Boiler, boiler on the wall...
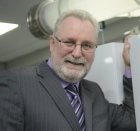
The market for commercial boilers has shifted in recent years away from floor standing units and towards wall hung appliances. John Bailey of Vaillant, explores the factors contributing to this.
Demand for wall-hung boilers for commercial applications has been steadily increasing in recent years. Five years ago, wall-hung boilers accounted for half of the commercial boiler market; today they represent two-thirds of sales.
Floor-standing boilers will, of course, remain in demand, particularly for sites with a very high demand and ample plant room capacity, but wall-hung units are set to dominate the commercial boiler market.
This shift has been predominantly driven the advent of higher-output variants.
The new range of 80, 100 and 120 kW wall-hung boilers recently launched by Vaillant is indicative of how far things have come in a comparatively short space of time. The models almost double the output previously possible from an ecoTEC boiler without any compromise on performance and efficiency.
As someone who’s been in this industry for not far off 40 years, I find these outputs and performance statistics extraordinary. Aside from the technical advances that are making this possible, there are several factors influencing this evolution, not least cost, efficiency, installation and performance.
Inevitably, cost has become an almost overwhelming influence across the board. It’s also inextricably linked with most efficiency, installation and performance objectives. We’re all under increasing pressure to do more with less, and, naturally, this is having a heavy influence on the specification decisions made.
Wall-hung units hold the trump card here over their floor-standing counterparts. In general terms and despite the complexity of the technology within their modest casings, they are less resource intensive to manufacture, transport and warehouse and, therefore, retail at a lower price. They also generally cost less to install and commission in both respect of the expertise required and the cost associated with getting the plant onto the site.
The development of modular cascade rigging has stretched the cost differential further. Cascade rigs, where wall-hung boilers are mounted to a floor-standing framework, until recent years have typically involved contractors fabricating their own rigs to suit the particular needs of the site and system. While solving a logistical challenge, custom-built rigs do have a time, expertise and material, and therefore cost, penalty.
Vaillant, for example, has recently taken this engineering solution to the next stage and developed a range of modular rigging which allows up to eight boilers to be installed inline, back-to-back or in a corner without any requirement for costly custom builds or flow and return pipe or flue assemblies. The rigging is assembled in kit form on site, with all system requirements integrated up to either a low-loss plate heat exchanger or low-loss header for connection onto the system. The cost of the rig is more than offset by the saving on the cost of an intricate installation taking several days.
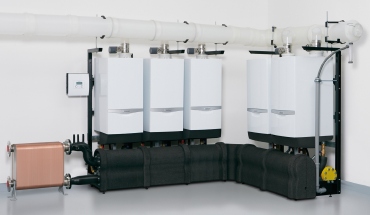
Beyond the capital investment in new plant, clients of course also have an eye on the rolling operational costs. Again, wall-hung boilers offer two distinct advantages: cost of maintenance and, when in a cascade, operational efficiency.
Efficiency has risen to the top of the agenda in recent years as organisations seek to combat rising fuel costs with more efficient plant. Legislation, incentive and self-imposed corporate responsibility is also encouraging the specification of the most efficient systems.
Individually, wall-hung boilers are not necessarily more efficient than their floor-standing counter parts, but they do offer significant gains when specified in a cascade thanks to the extremely wide modulation range this format permits. In the case of ecoTEC, a cascade of eight 120 kW boilers with sequence control can modulate from as low as 30 kW to as high as 960 kW, giving enormous flexibility of heat output.
Utilisation of multiple appliances also offers a number of advantages, including high operating reliability and maintenance flexibility (single units can be taken offline for maintenance or repair without affecting neighbouring appliances in the cascade) and the ability to extend the system if demands change.
A further, but frequently underestimated, influence concerns plant rooms. Smaller plant rooms, plant rooms with challenging access or plant rooms bursting at the seams with the paraphernalia of modern building systems are common scenarios facing installers and engineers on a daily basis. Increasingly, systems designed around smaller wall-hung units are required to overcome these challenges.
The final driver is performance — not simply the performance of the boiler itself but the long-term performance of the total system. Longevity of service, low noise, intelligent control, fail-safe operation and low-impact maintenance are today common requirements on the specification paperwork. While these requirements are not the preserve of wall-hanging models, the fact is, once again, that they hold the trump card on most points.
I feel that is it important to repeat a point made at the beginning of this article; floor-standing boilers have an important role to play and will continue to feature in system specifications for years to come. But the technical advancement of wall-hanging appliances, and demands for cost reduction, efficiency and performance mean this sector is set to flourish in the future.
John Bailey is director for commercial systems with Vaillant in the UK.