW of cooling capacity. This is typically a volumetric capacity of about 40 m3/h, still very small compared to ammonia or R134a compressors.
So what does the future hold for carbon dioxide cooling?
It will continue to be used in all the areas that it has entered in the last 20 years, including IT cooling and car air-conditioning, although it is currently only applied in niche applications. Subject to continued technical development in compressors, condensers and other components, we can also expect to see carbon dioxide gain a presence in some new areas.
Larger compressors would enable medium-pressure district-cooling systems delivering liquid carbon dioxide at an evaporating temperature of 10°C, with the returning vapour being compressed from 44 bar to 60 bar and rejecting heat to a high efficiency R-134a or ammonia system with free-cooling capability.
The technology used in dealer floors could also be applied to chilled beams in general offices, perhaps combined with the district-cooling system, offering a significant reduction in the energy used for pumping water, which is often a more significant electrical consumer than the water chiller in a typical variable-load building.
Andy Pearson is group engineering director with Star Refrigeration.