The challenges of commissioning variable-flow systems
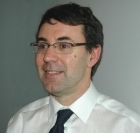
Chris Parsloe of Parsloe Consulting shares his experience of issues that he comes across regularly when carrying out design reviews and trouble-shooting work.
Variable-flow systems, whereby pump speed is varied in response to changing system demand, have been with us for nearly 20 years. And yet there are still regular examples of variable-flow systems that have been designed and commissioned with little obvious understanding of the principles of variable flow.
The critical difference between constant-flow systems and variable flow systems is that when you switch from 3- or 4-port valves to 2-port valves there has to be some form of differential-pressure control that limits the pressure against which the 2-port valve can close. This is essential if the valve is to achieve proper authority and, hence, control, but it may also be essential if the valve is to be able to close at all without generating noise.
From the designs I see, differential-pressure control is seldom properly assessed. Some designers adopt a rule-of-thumb approach, such as a general rule to locate differential-pressure-control valves (DPCVs) on each branch off the riser. This is not only a lazy solution but is invariably wrong since there is no logic to why the optimal differential-pressure control point should be at the riser.
Even worse is to see multiple levels of differential-pressure control and duplicate regulating valves alongside those DPCVs. It should be fairly obvious that in any circuit (a circuit being between the pump and any of the terminals) there should only be one differential-pressure controller. This can take the form of a DPCV or, to make life even simpler, a pressure-independent control valve (PICV) at the terminal. DPCVs located in the upstream branches of circuits feeding to terminals with additional DPCVs or PICVs have no function whatsoever and incur significant cost and energy wastage throughout the life of the system. Furthermore, a double regulating valve (DRV) in the same circuit as a DPCV or PICV is also pointless since both DPCVs and PICVs enable the flow to be regulated.
![]() |
Valves for variable-flow systems — a DPCV from Hattersley (below) and a Frese Optima PICV with 2-port modulating control |
![]() |
Faced with these strange offerings from designers, commissioning specialists are sometimes hesitant to criticise or simply confused themselves. How do you set a DPCV that has no function? Often some attempt is made to throttle the valve to get it into its operating range, but this just creates an unnecessary resistance and wastes even more energy.
In some cases it becomes evident that most commissioning specialists are used to setting flow rates but are not so familiar with the concept of setting a pressure differential. This misunderstanding is most evident when dealing with future-use by-passes. These are simple by-passes that are designed to accommodate circuits that don’t exist yet. Designers often think that these branches should have some form of differential-pressure control so that when the circuit is connected, it will always have enough pressure and/or flow. For the reasons stated above, this is usually the wrong decision and results in an unnecessary or poorly located DPCV or PICV.
To simulate the future resistance, the designer then helpfully adds a DRV to the by-pass alongside the DPCV or PICV. The challenge for the commissioning specialist is how to set the DPCV or PICV in such circumstances.
If a DPCV has been installed, the temptation is to leave the DPCV fully open whilst throttling the DRV to achieve the design flow rate. But having done this there is no room left to regulate the DPCV to get it into its operating range (part of the circuit resistance has to be generated by the DPCV). However, if they do it the other way round, by regulating the DPCV to achieve the design flow rate, they will find that it is impossible to achieve the required pressure differential because the fully open DRV has insufficient resistance.
The two valves need to be regulated in partnership. Most DPCVs come with manufacturers’ instructions that tell you the dial setting equivalent to a certain kPa differential-pressure setting — so, the valve can be adjusted to this setting as the first step. However, the valve won’t control to this setting until it sees a resistance across the DRV. Assuming sufficient pump pressure, this can be achieved by closing the DRV until the design differential pressure to be controlled by the DPCV is achieved. This is the correct approach.
In cases where a PICV has been installed in a future-use by-pass with a DRV alongside it, the situation is much simpler. Because the PICV enables flow regulation, the DRV has no function and should be left fully open. Then, to ensure that the future use by-pass has sufficient pressure differential, the pump-speed controller should be set at the BMS to ensure that the required index pressure differential is maintained.
I suspect the issues described in this article are fairly commonplace. Design reviews and commissioning-method statements prepared by a suitable specialist can often pay for themselves from the resulting time and cost savings achievable.