The filter factor

After a 10- year break, 50 year old Mark Bamforth returns to the air filtration industry and casts a critical eye over what has changed, and more significantly what hasn’t.
I’ve been amazed, and pleased, to find many of the same old faces — be it all a little older and greyer like me — amongst both customers and suppliers. Essentially much of the technology has remained the same, both in principle and in terms of the manufactured products, so I’ve had very little catching up to do to get back up to speed. Where the change has come is from external factors which have a conflicting bearing on the industry.
Belts are being tightened, with companies looking for ways to cut corners and save money whilst at the same time increased environmental responsibility and standards authorities press for clean air quality to be maintained and improved.
Filters are often the underestimated part of an air-handing system. They need to be replaced regularly and, where companies run central plant air-conditioning, are not generally designed to be repaired or cleaned. Optimised filter changes are key to ensuring that the air-handling system works efficiently. While a single new filter may cost less than £5 itself, it can have a great impact in determining the functionality of the system as a whole, which will have a cost thousands of pounds.
Replacing filters at the correct time intervals translates to a real cost effect for any business, and there is a temptation to reduce the frequency order to make a cost saving.
Inevitably however, not replacing filters leads to deterioration in the system’s efficiency and far more costly cleaning and replacement of expensive key parts. Ultimately it’s a necessary evil for every maintenance department, and it’s the job of companies like us at D&E Services to help customers to find the right balance between cost and quality.
Buying filters on price alone can be a false economy as with any product. The on-going filter replacement cost needs to be balanced against the quality and ability of the filter to do the job for which it is designed.
The lowest cost filters, generally media pads or panels, are designed to remove the great mass of large particles present in the air, acting as prefilter to more costly filters further down the system, protecting more expensive parts such as fans, coils, humidifiers and keeping supply ducts clean. A well-made, well fitted and regularly monitored panel-filter section can give an overall saving on plant maintenance far in excess of its basic cost, increasing energy efficiency and reducing cleaning costs.
For any building — retail, catering, offices or manufacturing — the wrong choice of filters or a lack of professional expertise in fitting them will impact on the whole air-conditioning system. At D&E when we first visit new customers we often find dirty ducts and staining on grilles, which can be indicators of a history of badly fitted filters or the wrong regime of filter changing. Such issues can be resolved by ensuring that filters are fit for purpose, installed properly and changed in accordance with the manufacturer’s specifications. Cost savings follow automatically.
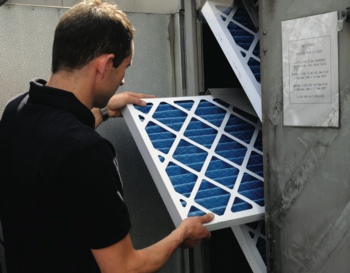
The means and method of filtering air, the media and technology used, has by and large remained static over the last decade. Pleated synthetic mats, spun glass fibres or glass paper, card-framed panels and bag filters are still the basic building blocks of the air filtration market.
The technological focus now is on how to use these basics in the best way to offer the user a long-term benefit over the lifecycle of the building. More filter media means more cost, but it also means a lower pressure drop and higher dust holding, which in turn leads to a longer filter service life and fewer changes — plus possible savings in overall energy costs. As business owners are increasingly pressured to lower their carbon footprint and improve their environmental profile this becomes a motivating factor in the buyer, affecting the filtration industry’s outlook with more focus on saving energy.
Rigid mid-range filters using pleated glass paper can cost twice as much as an equivalent conventional pocket bag filters, yet they offer savings in energy and change costs. Their shorter length can also offer savings to AHU manufacturers in terms of metalwork costs.
The focus in recent years on indoor air quality endorses the importance of efficient and well maintained air-filtration systems, whether for the benefit of staff in an office, clinically sanitised conditions in hospitals or for specialist industrial processes. When sick building syndrome became an issue the final filter grade stipulated for offices rose to finer grades F7 or F8, compared to F5 or lower. More significantly, the role of filters in air-conditioning units gained in importance.
As filter standards have been changed and refined over the years to more accurately reflect more stringent real life demands, it appears there are still many competing authorities such as EN, ASHRAE, ISO, UL with many maintenance department staff confused and not up to speed on the optimum filter specifications for their building. Thankfully for me, returning to the job late in 2011, they still need a specialist to advise on the right filter for the right job!
Mark Bamforth is sales manager with D&E Filtration Services