The BMS as the key to energy efficiency
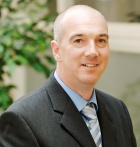
Whilst a building management system (BMS) is key to the control of mechanical and electrical equipment within larger commercial buildings, a number of additional considerations have to be made in the case of retrofit installations. Pete Mills of Bosch Commercial & Industrial Heating, explains the best measures to take when incorporating energy-using products into an existing BMS to manage emissions.
What has to be taken into account from the outset of any large-scale heating installation is the manner in which the heating sources can be managed and monitored by a BMS. Aside from technical specification of the heating technologies themselves, what also has to be considered is the make-up of the BMS, as the overhaul of an existing system can prove extremely costly.
When a new installation takes place ‘from scratch’, it is relatively straightforward to ensure the BMS has all the suitable credentials to allow the system to operate at maximum efficiency. The BMS code can be written to make sure all technologies are accounted for and done in a manner that keeps the control and monitoring of all associated technologies in one place.
What we find with existing BMS reconfigurations, however, is that when new heating sources are installed, the costs associated with the adjustment of the BMS can prove extremely high — and in some cases, could even make the install unviable. It is therefore hugely important to take advantage of the variety of dedicated heating controls manufacturers can often specify prior to any installation work taking place.
’Off-the-shelf’ controls offer a wide range of control options for single- and multi-boiler systems, as well as being able to incorporate renewable technologies such as solar-thermal collectors. With the ability to connect these sophisticated controls into a BMS, the management of emissions and the overall efficiency of the heating appliances can be maximised to its full potential.
It is important to remember that when a BMS is in place, it is programmed with a code, which essentially maintains the smooth running of the mechanical and electrical equipment within the building. A common occurrence however, is for a pre-written code to be transferred over from one BMS to another, in the misplaced belief that each system, if using the same technologies, will operate in the same manner. Unfortunately, no two systems are the same so this approach is likely to compromise the overall efficiency and the emissions from the system.
In incorporating a specific, sophisticated heating-control system, the specifier is essentially able to hand over certain parts of the control from the BMS to the dedicated heating-system controller. This is particularly valuable when it comes to bivalent or multivalent heating systems, where two or more heating sources are combined to enhance efficiency. The more complex the heating system, the more intricate the BMS control program required, which therefore opens up an opportunity for a manufacturer’s bespoke heating control to share the load and ensure the heating side of the building’s requirements is operating to its full potential.

Since the introduction of Part L2B of the Building Regulations, extensive control systems for heating and hot-water technologies have been more than a mere enhancement of the appliances installed, but a mandatory requirement. Part L2B lays down minimal operation seasonal boiler efficiency levels which are based on average boiler efficiencies operating at 30% and 100% output, with all gas boilers in new buildings having to achieve a minimum of 86%.
Minimum control packages are also required, according to the boiler output. All new installations must incorporate timing and temperature controls, which must be zone specific for buildings with floor areas over 150 m2. Weather compensation is required unless a constant-temperature supply is needed. Installations between 100 and 500 kW are also required to have optimal start/stop control with night setback or frost protection, 2-stage firing for multiple boilers, measures to limit heat loss from non-firing modules and sequence control for multiple boilers. Boilers over 500 kW must also have fully modulating burner controls.
The rules for existing buildings are more complex than the equivalent for new buildings. Natural gas boilers must achieve a minimum of 82% boiler seasonal efficiency, have zone controls where the building floor area is greater than 150 m2, and room thermostats and time clock controls as a minimum. However, the overall performance of the whole system must achieve the 84% level, and this is made possible by gaining Heating Efficiency Credits for additional controls or functions added to the basic specification.
Given the incentives on offer, the building-management system has a vital role to play in the awarding of Heating Efficiency Credits, particularly when, as suggested earlier, a sophisticated level of heating control is connected.
The latest generation of heating and hot-water appliances offer greater flexibility than ever before, and technologies such as gas absorption heat pumps and CHP can combine with a boiler to enhance efficiency. Using an intelligent control system to strategically spread the load across these technologies will be the key to curbing emissions, before the BMS is called to action.