Multiple benefits
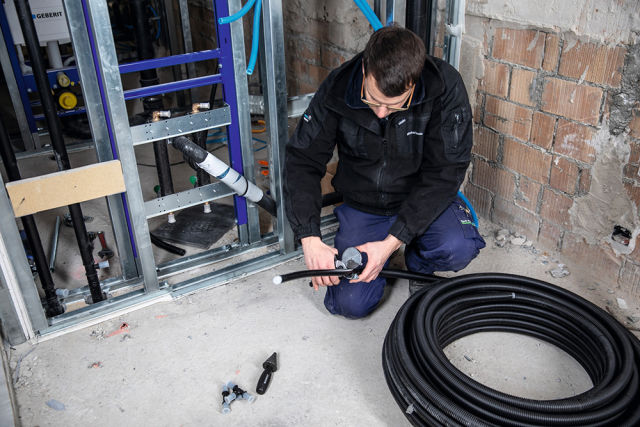
Antony Corbett explores the benefits of multi-layer piping as a solution for a wide range of project challenges.
The use of plastic piping for supply pipes has been steadily increasing over the last 10 to 15 years, as contractors exploit the benefits of flexible piping not only for underfloor heating but also potable water and general heating too. In addition to its bendable construction, single-skin plastic piping also offers the advantage of press-fit piping systems and flame-free pipe jointing in applications – although press-fit is not exclusive to plastic piping, of course.
However, there is another solution which is proving popular thanks to its unique combination of strength and stability (as with metal piping systems) alongside flexibility and corrosion resistance (like plastic), all with the added convenience of press-fit. This is multi-layer piping.
Flexible yet durable and an excellent complement to press-fit carbon steel within an overall building project, multi-layer piping systems consists of three layers. An outer plastic layer made of polyethylene (PE-RT of the second generation) which protects against corrosion and mechanical damage, a central aluminium layer which makes the pipe stable yet bendable, plus an inner layer, which is also made of PE-RT, for internal corrosion resistance.
The technology has been often reserved for industrial applications, but it also offers a single solution for all potable water and heating supplies on both domestic and light commercial projects. Here are five compelling reasons to consider multi-layer piping on your next project.
MULTI-PLAYER PIPING IN PRACTICE AT WHITMORE HIGH SCHOOL The benefits of multi-layer piping systems were demonstrated expertly during the construction of the new Whitmore High School, where the supply system, Geberit Mepla, was specified for the low temperature hot water and water services for the building. One of the key architectural features of the new school is the curvature of the building and the flexibility of the system enabled the piping to be bent to follow the line of the building. Simple and quick to install, being able to bend the lightweight piping system meant fewer fittings were needed and installation costs reduced when compared with conventional plastic or copper piping. Multi-layer systems also require around half of the flushing time of either a steel or soldered copper system, helping to tick the box for water saving as part of the school’s overall strategy to consider the environment during the construction and operation phases. |
Ultimately, multi-layer systems are about improving the strength and durability of the system when compared with plastic piping, without compromising on weight or portability as can be the case with copper.
The central-welded aluminium layer offers mechanical stability to ensure that the pipe remains in its required position yet remains flexible enough to bend. The aluminium layer also provides an oxygen barrier, making it suitable for use in central-heating systems and makes the pipe detectable by electronic devices after installation.
Thanks to the good bending capacity, multi-layer piping can be adjusted flexibly to the on-site conditions, even manipulated to follow the line of curved architectural features in modern buildings. Reduce the number of fittings required, saving time and money during installation, by bending 16mm and 20mm pipes effortlessly by hand. Larger diameters up to 50mm can also be bent without risk of de-lamination or kinking using an appropriate tool.
Even where fittings are required, press fitting offers quick, simple and reliable connections with no need for hot works, which would otherwise lead to additional mess on site, health and safety considerations and delays to allow for cool down when used for copper systems. The only tools needed to form a reliable, tight and durable connection are a cutter, deburrer and press tool, so joints can be easily.
As well as a lower insurance premium, the absence of a working flame also minimises the risk of damage to existing fittings and fixtures and the surrounding areas.
Crucially, multi-layer piping is suitable for cold water systems with no need for additional measures to prevent corrosion. The polyethylene inner layer is resistant to cracking, aging and general wear and tear, as well as being non-reactive and corrosion resistant, making it suitable for use in both plumbing and potable-water applications.
The inner layer also provides resistance to scale build-up, significantly enhancing the hygiene qualities of the pipe. The low internal surface roughness (7 µm) means it is more difficult for limescale and biofilm to adhere to the smooth surface and it also has excellent acoustic insulation properties, so water passing through the pipework produces much less noise than in metal piping.
![]() |
Fittings and pipes from leading manufacturers even come with protective caps for added hygienic safety when stored or during an installation break.
These benefits would be irrelevant of course if the piping was not reliable, but thanks to the unique construction of multi-layer piping, contractors and end users can have complete confidence in a permanently leak-proof system.
With multi-layer piping from reputable manufacturers, there is usually a fail-safe method of checking for unpressed joints. Unpressed fittings are designed to leak slightly during pressure testing (even at low water testing pressure), and any unpressed fittings can be pressed without having to drain down the entire system.
A must for all contractors working on light commercial and industrial projects, leading manufacturers offer pipes in a broad range of diameters to enable crucial consistency across larger construction projects, including new schools, hospitals and offices.
However, multi-layer piping is both versatile and economical – which makes it the perfect choice for a wide range of applications outside of plumbing and potable water. From compressed air and vacuum systems, to cooling equipment and process water systems, multi-layer piping offers high margin opportunities when working across a range of sectors including automotive, chemical, pharmaceutical and food processing.
Antony Corbett is product manager for Geberit