Prioritising maintenance
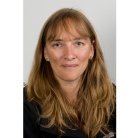
With BSRIA recently having updated its guidance to business-focused maintenance, Jo Harris gives an insight into where the concept is now, 12 years on from the original guidance, and how it can be used to prioritise maintenance requirements.
Maintaining the built environment and its building-services assets is an important part of ensuring they last for their designed life and continue to provide the service for which they are employed. Increasingly, organisations place greater expectations on the reliability of building services to support their operations and that in turn increases the requirement for maintenance regimes to improve.
Unfortunately the budget for maintenance doesn’t always increase in line with this expectation. Our industry suffers from maintenance contracts with service-level agreements (SLAs) that drive the wrong behaviours. An example is promoting time-based maintenance no matter what service the asset provides, and this can result in inefficient use of resources and higher-than-necessary maintenance costs.
BSRIA’s guide to ‘Business focused maintenance’* (BFM) provides the built environment industry with a methodology for utilising maintenance budgets more effectively. Assets critical to the business are maintained as normal, but other less-critical assets are managed as well as possible within the available budget.
Utilising this BFM methodology, organisations can direct resources based on the risk of failure and the consequence to the business of that failure.
There are many instances where BFM is being carried out informally by maintenance staff. If an engineer is assigned a planned-maintenance task for a pump that was visited three months ago and knows it has only run for five hours in that time, the likelihood of them undertaking anything more than a visual assessment is slim. This is a system that works satisfactorily —unless the asset in question provides a critical function to the business, in which case the decision not to perform that maintenance task becomes a business risk. There is another side to this; while the engineer is informally following BFM principles, the maintenance management system still allocates a time to the task, and resource planning is inaccurate.
To calculate the BFM risk score using the methodology explained in the guide enables the type and frequency of the maintenance tasks for each asset to be modified. There are four areas to assess.
• Consequence of failure.
• Functional resilience.
• Condition.
• Likelihood of failure.
The BFM risk score results in a number between one and 100, making it easy to explain to others within the business. Explaining that the business has an asset that has a 90% chance of failure rather than a 10% chance can ensure resources are allocated appropriately.
Maintenance professionals must explain to both the engineering staff and business managers that maintenance tasks and schedules are not written ‘on tablets of stone’. They need to be updated and modified to take account of the diversity of plant and their operational circumstances. Generic maintenance can result in plant reliability that doesn’t take into consideration the service levels required by the business or the safety, environmental and operational issues specific to a particular facility.
The benefits of BFM include the following.
• Encouraging proactive maintenance and management of facilities.
• Improving the identification of opportunities and threats in maintenance management.
• Providing a reliable basis for decision making.
• Maximising resources.
• Minimising losses.
The methodology is intended for use by those who establish or implement maintenance policies or strategies, but is also relevant to those who procure the services of maintenance contractors.
The term ‘failure’ is used in the methodology to mean the inability of an asset or a system to fulfil its function or meet its expected performance, such as cooling an office area. This BSRIA guide provides a step-by-step approach to determining this risk and can be purchased from the BSRIA bookshop.
BFM is not the sort of process that should be completed once and then forgotten. Assets that have had their maintenance regime changed should be monitored for any increase in failures. The successful introduction of a plant-room tour that ensures early signs of failure can be picked up on assets that have been identified as not requiring preventative maintenance will allow a proactive approach to maintenance. Implementation of condition monitoring through the BMS (building management system) is also possible to allow early warning signs to be picked up before failures occur.
Reactive calls should also be captured and allocated to an asset that has caused the problem. This data should be reviewed to provide an understanding of the following questions.
• What is failing?

• What are the consequences to the business?
• Why is it failing?
• Can it be prevented?
The condition of assets should be regularly updated, and this can be completed by maintenance teams during their regular activities rather than wait five years for a full condition survey.
Condition monitoring is widely used in the process industry, and has been for many years, but there has been a slow migration of these techniques into building-services maintenance. Condition monitoring provides a means of improving the conventional maintenance regime by evaluating indicative parameters of plant condition such as temperature, vibration, oil condition and power quality. This is known as condition-based maintenance (CBM).
Condition monitoring can also enhance fault detection in many assets, thus potentially reducing failure rates. In addition, potential benefits are gained by providing a greater understanding of plant performance, reduced labour time and repair budgets. It can also improve the energy efficiency of many assets. The most common condition-monitoring methods are really no more than highly sensitive versions of human senses — hearing, sight, touch and smell.
The methods available to the maintenance engineer fall into six primary classifications.
• Dynamic effects (vibration, pulses and acoustics).
• Particle effects (particle monitoring, change in size and/or shape).
• Chemical effects (change in chemical emission).
• Physical effects (changes in physical appearance or structure, cracks, warping etc.).
• Temperature effects (increased operating temperature wear, friction etc.).
• Electrical effects (changes in resistance, conductivity, dielectric strength and potential)
Understanding the strengths and weaknesses of these methods is critical if the correct condition-monitoring system is to be applied. Almost all building-services maintenance engineers rely on their senses to monitor the condition of plant. Understanding how a particular asset operates is critical for preventive maintenance. The noises, vibrations and heat given off while plant is running give an experienced maintenance engineer a good indication of plant condition.
Statutory testing and inspections are applied to asset scoring of between 10 and 40 on the scale of one to 100. No assets that are subject to statutory inspection or are mandatory for that sector (such as locks in prisons or playground equipment in schools) should score less than 10, as the business consequence will always be high, and failure to comply with the regulations will result in the responsible person being investigated.
If an asset scores between 11 and 40 then a standard (good) level of maintenance would be suggested. The assets in this range are not necessarily putting the business at risk but they should be maintained to ensure the risk doesn’t increase.
An asset with a score of 41 to 100 requires a high level of maintenance. The maintenance task specified must address the most likely failure modes expected from that type of asset. It is with these high-risk assets that a review is conducted to determine if there is an option of designing out the risk, planning a business continuity measure or updating the maintenance task to address the most likely failure modes.
To support this assessment, a set of typical failure modes, consequences and preventive actions for a range of building services assets are provided in the BSRIA guide. For each asset or part of an asset (a component), a list of failure modes is provided — with the most likely cause, what the consequence of that failure mode will be on that component and what needs to be carried out during maintenance to prevent that failure mode.
Of course regular dialogue with the core business will be required to understand any future changes in business needs that will impact of the maintenance regime.
Jo Harris is head of sustainable construction at BSRIA.
* BG 53/2016 ‘Business-focused maintenance’ 2nd edition is available from the BSRIA bookshop.