Flues and boilers in harmony
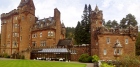
Flues play a key role in every boiler installation, with condensing boilers and biomass boilers posing particularly problems — as Chris Laughton explains.
High-efficiency boilers place extra demands on chimney systems. This is due to the lower natural buoyancy of flue gases as they leave the outlet of the appliance. Sometimes these flue gases are so low in temperature (because of the high appliance efficiency) that the moisture within starts to condense.
If the chimney system is correctly designed, this can be a desirable way of reclaiming further latent energy, although condensation can also be quite damaging due to the risk of corrosion if this is not correctly anticipated during the design stage. There is also a risk of ice formation at the chimney terminal on freezing days.
In general, low-temperature flue gases usually need fan assistance to create sufficient positive pressure to move the gases through the appliance and flue connector and then into the vertical chimney. However, with many appliances, particularly with certain fuels such as biomass, chimneys have historically been run under a natural draught — hence at a slight negative pressure. It is important at the outset to make the decision whether to design instead with a positive-pressure flue.
![]() |
3D drawings helped with the layout design of boiler plant rooms for two biomass boilers at Glenborrodale. (Image: Euroheat) |
The relationship between pressure, temperature and rate of mass flow is complexly influenced by the laws of fluid dynamics. To simplify matters when complying with building and emission regulations, basic codes or approved documents are often used. These vary between the various devolved regions, but what underpins them all are sets of European standards which help to categorise components and provide design calculations allowing for consistent analysis throughout.
A common standard used to specify chimneys is BS EN1443: ‘Chimneys – general requirements’. For example, using that standard, a minimum specification for burning wood might be ‘T400 N2 D 3 Gxx’, where each set of digits describes an important characteristic.
The European standard used for performance calculations is BS EN13384, which is in two parts. Part One is for single appliances, and Part Two is for multiple appliances — including cascading of flue connector pipes. Using such European standards is an increasingly important part of the design process for combustion-based plant rooms.
Where the choice exists, multiple-boiler (bivalent) systems should be considered for better contingency and minimum-load matching. In such cases with multiple combustion appliances, considerable savings on chimney costs can be made if a chimney and/or flue connecting pipe can be shared between multiple appliances. However, this is not always technically possible and can conflict with regional codes, although this is generally supported by European standards, provided the chimneys run at similar pressures.
Biomass boilers have recently been the subject of particular focus due to the current availability of the Government’s Renewable Heat Incentive (RHI). This regularly pays the owner of a commercial appliance for combusting biomass, typically wood chips or pellets.
Industry estimates suggest that by 2020 renewable heat will have grown to supply 25% of the heat demand of commercial enterprises paying business rates on premises from schools and hospitals to retail shops and smallholdings. End-users not only get regular RHI payments for 20 years according to a metered supply but also the potential savings that come from using a cheaper fuel. It would not be unusual to expect a combined annual benefit approaching £40 000 for a 200 kW chip boiler replacing oil. Over 20 years, this would significantly offset capital and running costs.
![]() |
Chimney calculation software can be used to prove design compliance with European standards. (Image: KESA-aladin) |
With the RHI, more premises are becoming commercially viable for biomass than ever before. This comes at the same time as increasing emission requirements require chimney performance to be optimised. Different boilers have different draught requirements, and comparing the options is an onerous task. This is why software is fast becoming an essential design tool, used to perform dynamic chimney performance calculations and to plan layouts in 3D — as the following case study demonstrates
The boiler replacement and biomass conversion for Glenborrodale Castle presented difficulties, as the Grade 1 listing mitigated flue appearance and terminal locations. Ultimately, the only option was initially to pass the flue connector horizontally towards the external wall of an old stable block, through a wall, and then allow the chimney to pass vertically up. Due to the complexity of this unusual design, two important software applications were used in tandem.
KESA-aladin chimney calculation software was first used to prove that the chimney performance would comply with BS EN13384-2. Secondly, a 3D CAD package was used to ensure the layout would work within the space. The chosen appliances were a pair of HDG Compact 200 wood chip biomass boilers supplied by Euroheat and installed by Edge Renewbles with FRA flexi blade wood-chip feeding system. Choosing wood-chip as the fuel allowed the owners to claim RHI payments while making use of trees grown on their own land. This produced a peak output of 199 kW per boiler. A pair of 3600 l accumulators was used to even out load fluctuations.
The KESA-aladin software demonstrated that it would be possible to set the twin-wall flue connector and chimney components at 300 mm diameter with a 6 m-high chimney. The software showed that this system would meet temperature and pressure requirements, even though it required three 45° bends and one 90° bend with a long horizontal run along the top of the boiler. The boilers each had a turn-down to 57 kW, necessary as the building is a hotel and hot water is required all year.
Estimated fuel-cost savings against the previous LPG boilers were around £16 000 per boiler per year. These benefits were particularly high because the owner was able to use fuel from their own land. The potential RHI payments were £22 488 per boiler per year, bringing the total financial benefit of this system to around £76 976 per year as set against initial capital costs and the ongoing running costs of boiler and fuel.
Chris Laughton is managing director of The Solar Design Company