Delivering energy- efficient heating
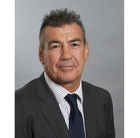
An energy-efficient heating system should be at the top of the agenda for any building-services professional. However, improving the efficiency of a heating system is about more than just installing a high-efficiency boiler, as Steven Evans of Potterton Commercial, explains.
Cutting back on energy use and carbon emissions should be an important priority for any business. With the non-domestic sector contributing to 18% of the UK’s total carbon emissions, this market has a major part to play if the country is to reach its carbon reduction targets(See 2nd link below).
In an effort to encourage businesses to take their carbon-cutting commitments seriously, the Government has introduced a number of initiatives that will help organisations implement energy-saving upgrades and encourage the installation of more efficient products.
One of these is the Energy Savings Opportunity Scheme (ESOS), which is a mandatory requirement for large undertakings, helping them identify opportunities to make energy and cost savings. According to a sample of the assessments, the cost reduction achievable through the implementation of energy saving measures identified by ESOS audits could be much higher than first predicted, at nearly 25% (See 3rd link below).
And while ESOS is not a requirement for smaller businesses, the heightened focus on climate change and energy policy is likely to still filter across the wider commercial sector.
There has been no better time to consider ways to review energy consumption — and with a large proportion of energy use resulting from the heating system of a building, it makes sense to make this a priority.
Recent advances in the heating sector mean that it is now easier for building managers to select the most effective solution. Product efficiencies have become more visible and easily understood thanks to the Ecodesign and Energy Labelling Directive, commonly referred to as ErP, which was introduced in September 2015.
While the legislation covers a number of points, two of the main changes are that energy labels are required for boilers up to 70 kW, and manufacturers have to offer extra information on their websites, helping to compare products in the same energy banding.
When it comes to replacement, taking the opportunity to install a condensing boiler and updating system controls could save a substantial amount on existing energy costs.
Heating appliances offer the most potential for reducing cost and energy consumption when they are closely matched to the demand of the building in question. By considering how and when a building is used in the early stages of the project, building managers and contractors can ensure that the heating system has been correctly sized to the predicted demand of the building and can deliver to its performance capabilities.
However, there is more to cutting emissions and energy costs than just selecting an efficient and correctly sized boiler. It’s important to look at the bigger picture, taking into account how the system is operated and maintained to ensure it continues to run at optimum performance.
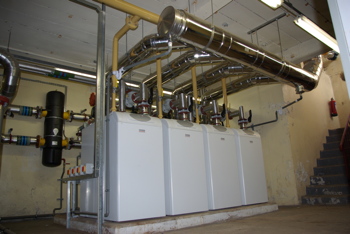
Many commercial building managers will expect a system that is flexible enough to respond swiftly, accurately and efficiently to changes in heating and hot-water demand, making the specification of correct controls essential.
Zone controls are ideal for commercial applications as they can be programmed to allow for the fact that different areas within a building don’t always need to be heated in the same way. Some newer commercial boilers also come fitted with weather-compensation controls as standard — enabling the boiler to react according to the outdoor temperature.
A scheduled maintenance and service regime must also be implemented from the installation stage of any heating system to safeguard long-term energy efficiency and performance. An important element of this is chemical water treatment, as heating-system efficiency and longevity can be severely reduced with un-treated water.
This is because water contains dissolved atmospheric gases and minerals that can affect a heating system’s components. Failing to invest in appropriate water treatment can result in corrosion and the build-up of lime scale, leading to inefficiencies, poor performance and potential boiler failure after a relatively short period of time.
Systems that are corroded become blocked with sludge and debris, which will cause the boiler to work harder and for longer, as the circulating water is unable to transfer the heat efficiently throughout the system. This drastically reduces energy efficiency, in turn increasing running costs as well as carbon emissions.
Although an efficient boiler should be at the heart of a heating system, energy efficiency is achieved by implementing a combination of key factors. These include correct installation from a suitably qualified tradesperson, weather compensation and adequate chemical water treatment – which can not only help save energy, but also extend the life of a boiler and improve reliability.
Anyone looking to change a boiler to improve the efficiency of a heating system should also consider other key variables to ensure key performance is maintained alongside important cost and energy savings for the end user.
Steven Evans is national sales manager at Potterton Commercial.