A simpler approach to voltage optimisation
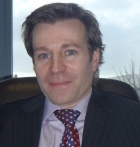
Jeremy Dodge of Marshall-Tufflex describes how a simpler approach to voltage optimisation can deliver benefits more quickly and at less cost.
Controlling energy consumption is imperative for organisations actively managing fuel bills, but it is difficult to achieve when capital budgets for environmental initiatives have been cut, frozen or re-allocated.
Specifiers and their clients are caught between a rock and a hard place — the will is there, but budget may be lacking for serious investment in energy saving systems. However, where there’s a will there is a way in the form of energy-saving solutions that require lower investment levels yet offer meaningful savings, fast payback, quick installation and little or no maintenance/user involvement.
Voltage-optimisation (VO) systems are a good example. Investment in R&D has recently brought to market a raft of new, smaller off-the-shelf VO units, from entry level upwards, equipped with multi-tap transformers, allowing engineers to select the most appropriate tapping level during installation and at any future point should mains voltage levels change significantly.
These quickfix systems offer several benefits.
• Cheaper than bespoke units, which have historically delivered the highest performance.
• Quicker, and therefore cheaper, installation.
• Off-the-shelf availability allows faster project completion times.
• Smaller and lighter, so easier to site.
• Installations may not need an in-depth energy audit, further reducing the cost of a project.
• Choice of three tappings setting; decision can be made on site at point of installation, simplifying the specification process and future proofing installations.
Units with multi-tap transformers allow installers to select the most appropriate tapping level on site and return at any future point to re-adjust if mains voltage changes significantly. We advocate three tapping settings (for mains at 245 V or above, at 240 V or at 235 V), with the voltage being dropped by 11%, 9% and 6%, respectively. For incoming mains of 240 V and above, savings of 10 to 20% are achievable, depending upon site demands, power utilisation profile and incoming power profile.
The multi-tap transformer approach is available on both high-spec and entry level ‘no-frills’ units. Entry-level units are suitable for users who do not have voltage-dependent equipment and whose electrical consumption is characterised by consistent, steady loads where intelligent control for more dynamic loads is not always necessary. They deliver a simple 3-phase VO solution that is easy to source and install, is not built to a specification and which is smaller and more cost-effective than more sophisticated systems.
High-spec multi-tap units offer a more sophisticated approach, with automatic, seamless, neutral-switching bypass (ensuring the VO unit never drops voltage so low as to cut power to site), intelligent control (important to maximise savings) and remote monitoring.
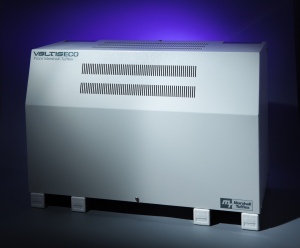
Voltage optimisation does not make savings on all electrical systems. It can deliver substantial savings, for example, on 3-phase induction motors, probably the most common type of 3-phase load used in a variety of equipment — including refrigeration, pumps, air conditioning, conveyor drives etc. The de-rating effects of overvoltage and 3-phase imbalance on AC motors are well known. Excessive overvoltage results in saturation of the iron core, wasting energy through eddy currents and increased hysteresis losses. Drawing excessive current results in excess heat output. The additional stress of overvoltage on motors will decrease motor life.
Electronic equipment is designed to provide a fixed output regardless of supply voltage. ICT-equipment power demand will not change if the voltage varies, so the potential savings are negligible.
Reducing the input voltage to variable-speed drives will result in a proportionate dip in output voltage, so the drive will draw less current and eventually consume less power. However, if the motor is running on high load, the dip in voltage will result in reduced torque, and the motor will draw more current and power.
Heaters will consume less power but produce less heat, resulting in no saving.
Testing of LEDs commissioned by the Energy Systems Trade Association’s voltage-management and optimisation group looked into the impact of VO systems on the effects of supply voltage on LED light output and power use. Typical light outputs were obtained and normalised, with the output of each type set at 100 lm at 245 V. Optimising the mains voltage by 10%, from 245 V to 220 V, delivered an 8% power saving but only a 1% decrease in lumen output. The variation between 230 and 220 V was also examined; tests indicated that 4% savings could be made with minimal, and most probably imperceptible, loss of brightness.
Incandescent lamps (standard tungsten filament, tungsten halogen and reflector lamps) are voltage dependant, so they will provide savings when optimised, but may result in lower light levels.
Fluorescent lamps of the modern electronically controlled type will show negligible savings. Older types may provide savings, but lower voltage/power may result in lower light levels.
Voltage optimisation is a highly effective approach to managing power bills. Savings of up to 20% achievable with the added bonus of prolonging equipment life. By reducing the kWh required, additional savings will also result in a reduction in Climate Charge Levy and kVA charges.
Sub-metering is another approach; it does not directly make savings but can provide in-depth energy data to allow organisations to highlight where savings can be made. Fixed or portable sub-metering units can cost from just a few hundred pounds but have the potential to save thousands.
There is also the option of savings on individual pieces of equipment, for example boiler plant. Commercial-boiler-manager units are straightforward to install and can return savings of up to 20%.
Jeremy Dodge is head of marketing and technical services with Marshall-Tufflex.