The benefits of challenges of a larger ∆T in hydronic systems
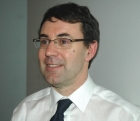
So great are the benefits of a larger ∆T in hydronic heating and cooling systems that the issues posed to the commissioning process are well worth addressing. Chris Parsloe explains.
The current trend towards heating and cooling networks with low-carbon heating or cooling sources is a consequence of the drive towards reducing carbon emissions from building-services systems. To operate efficiently, the design of these systems must establish and maintain a large ∆T (difference between primary flow and return temperatures) as the main priority.
Furthermore, the commissioning of these systems has to involve checking to ensure that this ∆T is maintained under all operating conditions. This is equally if not more important than simply checking to ensure that the design flow rates are being achieved.
Based on my experience trouble-shooting heating and cooling pipework systems in the UK, I can confidently say that every system design that crosses my desk fails to appreciate the relevance of ∆T. Some heating designs are still 80/70°C, whilst more are moving to 80/60°C. However, in all cases it is obvious that designers view the ∆T as a notional value not to be taken too seriously. They might size the terminal unit using the selected ∆T, but when installed in a real system, the return temperature could vary for all sorts of reasons.
For example, if a large ∆T leads to a very low design flow rate that is below the range of commercially available orifice-type flow-measurement devices, then some engineers will increase the flow rate to a value that can be measured. This, of course immediately kills the ∆T. The result is an over-sized terminal unit with a small ∆T.
Alternatively, the designer might decide that to provide a path for flow under low-load conditions they will add bypasses containing pressure-relief valves that open when the pressure increases. This approach ensures that the pump can’t drop its pressure significantly, thereby wasting pump energy but also permitting a large slug of uncontrolled by-pass water to mix with return water, which again kills the ∆T.
Missing out on the benefits of good ∆T control causes all sorts of operating problems in systems, as well as incurring major installed cost and energy wastage.
For a start, the larger the system ∆T, the smaller the flow rate, the smaller the pipes and the smaller the pump energy. Doubling the ∆T halves the flow rate, so the potential savings in installed costs are significant. The additional cost incurred in slightly bigger terminals is tiny in comparison. Furthermore, losses from heating pipework and heat gains to chilled-water pipes are greatly reduced by widening the ∆T.
The sizing of thermal stores or buffer vessels is made easier with a larger ∆T, and these vessels can be a lot smaller if there is a larger ∆T.
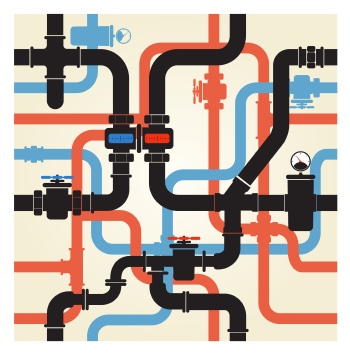
Simply ask yourself what size of thermal store is required to provide 100 kW for an hour with a ∆T of 20 K compared to 40 K; it is straightforward that for 20 K ∆T you need double the volume of storage for the smaller ∆T.
However, what if you are asked to make this type of assessment when, for one of the reasons above, you have no idea what the return temperature could be in practice. In this case the thermal store is impossible to size.
If a system is designed so that the desired return temperature is achieved under all operating conditions, then the thermal store is easy to size; with a large ∆T its volume can be minimised. It even becomes possible to sequence boiler/chillers on and off using temperature stratification in the store. As the moving thermocline moves up and down in the store, sensors located in the vessel sense the movement and switch additional boilers/chillers on and off as required. This is far simpler and cheaper than trying to assess energy consumptions of the various circuits using heat meters.
The commissioning of the system is critical to making these systems work. Instead of simply following the advice to measure and confirm design flow rates (the main focus of CIBSE Codes and BSRIA guides) the additional aim should be to check ∆T values. This should ensure that under peak- and minimum-load operating conditions, the temperature of the water returning to the central plant is maintained to maximise the ∆T — and certainly not less than the designer’s intended value.
This involves checking the main flow and return temperatures and, if necessary, investigating why the ∆T is not being achieved. This could involve searching for unanticipated bypasses or checking control functions to ensure they are reducing flows as intended.
This requires a different type of commissioning process that goes beyond what is advised in existing guides. Furthermore, commissioning specialists may not have the necessary skills to investigate these issues. Inevitably, input will be required from designers and installers. However, the performance, cost and energy benefits are too great to keep on ignoring.
Chris Parsloe is director of Parsloe Consulting.