Low-water-content boilers — popular for a reason

Low-water-content boilers are typically the first choice for commercial applications. Peter Gammon of MHS Boilers compares boilers with low and high water content to explain why they are so popular.
Oh here we go,’ I hear you cry, ‘another manufacturer bragging about how its products perform better than the rest!’ Well, to avoid such reproach, and in the spirit of fair debate, we should look at the pros and cons of both high- and low-water content boilers. After years of information blurring the lines between the two versions, as well as boilers from different manufacturers competing against each other, there is often a misunderstanding of the advantages and disadvantages of each type.
Which type offers the most efficient system? Can they both be used in the same applications? And, is there a financial advantage from using one over the other?
If we simply consider the overall efficiency levels of the boilers, there is unlikely to be much difference. Likewise, if we carry out a seasonal efficiency calculation for both boiler types (based upon the calculation methodology given in the ‘Non-domestic building services compliance guide’), we again see little difference.
However, if you take the weight of water contained in a high water content appliance into consideration when comparing running costs – particularly over the boilers lifetime — the higher water content unit will consume far more fuel to bring it up to working temperature from ambient standby.
To illustrate this point, let’s take a typical modern premix gas-fired low-water-content condensing boiler, with an output of 1043 kW at 80/60°C and a heat input at maximum rate of 1183 kW. The water content is 117 litres (kg), and the time taken to bring that water from an ambient standby temperature of 20°C to a flow temperature of 80°C is 28 s. In terms of energy input, this represents 9.2 kWh.
Conversely, if we look at a typical high-water-content unit of similar input and output, with an average water content of around 1100 l (kg), the time taken for the water mass in the boiler to reach operating temperature is 264 s and an energy input of some 88 kWh, which equates to a difference of some 78.8 kWh per heat-up cycle. Depending on the system/building’s working regime, this disparity in heat up consumption over the lifetime of the boiler plant, usually 15 to 20 years, could equate to considerably higher costs. Further, carbon emissions will also be some 9.5 times higher per heat-up occasion.
It has also been suggested by some manufacturers that a low-water-content unit suffers under low loads, as they circulate a high volume of freshly heated water back to its return port via the low-loss header (boiler-system interface) — an assertion that is not strictly true.
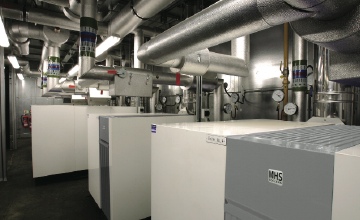
As high-water-content boilers don’t require a minimum water flow, they are often seen as a superior option. However, the Ecodesign Directive requires high-efficiency pumps to be used (since 1 January 2013) and to comply, manufacturers of low-water-content appliances supply speed-controlled pumps to match the delivery of heated water to the load, thereby avoiding recirculation and impairment of the boiler’s capability to operate in condensing mode.
The heat loads of buildings vary constantly, and a well-planned installation of low-water-content boilers provides a flexible heat-generation service that is quick to respond to increasing or decreasing changes in load. This allows very high, real-load-driven operating efficiencies that are not damped by the effects of high-water-content inertia.
The main feature in favour of the high-content appliances is their ability to be installed with no particular water-flow requirements. However, as a consequence, they are considerably heavier, which puts additional weight loadings on the building structure and, in addition, causes slower response times, considerably higher costs to heat-up from a cold start, greater heat-up-time emissions, a potential increase in water-treatment chemicals, plus the requirement for larger system expansion vessels. Consequently, in most commercial applications, low-water-content boilers steal a march on their competitors.
There are, of course, plenty of considerations to take into account when specifying low- or high-water-content boilers. Although there will not always be a one type fits all approach, low-water-content boilers are sure to remain the most popular option across the commercial sector. Ultimately, they provide more flexibility in plant location, as well as a greater potential for energy savings over their life time — pre-requisites for any installation surely?
Peter Gammon is technical manager with MHS Boilers.