The evolution of cast-iron boilers
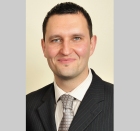
Cast-iron boilers have stood the test of time and evolved — and they continue to develop to provide effective solutions that can be integrated into existing heating systems — as Hamworthy Heating’s Liam Elmore explains.
Cast iron is a proven material that has stood the test of time, demonstrating its reliability over many years. It has been used for the manufacture of boilers since the late 19th century when the first coal-fired cast-iron boilers were produced. In the UK at this time there were many foundries that could cheaply and easily make the large components required. Cast iron was also chosen for its tolerance to sulphurous flue gases — a by-product released as a result of burning coal which has high sulphur content.
In 1956, when the Clean Air Act was introduced, we saw the move from solid fuel to town gas and oils and with that the arrival of steel as a viable material for boiler heat exchangers.
Once natural gas became readily available this opened the door to all types of metals and more refined manufacturing processes. Today we see boilers manufactured in a range of metals from steel, stainless steel and aluminium, to copper and cast iron.
Historically, cast-iron heat exchangers have been constructed using sectional designs that remain in use today. Early designs used sections that stood vertically, like a sliced loaf of bread, with the system return entering at the bottom of the rear section. Flow throughout the sectional assemblies was not always even, and some boilers relied on the use of flow distribution tubes to help direct flow to the front sections of the heat exchanger.
![]() |
Modern cast-iron boilers, such as Hamworthy’s Purewell VariHeat are much more efficient than traditional designs — and when operated in a multiple installation are even more efficient. |
In the late 1960s Hamworthy introduced a heat-exchanger design using horizontal sections stacked one above the other. System return water entered the bottom section and flowed towards the front, where it would rise into the section above and flow towards the back, again rising into the next section above. Using this series-flow arrangement resulted in a naturally balanced flow path throughout the boiler.
The design also allows for simple replacement of a single section, if required. Plus if access to the plant room is restricted, a particular problem with existing plant rooms in need of refurbishment, the boiler and heat exchanger can be quickly dismantled into manageable sections and reassembled in situ.
The waterways in a cast-iron heat exchanger are larger than typical lightweight wall-mounted boilers, making it more tolerant of demanding system conditions often found in existing heating systems and particularly suited to projects where the boiler plant, not the entire system is being replaced.
Some regard cast-iron boilers as inefficient, and cast iron as an old-fashioned technology. These impressions are gained partly due to the less-efficient control systems that were fitted on many of the old cast-iron atmospheric boilers still out in the field today and also because those boilers did not have the condensing functionality of many modern boilers.
The efficiency improvements between old atmospheric cast-iron boilers and newer condensing cast-iron models are vast. The efficiency gains are even more evident on multiple boiler systems with the use of intelligent controls.
Consider a system designed for a peak demand of 280 kW using four 70 kW boilers (Fig. 1). With old on/off atmospheric boilers, the plant's maximum turndown ratio is 4:1 — meaning the plant can be turned down from 280 kW to 70 kW, but only in 70 kW steps.
If an off-peak demand period ideally requires a constant 95 kW of output to maintain a heating circuit at a set temperature, then to meet that demand two boilers would need to run together. The plant would then produce 140 kW which is 45 kW more than necessary.
![]() |
Fig. 1: Diagram showing the improvement in turndown and efficiency on multiple-boiler systems with cast-iron boilers. |
When the required temperature is attained, one boiler would turn off, and the other would continue alone at 70 kW until the circuit temperature dropped to a point which triggered the second boiler to turn on again.
Using today's fully modulating 70 kW condensing boilers, the example plant's turndown ratio increases to around 13:1. Moreover, infinite speed control of the burner fan speed burner enables the incremental adjustment of each boiler's output power between part and full load to be far more precise.
With a multiple-boiler programmable controller the appropriate number of boilers can be set up to fire and modulate together to accurately respond to variations in demand in the most efficient manner — increasing overall plant efficiency with improved load matching of the entire boiler plant to the building’s heating load profile.
Improved turndown ratios and typically higher outputs of modern condensing cast-iron boilers over their predecessors, as well as better-insulated buildings, means that when refurbishing a plant room there is often the opportunity to reduce the total number of boilers used and so make savings in the overall cost of purchase and installation.
Cast iron still has its place in manufacturing, and in particular commercial-boiler design, to provide high-efficiency, future-proof and long-lasting products that can easily be integrated into an existing heating system.
Liam Elmore is northern regional sales manager with Hamworthy Heating.