Stepping up the performance of radiant heating technology
Glyn Turner, new-product development manager with Ambi-Rad, with the burner specially developed for the company’s new range of U-tube radiant heaters. It produces a long flame to achieve a more even distribution of heat along the radiant tube.
One effect of the Energy Technology List and Enhanced Capital Allowances has been to impose higher standards of efficiency for radiant heating — a challenge that Ambi-Rad has responded to.Radiant heating has long been applied as an effective and energy-efficient method of heating large spaces. Compared with, say, warm-air heating in large, high spaces with high ventilation losses and large doors that open frequently, radiant heating delivers comfort more quickly and with lower fuel consumption. The effectiveness of radiant heating is not just due to the efficiency with which it burns fuel but also to the fact that it heats people and objects directly rather than enveloping them in warm air. Indeed, since people are more sensitive to radiant heat than to air temperature, they are comfortable with a lower air temperature if the source of heat is principally radiant. Glyn Turner, new-product development manager with Ambi-Rad, tells us that when radiant heating first appeared on the Energy Technology List in August 2002, so that it qualified for Enhanced Capital Allowances the radiant efficiency required was 52.5%,, with a combustion efficiency of 82%, net.
Out of range About two years ago, the ECA requirements were increased to a radiant efficiency of 60% and a combustion efficiency greater than 86%, net. Glyn Turner explains that such performance levels were out of range of the products that existed at the time, so that although radiant heating remained an effective approach to space heating, it could not qualify for Enhanced Capital Allowances. To meet these new requirements, Ambi-Rad embarked on a programme of research and development aimed at delivering a step change in the performance of radiant-tube heaters. Glyn Turner explains that the programme covered the three key elements of radiant-tube heaters. • Burner • Radiant tube • Reflector In addition the project looked to further increase the efficiency of production by using different materials and standardising on components across a wide range of heater sizes. These U-tube heaters will become available in the summer in time for the next heating season and provide outputs from 15 to 50 kW. They deliver a thermal efficiency around 90%, which is well above the requirement for Enhanced Capital Allowances. Combustion efficiency has been improved with the development of a new burner. The key to increasing combustion efficiency is to preheat combustion air. This is achieved using a heat exchanger at the end of the U-tube but adjacent to the burner (see photo). Air is drawn in from the space, heated by the exhaust gases before they are flued and then supplied to the burner. Preheating combustion air also reduces NOx emissions — from 120 ppm to less than 70 ppm.
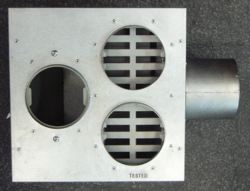
This heat-exchange module improves the combustion efficiency of Ambi-Rad’s new radiant heaters by transferring heat from the flue gases to incoming combustion air. The flue gases enter this module through the stub on the right and leave on the left. Combustion air enters and exits through the other two ports.
Glyn Turner says that the temperature of the flue gases is reduced by about 100 K, so that they are flued at about 150 to 250°C). The new burner has a much longer flame, which provides a more even distribution of temperature along the radiant tube. The tube is much cooler near the burner, which has important implications on the material used. By reducing the operating temperature of the tube to 700°C, Ambi-Rad has broken away from the need to use stainless steel. Instead, an aluminised-steel tube is heat treated at 700°C to give it a dull-grey finish which radiates heat more quickly than shiny stainless steel and improves the emissivity of the heater. The third element of development has been to enhance the reflector that directs radiant heat from the tube downwards. Glyn Turner explains that the key improvement has been to increase the depth of the reflector skirt to below the level of the radiant tubes to reduce convection losses and increase radiant efficiency. Rather than apply insulation to the reflector to reduce upward heat loss, the new design is covered by a canopy, with an air gap to obviate the need for thermal insulation. Since the geometry of the reflector and its distance from the tubes affects their temperature, a programme of testing was undertaken to optimise performance while avoiding the tubes getting so hot that more expensive materials would be needed.
Two ideals In developing this new range of radiant heaters, Ambi-Rad has achieved the two ideals of a better-performing product and improved customer service through product standardisation and component rationalisation.
Related links:
Related articles: