Pursuing energy efficiency
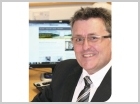
Where energy efficiency is concerned, heating manufacturers and specifiers are setting themselves new challenges to deliver maximum efficiencies and energy savings at all times, says Mark Northcott of Remeha Commercial.
It’s official. Energy efficiency has replaced renewables as the Government’s new buzzword. November saw the DECC launch the UK’s first national Energy Efficiency Strategy as part of its aim to kick start ‘a revolution’ in UK energy efficiency across all sectors.
Improved energy efficiency will bring financial and environmental gains to businesses, helping us meet our carbon commitments and increase profitability. As we move to a low-carbon nation, focusing on energy efficiency will help bridge the energy gap between our current energy demand and the small proportion (3.8%) of our energy that is provided by renewable energy. After all, according to research by the Lawrence Livermore National Laboratory in the United States, 56% of all energy generated in the world is wasted.
For manufacturers of heating equipment, the drive for improved energy efficiency is far from new. Given that heating and hot-water production alone account for nearly half the UK’s energy consumption, manufacturers have been innovating with a whole of range of different heating technologies. All have the same aim — to develop cleaner, smarter systems that will provide quality energy, reduce carbon emissions and lower fuel bills.
With the financial crisis far from over and energy prices continuing to rise seemingly inexorably, affordability is key to businesses ‘buying into’ energy efficiency. Where heating is concerned, while renewable technologies continue to require a large financial investment, the humble condensing boiler is probably the most cost-effective way of bringing substantial energy savings. This is particularly true when we consider the nation’s large proportion of old building stock, where refurbishment is often the only solution.
Manufacturers have responded with new models that are quicker and easier to install in refurbishment projects, more flexible, more versatile and with a smaller footprint, and fully modulating for higher efficiencies and cleaner combustion than ever before.
As a result, the challenge for manufacturers and specifiers today is to ensure not only that the most appropriate products are used in a particular project within the budget framework, but that these products are used as efficiently as possible to achieve their maximum potential. Manufacturers, specifiers and consultants must set themselves the goal of best system design for maximum system efficiency if the full energy savings of our heating equipment is to be realised. At Remeha Commercial we call this maximum seasonal efficiency level ‘Blue efficiency’.
To understand how we can achieve the greatest energy savings, we need to understand the difference between combustion efficiency and seasonal efficiency.
Boilers have to respond to mild days, cold days and very cold days — adjusting or modulating their output, which affects their efficiency. Condensing boilers can achieve a range of efficiencies of up to 107% NCV down to the standard 80% with higher flow and return temperatures. The challenge is to maximise efficiency at all times. One simple step is to add appropriate control to help a boiler deliver more usable energy.
The minimum control strategy should encompass valved zone control, thermostats and timers. Further improvements can be achieved by sequential control of boilers, 2-zoned temperature and time control, and weather compensation — all of which advanced controls like the Remeha iSense Pro provide, helping the system use less energy and increase seasonal efficiency.
Systems with heat recovery also increase seasonal efficiency by delivering a higher attainable level of efficiency of 107% NCV for all energy at all times and all temperatures. Systems like the Remeha Quinta Eco Plus use passive flue gas heat recovery devices to achieve full-time maximum combustion efficiency. For every £100 or energy input, such a heating system would deliver you £97 of usable energy. A ‘Blue efficiency’ system that incorporates ‘super-condensing’ systems with controls would deliver energy savings of about 20%.
Another area where system efficiency could be improved is in bivalent heating systems, where a condensing boiler supports renewable equipment. Specifying a boiler with a secondary-return feature would allow both components to work at their full potential and achieve their maximum efficiency levels over the course of the year.
The Government is throwing down the gauntlet to businesses to follow the energy-efficiency path. Where heating is concerned, the industry should use its experience and knowledge of its products to push the boundaries of accepted efficiencies and reduce unnecessary waste. With the ‘Blue efficiency’ philosophy, we at Remeha Commercial look forward to doing just that.
Mark Northcott is managing director of Remeha Commercial.
Knauf Insulation enjoys benefits of super-efficient boilers
![]() |
Maximum condensing at full output at all times is the key to the full-time attainable efficiency of 107% NCV for the Remeha Quinta Eco Plus boiler. Note the four passive flue-gas heat-recovery devices near the top. |
Knauf Insulation recently took a leaf out of its own energy-saving book when it upgraded the heating at its Cwmbran plant to two ‘super condensing’ Remeha Quinta Eco Plus 115 PFGHRD heating systems. With the new systems in place, Knauf is looking forward to a reduction in energy use for heating of up to 40% with a financial payback of 18 months.
The existing 30-year-old boilers were wasteful and inefficient compared with modern condensing boilers. However, even high-efficiency boilers typically waste around 20% of energy when run at high loads and high temperatures. The Remeha Quinta Eco Plus PFGHRD heating systems ensure maximum condensing at full output at all times, achieving a new level of full-time attainable efficiency of up to 107% NCV at 82/71°C flow and return temperatures.
‘The Quinta Eco Plus is pre-plumbed and configured, so installation came down to a simple wheel-in and connect fitting, which meant less downtime for Knauf Insulation,’ said Andy Norman of MII Engineering Ltd.
‘This heating system is simple to install, hugely space saving — Knauf gained a whole new office space — and will bring welcome energy savings. I’ve already recommended it for other refurbishment projects.’