Making tracks to the future
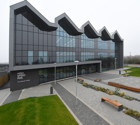
As the HS2 project takes shape, heating the rail sheds along the route is a significant challenge. Here Nick Winton explains why engineers need to get to grips with the knowledge of how to apply radiant heating for efficiency.
High Speed 2 (HS2) is one of the largest infrastructure projects that this country has ever seen – six times the budget of the 2012 Olympics. It will provide a new high-speed railway link between London, Birmingham, Manchester and Leeds, speeding up journeys, releasing space on crowded lines and bringing Britain closer together.
Around 25,000 people are needed to build the project, including 2,000 apprentices. To support them all with the right skills, Network Rail is providing two state-of-the art colleges in Birmingham and Doncaster to train the next generation of rail engineers. This includes understanding elements of building services for efficiency and performance.
The ways in which train care depots are utilised, often intermittently and at irregular time intervals, make the efficient use of energy extremely difficult. Therefore, consideration must be given to selecting a heating system that offers flexibility of operation at optimum efficiency.
Train maintenance sheds are invariably very long and narrow with large doors opening constantly at each end, thus notoriously difficult to heat and even more difficult to keep warm. The doors often occupy the full width of the building and may be left open for many hours a day, creating a wind tunnel effect where cold air at high velocity is drawn through the shed.
This means that air infiltration can severely disrupt comfort conditions within the interior. A heating system needs to be able to sustain a comfortable environment in these conditions and especially provide rapid recovery once the doors are closed. Air curtains over or to the side of the doors, either ambient or heated can mitigate the issue of air infiltration at the doors.
Maintenance is frequently carried out at night, compounding the inhospitable climatic conditions along with partial occupation. It is therefore important for efficient use of energy that the heating system can be easily and effectively zone controlled. What’s more, the mass of a train is considerable, and when a cold, wet train enters the shed it creates a cold sink. The heating system needs to be able to provide rapid response to changed conditions.
Radiant heating can be applied successfully in these challenging buildings. The primary source of radiant energy in the natural environment is the sun. Radiant heat warms all solid objects and surfaces in its path.
Reznor has exploited this concept in its energy efficient radiant heating systems. Radiant tube heaters, mounted overhead, produce infrared radiant heat that is directed downward by a reflector. The infra-red heat passes through the air without heating it and falls on people, floors and equipment below creating comfortable all-round radiant warmth at low level, without wastefully heating the whole volume of the building or the roof space.
Because radiant heat can be controlled directionally, only the occupied areas of the building need to be heated, which enables considerable energy savings to be realised.
The objective of a radiant heating system is to ensure that the people in the building are comfortably warm. By the correct application of a radiant heating system comfort levels can be optimised. Radiant heat warms objects and surfaces, increasing the mean radiant temperature and reducing the body’s loss of heat to its surroundings. In addition, by eliminating air movement, convective loss of heat from the body will also be reduced.
Steam Loco Sheds
Steam trains aren’t often used these days, but they are still in operation and need to be carefully and continuously maintained. Due to the nature of the locomotive, vast amounts of steam are released, captured by massive hoods and released to atmosphere. When designing a heating system account of these hoods in the roof space is critical.
1. The majority of work undertaken on these locos is at low level, ensuring heat is delivered between the tracks on the platform and in the pits is vital.
2. Radiant heat delivered via long lengths of radiant emitter is an ideal solution for heating the long distances between trains.
3. Some rail sheds are in excess of 300m in length, so the design of the heating system is paramount to ensure optimum zoning capabilities, both for client operational flexibility to minimise running costs and to ensure the capability of being able to rapidly respond to changed conditions.
Older sheds were notoriously poorly insulated structures with open doors at each end creating a massive wind tunnel. Radiant heat was the only realistic option as a heat source. Modern radiant systems continue to be the best choice, but with better delivery of warmth for occupants due to advances in technology.
Diesel Loco Sheds

Many of these sheds derive from the steam era and as a result some still lack good insulation values for the fabric. Diesel locos also have hoods to collect diesel fumes from the engines, but due to the general atmosphere within these sheds, the radiant heating system has to be designed to have ducted fresh air supply from outside to the gas burners. This ensures the filters within the burners are kept clean and not clogged from the diesel fumes. Points 1 to 3 regarding steam loco sheds apply here too.
Electric HS Loco Sheds (power via 3rd rail)
These sheds tend to be cleaner due to the lack of diesel fumes and do not require ducted air to the gas burners of a radiant heating system. The work on these trains is primarily at low level, so again the above points 1 to 3 are relevant to heating these sheds.
Electric HS Loco Sheds (overhead power)
These sheds are primarily new facilities, in which case they are well insulated. Again due to the cleanliness within the sheds compared to diesels, there is no requirement for ducted air to the gas burners of the radiant heating system.
Unlike the previous types of locos, work has to be undertaken on top of the train to maintain the power unit. These sheds have personnel staging for access to the top of the trains. When designing a radiant heating system for such facilities, due regard of the staging has to be taken into account. The radiant emitter cannot be too close to the working area above the trains. The staging is normally in a defined location within the facility. This can result in a challenge for designers, but it is achievable given sufficient roof height within the facility. The ability to be able to zone the radiant heating is paramount in such instances.
Evidence of Success
Amongst other successful train maintenance shed applications, Reznor was able to provide the ideal heating solution for the National College for High Speed Rail at Doncaster. Radiant heat (Nor-Ray-Vac) was specified as the heating system for the Largescale Workshop, comprising an area of 1,906m2 within the facility.
• NRV system comprised 9 x 38LR burners arranged in 3 branches, suspended at 12m above finished floor level, with one discharge fan flue.
• Due to the type of operation within the facility, i.e. training of students throughout the floor area, the system is controlled as one zone.
• The NRV system produces blanket uniform heat coverage.
• Operating costs are minimised by concentrating the heat at low level, where it is most needed, without heating the volume of air in the building.
• Rapid response times mean warmth is felt by occupants within minutes of start-up and no fuel is wasted bringing the whole volume of air to a comfortable temperature.
• Since the Nor-Ray-Vac radiant system burns fuel at point of use, there are no distribution losses to take into account
The college is a flagship facility for apprentices, as well as trarining the existing workforce in new skills, meeting the need for more engineers and will therefore have a purpose beyond the timeframes of HS2.
Nick Winton is divisional manager for Reznor