Flushing your way to system success
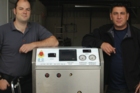
Mike Creamer of Business Edge explains why flushing and cleaning air conditioning systems of contaminants can prevent parts failing and save thousands of pounds
When the refrigeration circuit of an air-conditioning or refrigeration system is corrupted with water or acid it often spells death for the entire system. This is especially true of liquid-water entry as a result of evaporator fractures on water chillers, but is very often true of acid attacks on motor windings.
Water that has entered a system can often take months to be removed by the lengthy process of evacuation and dehydration. The vacuum pumps used often suffer as a result, and the repair manpower involved is also expensive.
When acid formation attacks the windings of semi-hermetic and hermetic compressors, engineers often attempt to clean the system using nitrogen or oil dilution. Replacing a compressor motor to solve the problem can fail too, with acid attack continuing as the oil in the system retains the acid.
Using a flushing and cleaning system specially designed for air-conditioning or refrigeration equipment is often the most cost-effective alternative. In many cases, flushing and cleaning can eliminate the need to dismantle, destroy and replace critical components. In some severe cases it avoids the need for complete replacement of the system.
This technology is perfect for refrigerant retrofits where, for example, R22 and its associated mineral oil must be completely removed from the system in readiness for a drop-in replacement refrigerant and new synthetic oil.
In most systems, removing refrigerant is easy but removing all the oil is almost impossible. Again, a flushing and cleaning system is capable of cleaning the system entirely — removing all traces of oil, liquid water, acids and particulate matter. If a motor has burned out, the gradual degradation of the motor windings often results in a considerable amount of debris being distributed around the system, which can block expansion valves. A flushing system will remove all debris.
How does flushing and cleaning work?
First, a high-quality flushing and cleaning system like the Fri3Oil deep-cleaning system recovers liquid refrigerant at a rapid rate — up to 1.3 kg/min.
![]() |
The Business Edge flushing team get on with the job of cleaning a system. |
As the refrigerant goes to the recovery cylinders, the flushing machine cleanses it to an extremely high degree of 600 parts per million (150 ppm in the case of HFC refrigerants). The cleansing process sends the contaminants into separate cylinders.
The reprocessed and recycled refrigerant is then ready for use as the flushing medium. The flushing system applies the refrigerant in liquid form in a cyclic manner to the refrigeration system, repeatedly raising and lowering the liquid level in order to float off contaminants from all system pipework and vessels.
The process is fully automated and micro-processor controlled, but the presence of a refrigeration engineer is essential for good practice, safety and legal reasons.
It is often necessary to use some virgin refrigerant of the same type since more refrigerant is needed for flushing than the normal running charge of the system.
When flushing and cleansing is complete, this being visible on the flushing machine, the entire refrigerant charge is then rapidly recovered and again recycled to an absolutely clean condition in readiness for re-use by the system.
The recovered residue in the form of water, oil, acid and particulate matter can then be easily disposed of via REA cylinders without any destruction charge.
This technology avoids the need for the user or contracting company to pay a destruction charge of several pounds per kg, while also having to pay for new refrigerant. These two major cost savings, coupled with the re-use of all system components, providing they are in working order, can represent substantial savings on the cost of maintaining air-conditioning and refrigeration installations.
The technology works well on systems with extraordinarily long refrigerant pipe runs — discharge lines, liquid lines and suction lines — and also thrives on dealing with systems with long vertical pipe sections.
The Fri3Oil deep-cleaning system will completely flush compressor crankcases, suction accumulators, oil separators and liquid receivers. On large systems, the cleansing process is more effective if the system is sectioned — with the flushing tackling one area at a time.
Over the past year, Business Edge engineers have saved customers tens of thousand of pounds by flushing and cleaning rather than replacing parts on systems.
Mike Creamer is with Business Edge, from which this system is available for buying or hiring. The company runs training courses on how to use the machines and will also make available its own engineers for projects.