Cut the NOx
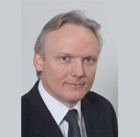
One of the options for achieving low NOx emissions is to use premix burner technology. Bernard Dawson explains how this differs from traditional pressure jet burner technology.
With a growing demand to reduce NOx emissions from combustion equipment it’s important for building services engineers to be aware of the options available. Pressure jet burners using flue gas recirculation (FGR) are a popular option but there are occasions where premix burner technology offers an alternative.
In traditional pressure jet burners, the gas and the combustion air are mixed at the point of ignition on the end of the combustion head in the space available in the combustion chamber (diffusive flame). This is the most familiar arrangement.
In premix burners the air-fuel mixture is created upstream of the combustion head – which comprises a metallic cylinder that has multiple gas ports on its surface and is covered with a woven wire gauze (known as a ‘sock’). The air-fuel mixture flows inside the combustion head, through precision-located ports and sock to the external side of combustion head where ignition occurs through spark generation to an electrode and the flame is established.
Geometry for efficiency
This means that the flame develops only on the external surface of the combustion head, with combustion taking place very close to the metallic fibre of the blast tube.
![]() |
Premix burners support high turndown ratios; good for varying heat loads |
The geometry of the gas ports has been designed to ensure that throughout the modulation range the speed of the air/gas mixture is sufficient to avoid burn-back. Premix technology also offers a much lower risk of flame impingement, due to the reduced likelihood of contact of the flame with the combustion chamber walls.
Also, the high combustion intensity developed on the premix burner head means that a greater heat output is achieved over a much smaller combustion head dimension, when compared to other burner technologies. This means that in certain applications combustion chamber dimensions can be greatly reduced, resulting in lower manufacturing costs.
A key factor here is the design of the combustion head, which can vary. The best design uses a seamless knitted wire for the ‘sock’ that allows its application around the support without any welded seams. Thus, critical situations to components caused from thermal stress, are eliminated. Moreover, this “sock” technology allows for an even distribution of the heat along the length of the combustion head, also providing precision of heat control.
Premix packaged burners, which are currently available in outputs from 5kW to 3MW, offer a number of benefits. These include low emission levels to ensure compliance with the most stringent of current and anticipated legislative requirements. Even on large burners up to 3MW, we have seen NOx emission of lower than 30 mg/kWh – and some independently witnessed site tests even down to less than 20 mg/kWh.
The exact NOx emissions will depend on a number of factors, but are consistently lower than current requirements. For instance, at Liverpool Metropolitan Cathedral, Riello RX premix packaged burners are achieving NOx levels of less than 40mg/kWh, more than half the 80mg/kWh threshold required by EN 676 for gas-fired burners to be classified as ‘low NOx’.
Premix burners also support high turndown ratios up to 8:1 on specific applications to ensure optimum performance at varying heat loads. This makes premix burners ideal for a host of applications from condensing boilers through to the process sector including spray booths and industrial ovens amongst others.
Another benefit is reduced noise levels - potentially 30% lower can be achieved compared to other forms of combustion technology. Variable speed drive motor technology can also be utilised to provide additional noise reductions and electrical cost savings at lower heat outputs. Advantages of a reduction in flame noise further reduce the noise levels experienced at the flue exhaust.
![]() |
Selecting the right burner for the job can save energy in the long term, and help reduce NOx emissions. |
Recirculate flue gas
In terms of control, premix burners can operate with a range of options, from progressive two-stage operation to fully modulating via 0-10V or 4-20 mA. Full electronic control is also available, which offers operational display and diagnostic features at a glance.
It’s worth elaborating on the use of flue gas recirculation to reduce NOx levels. Flue gas recirculation (FGR) is a proven method for reducing NOx levels but has not been widely used in the UK as it requires additional controls. However, with tighter NOx regulations it is a very effective way to meet stricter requirements and FGR burners are now available with outputs from 500kW to 32MW, to provide ultra-low NOx emissions as low as <40mg/kWh.
The principle of FGR is that a percentage of flue gases are piped back into the burner air supply system to reduce the flame temperature. The recirculated flue gases are relatively cool and inert, and with the inhibiting presence of CO2 they reduce peak flame temperatures.
FGR burners need to be used in conjunction with electronic cam control of the combustion air/fuel ratio via separate servomotors and a further separate servomotor to control the flow of the re-circulated flue gas. The use of FGR with electronic cam control delivers improvements in energy efficiency as well as reductions in NOx emissions.
There are a number of options for engineers, and the important point is to select for your project based on knowledge of the technology available today.
Bernard Dawson is technical director with Riello