BIM and BEMS — bringing in the human factor
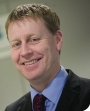
Ian Ellis of the Building Controls Industry Association says that while new technologies are leading the way to more efficient building design and construction, good communication is still the key to specifying and designing controls for long term energy efficiency.
The drive to integration in the design and construction of buildings has never been greater. Sir Michael Latham spent years exhorting the industry to adopt more co-operative working practices, but it looks as though technology may now be enabling greater teamworking among architects, engineers, contractors and the rest.
Over the past two years, the use of Building Information Modelling (BIM) has doubled on UK construction projects. Government is driving its use, with a view to increasing the industry's productivity and profitability. Construction represents around 7% of the UK's GDP, so a lift for construction gives the economy a nice boost too.
It is easy to see why BIM seems to have the answers for the construction industry's challenges of poor co-operation, repeat works, unpredictable costs and other issues. BIM brings together shared information in a digital format so that those involved in a construction project have access to the same data. The client and end user can also use BIM to support whole-life asset management, making BIM a design-to-operation tool that improves productivity, risk management and sustainability.
In the controls industry, integration has always been a key issue —although from a slightly different point of view. The nature of controls design and installation is to knit together the elements of the building's heating, ventilation, lighting and, potentially, many other technologies. The aim is to create an holistic, integrated system that functions effectively and in an energy-efficient way.
The Building Controls Industry Association considers that an holistic view of how HVAC systems work is crucial for controls engineers; our building controls technical training courses cover this area in great detail. BIM is therefore to be welcomed — encouraging, as it does, a single view of the building, rather than slices and sections. But the technology can only go so far. Seeing the building services on a model is very different to making them work in a well controlled system.
One of the main benefits of BIM that is often cited is that a digital model of the building design means that clients know exactly what they are going to get. In many ways that is true. A 3D model shows clients what the outcome of the project will be. Engineers and contractors can also see how their components fit within the space provided.
However, predictions of long-term building performance are more realistic if they take into account the importance of the proper application and use of building controls and building energy management systems (BEMS). No matter how efficient the boilers, fans or lighting, a building it will not be energy efficient if it is not controlled to ensure energy efficiency. Without input from clients and a clear understand of what the objectives are, a BEMS will not provide the maximum benefits in terms of energy savings and smooth long-term building operation.
The human factor and ensuring that controls are correctly procured and commissioned, will still be the important elements of an efficient building. This means communication of requirements from the start of the project, early involvement of the experts and good handover so that the building managers know how the BEMS works.
Interestingly, the Government's own BIM website (www.bimtaskgroup.org) says that the technology isn't really the point: ‘Other than a digital tool set, you don't actually use BIM; it is a way of working; it's what you do: information modelling and information management in a team environment.’
Ian Ellis is president of the Building Controls Industry Association.
Specifying a BEMS — a quick checklist
The three main types of specification for controls are standard guide specification, performance specification and propriety specification. Standard specifications are widely available and generic.
Performance specifications are determined by the particular requirements of the client. Proprietary specifications are more exacting as they allow for the selection of particular building controls products. The choice of specification method will depend on requirements and budgets.
Draw up a checklist for the following:
• What is being controlled.
• What is being monitored.
• What are our energy-saving measures? It is important that these are a high priority on any specification.
• What is just being enabled.
• Who is providing the wiring and connections between equipment and controllers.
• Who is providing the equipment and controllers, valves, dampers, actuators and sensors.
• Who is providing the programming.
• What are the key performance indicators
Don’ts
Don’t use or accept the phrase ‘the system shall be capable of’. Instead state that the strategy will be programmed, set up, tested, and fully functional.