Business focused maintenance – the what, where and how
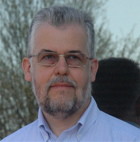
Colin Pearson shares his insights into an alternative to the traditional planned preventative maintenance method, and why it offers a way to think about maintenance planning that best suits each building, business and client.
What is maintenance for? To keep equipment in good condition? To make it last longer? To prevent it failing? No, it is to support the business. When maintenance is seen as business support it is part of the profit-making process, not an overhead cost.
BSRIA recently published an updated guide to Business Focused Maintenance (BFM) to show how plant maintenance should be used as a means of supporting a business function. With that in mind, maintenance schedules, supposedly developed to avoid equipment failure by always ensuring components were replaced before they failed, can be discarded and replaced by a more pragmatic approach. The planned preventive maintenance task frequencies can be modified or discarded if more sophisticated methods are used.
Analysis
BFM relies on system analysis and plant condition management to ensure that business function is maintained with the minimum of intrusive maintenance, recognising that:
• Plant failures often happen just after intrusive work (maintenance-induced failures).
• Maintenance task frequencies were set for generic plant in constant use (which may not be the case in every building).
• Keeping plant working may not be necessary if you have a system with redundancy (spare capacity).
• The likelihood of failure rarely depends on the age of components.
The building services industry has a standard specification of maintenance that has been updated over the years: SFG20. Many organisations use this to enable them to tender for outsourced maintenance on a like-for-like basis but the use of this to deliver maintenance can lead to generic maintenance being delivered across the business.
Take pump maintenance. This is defined in SFG20 as a three-monthly task, but if the pump is one of three that can each support the needs of the business function, there may be no need to routinely dismantle it and inspect the impellor. If it fails, the alternate pumps can still support the business function. That would be the best time to dismantle it and inspect the impellor. One needs to consider load factor, criticality, manufacturing quality and many other factors.
Business needs
BFM recognises that the need for maintenance generally arises from business needs, such as:
• Complying with legislation.
• Minimising health and safety risks.
• Managing business risks.
• Responding to business and customer requirements.
• Adding value as part of the business process.
• Reducing overall business costs.
• Minimising whole life cost.
• Increasing asset/system availability.
• Increasing operational uptime.
• Managing business continuity.
Users of the BFM guide, first published by BSRIA in 2004, have demonstrated increased system availability and reduced costs. Adopting BFM requires a process of:
• Functional analysis.
• Criticality assessment.
• Business continuity planning.
• Condition survey.
• Assessing likelihood of failure.
• Assessing consequences of failure.
• Maintenance strategy review.
• Maintenance task review.
• Continual monitoring of performance.
Failures
Many maintenance tasks can be eliminated, adopting a ‘run to failure’ approach or replaced by condition monitoring (CM) which leads to condition based maintenance (CBM). If CM is used further analysis must be applied to find the likely modes of failure and the most suitable parameters to monitor so that early signs of failure can be detected. Common CM methods include:
• Thermal imaging.
• Vibration monitoring.
• Acoustic emission monitoring.
• Lubricant analysis.
• Plant performance monitoring.
Many of the common failure mechanisms in building services plant generate heat, such as increased friction in failing bearings or drive belts. These can be quickly and easily detected with thermal imaging. Advances in the technology of infrared cameras in the last two years have made them more affordable and easier to use. The simplest infrared cameras now weigh less than 50g, cost under £200 and attach to smartphones for easy use and sending images to the plant manager. The thermal image may not show why heat is being generated, but it will clearly show where so that other methods can be used to diagnose the problem.
Diagnosis
Vibration or acoustic emission analysis can be used to diagnose a range of problems in bearings including wear, damaged rolling elements, pitting, shaft unbalance or misalignment. All the condition monitoring techniques can detect faults long before they develop into failures so appropriate remedial action can be planned and scheduled for minimum disruption.
Cost-effective
Regular use of these methods at appropriate intervals can be more cost-effective than maintenance based on generic schedules for critical plant. But for non-critical plant the most cost-effective maintenance may be ‘run to failure’. By applying the BFM methodology you can be confident that you have selected the most appropriate maintenance for your building services plant.
The BSRIA Business Focused Maintenance Guide – BG 53/2016 provides the background information, methodology as well as guidance on component failure modes and preventative actions and a detailed case study of BFM applied to a real building.
Colin Pearson is head of Building Performance Sustainable Construction Group, BSRIA. Books and guides from BSRIA can be purchased through the website: link below.