Good commissioning pays long term dividends

In previous articles, the CSA has discussed commissioning in some depth, covering aspects such as what commissioning is, why it is carried out, when is it done and who does it.
Of course, those articles concentrated on how to do it properly. Perhaps we should also discuss what the likely outcome is if that route is not followed?
It has long been the case that too many projects either do not allow enough time to commission a building or significantly underestimate the cost of doing so properly. Even worse, some projects squeeze both the time and cost elements.
The impression that CSA Members have is that there is still a tendency among developers to divorce the initial construction from ongoing maintenance when calculating the lifetime costs of a proposed project. That is an error in our view. Here is why.
Today, it is self-evident that energy consumption is a major element of the ongoing cost of operating a building. It therefore stands to reason that ensuring the building is set up to work in the most energy efficient way from the outset will have a significant impact on those costs. There is only one way to achieve that: Commission the building properly.
Ah, you say. Controlling the building space conditions efficiently is what the Building Management System (BMS) is for. Correct. Nevertheless, you need to consider how the BMS does that. Simply put, it does it by manipulating the heating, cooling and ventilation in such a way as to minimise the energy input required.
That’s fine, but the degree of that manipulation is finite. Dampers that modulate airflow and control valves that vary heating or cooling water flows, by definition, work best when asked to operate in the centre of their operating range. Talk to any experienced commissioning engineer and they will have tales of dampers struggling to manage airflow when almost completely closed – opening the damper by two or three degrees suddenly doubles the airflow. They’ve probably also come across control valves being fully open for most of the day, yet still not managing to achieve the correct space temperature because the flow of liquid is too low.
Such situations can only mean that the overall system is operating inefficiently and that means it is wasting energy. If that is how the systems in a building are set up from day one, can you imagine how much energy is wasted during the building’s life? It is also obvious that equipment operating at the extremes of its capability is likely to suffer more failures than might otherwise be expected.
That means increased maintenance costs. In extreme circumstances, equipment failure can lead to reducing or even stopping building operation.
Any measures that can be taken to eliminate those sorts of situation must have future benefits for both building owners and users. Developers should also recognise that building users are now savvy when it comes to evaluating how much the building they are being offered will cost to run.
So, as we said previously, the easy solution is to commission the building properly.
It really should be quite simple; it just needs a bit of forethought:
• Make sure there are enough measurement and regulation points embodied in the design of each system – orifice plates, regulating valves, volume control dampers. Also remember – just because the computer says system leg A is the index leg and will be fully open doesn’t mean it will be in practice.
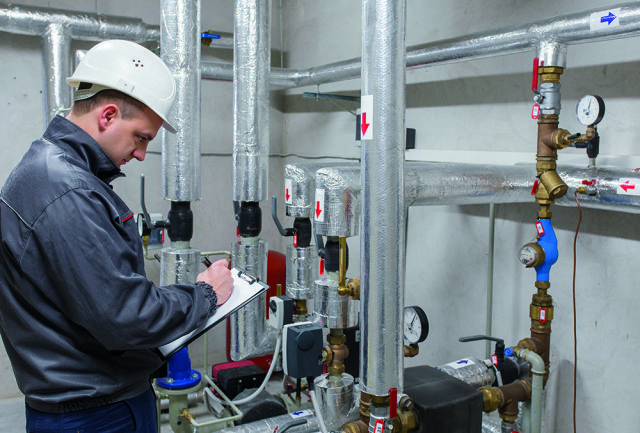
• Make sure there is suitable access to those measurement points – too often commissioning engineers go to jobs where the only piece of straight ductwork to measure the airflow is 15 feet up and above pipework, cable trays and the like.
• Monitor the installation as it progresses. Don’t let the installers miss out some of those measurement / regulation points just to save a few pounds. Make sure all those ‘little’ design changes are properly thought through so as not to affect the commissionability of the systems.
• Monitor the installation again, but this time to make sure it’s being installed properly. Are the flexible connections between fan and duct properly secured; are they aligned correctly? Can you get to the regulating damper handle or is it jammed against the wall?
• Ensure all the VCDs and fire dampers have been left fully open. Check that all the ductwork access hatches are properly fitted – and that there’s enough of them.
Most of the above points concern air systems, but there are similar ‘whoopsies’ on water systems.
Unfortunately, although it should be quite simple, all too often circumstances arise that make it anything but. Personnel change, things get said in passing that are not followed up, verbal agreements are made that never get put into writing, etc., etc.
Finally, we need to deal with the commissioning program. It always starts out with enough time to do the job properly. Why is it that everyone thinks you can just cut the time in half, or even by 75%, and still do the job just as properly? You can’t. You just end up with a building that is not commissioned correctly. Remember, every building, no matter how formulaic the design, has its own quirks and peculiarities. It thus needs to be treated as a prototype. Commissioning a prototype takes time. Please allow it.
The CSA viewpoint is that, if you employ one of our specialist member companies early enough, pay them a reasonable (i.e. fair) amount and give them enough time to do their job correctly, the result will be a much more efficient – and thus cheaper to run – building. What’s not to like about that?
If this article has whetted your appetite to find out more – and it really should have – make sure you come to the CSA seminar ‘Making Buildings Work’. It will be held at The Crystal in London’s Docklands on 31st March. Visit the csa-conference link below for details.
Picture credits: Shutterstock/Kaspars Grinvalds